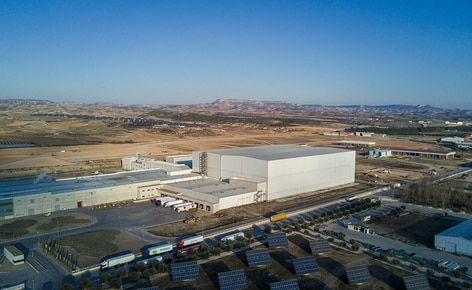
Mecalux towarzyszy firmie Congelados de Navarra w ciągłym rozwoju
Firma Congelados de Navarra magazynuje 146 000 palet w trzech chłodniach automatycznych
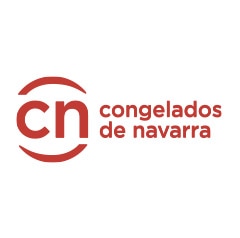
Firma Congelados de Navarra powstała w 1998 roku. Jest jednym z najmłodszych, a zarazem wiodących producentów mrożonek w Europie. Strategia firmy opiera się na stosowaniu innowacyjnych rozwiązań i technologii we wszystkich procesach produkcyjnych, dzięki czemu plasuje się w pierwszej dziesiątce europejskich przedsiębiorstw działających w tej branży. Mecalux towarzyszy rozwojowi i rozbudowie Congelados de Navarra od chwili powstania firmy, projektując i wdrażając optymalne rozwiązania logistyczne.
Historia firmy
Dynamiczny rozwój oraz sukces, jaki odniosła firma Congelados de Navarra w swojej branży, wynikają z przedsiębiorczości i wysiłku włożonego w jej rozwój przez jej założyciela, Benito Jiméneza. W 1998 roku zainicjował on budowę zakładu produkcyjnego zlokalizowanego w miejscowości Arguedas (Navarra).
Na początku centrum składało się z jednej mroźni wyposażonej w regały wjezdne. W momencie kiedy firma zanotowała znaczny wzrost sprzedaży, rozwiązanie to stało się niewystarczające. Niezbędna była inwestycja mająca na celu powiększenie magazynu oraz zautomatyzowanie go, a tym samym maksymalne zwiększenie wydajności wszystkich odbywających się w nim procesów.
Obecnie zakład w Arguedas składa się z dwóch całkowicie zautomatyzowanych mroźni, w których może być składowanych 12 700 palet. Dzięki automatyzacji pozwalającej osiągnąć wysoki poziom wydajności, w 2004 roku firma została nagrodzona prestiżową nagrodą przyznawaną największym europejskim producentom, przetwórcom i dystrybutorom produktów spożywczych.
W związku z dynamicznym rozwojem i perspektywą jego utrzymania w przyszłości w 2008 roku firma Congelados de Navarra otworzyła drugi zakład produkcyjny w miejscowości Fustiñana (w odległości zaledwie 24 km od pierwszej fabryki).
Centrum to stale się rozwija i jest adaptowane do wymogów firmy. Obecnie składa się z dwóch zautomatyzowanych mroźni zlokalizowanych w magazynie samonośnym o pojemności całkowitej wynoszącej 63 000 palet. W trakcie budowy jest trzecia mroźnia, w której będzie możliwe składowanie 83 000 palet.
W 2012 roku zostało otwarte biuro we Francji, co było pierwszym krokiem w kierunku ekspansji na arenie międzynarodowej. Obecnie firma ma również oddziały w Wielkiej Brytanii i Stanach Zjednoczonych. Eksportowane jest 70% całej produkcji. Utworzono sieć dystrybucyjną oraz sieć importerów, dzięki czemu produkty firmy są sprzedawane na całym świecie.
Współpraca pomiędzy firmą Mecalux a Congelados de Navarra
Współpraca pomiędzy firmami rozpoczęła się w 1998 roku, w chwili powstania Congelados de Navarra.
Dzięki współpracy z firmą Mecalux możliwe było zaplanowanie i wdrożenie nowych projektów wpływających na znaczne usprawnienie operacji logistycznych, które mają miejsce w magazynie Klienta, a co za tym idzie poprawę jego pozycji konkurencyjnej. Oto niektóre z przeprowadzonych inwestycji:
Arguedas
W 2000 roku Congelados de Navarra zlecił firmie Mecalux dostawę pierwszego automatycznego systemu magazynowego do mroźni istniejącej w zakładzie produkcyjnym w Arguedas. Zainstalowano system Pallet Shuttle z układnicą, a pojemność składowania wynosiła 3800 palet.
W 2004 roku została uruchomiona druga mroźnia automatyczna, oprócz magazynu samonośnego, tuż obok pierwszej mroźni. Mierzy 33 m wysokości i składa się z trzech korytarzy o podwójnej głębokości po obu stronach. Umożliwia składowanie 8900 palet.
Fustiñana
Firma Congelados de Navarra w 2008 roku otworzyła nowy zakład produkcyjny znajdujący się w miejscowości Fustiñana. Celem było utrzymanie tempa rozwoju przedsiębiorstwa oraz szybka obsługa klienta. Ten ambitny projekt został przeprowadzony w następujących etapach:
- Etap 1.
Mecalux buduje zautomatyzowany magazyn samonośny o wysokości 36 m, w którym możliwa jest praca poniżej -21 ºC. Magazyn składa się z 6 korytarzy z regałami o podwójnej głębokości, na których można składować 27 000 palet.
W zakładzie tym transport wewnętrzny pomiędzy poszczególnymi strefami produkcyjnymi a mroźnią jest zautomatyzowany. Odbywa się za pomocą układu przenośników rolkowych, wózków wahadłowych, podnośników i systemu wózków podwieszanych.
- Etap 2.
Pomiędzy 2010 i 2011 rokiem powstaje nowa mroźnia, przylegająca i zintegrowana z pierwszym obiektem oraz o podobnych parametrach. Umożliwia składowanie 36 000 palet rozmieszczonych w ośmiu korytarzach.
- Etap 3.
W 2015 roku firma Congelados de Navarra powiększa strefę zsypów. Ponownie projekt wraz z instalacją wszystkich urządzeń transportu wewnątrzzakładowego, które komunikują ten obszar z pozostałymi strefami produkcyjnymi oraz magazynami, jest powierzony firmie Mecalux.
- Etap 4.
Rok później zostaje nawiązana współpraca z firmą Mecalux, której celem jest wdrożenie odpowiedniego rozwiązania w związku z potencjalnym wzrostem produkcji Congelados de Navarra oraz wzmocnienia w ten sposób możliwości rozwoju firmy zarówno na poziomie produkcji, jak i pojemności składowania.
Zdecydowano się na budowę kolejnej mroźni do składowania półproduktów, która stała się uzupełnieniem dwóch poprzednich. Połączona została z istniejącą linią transportu wewnątrzzakładowego, umożliwiając przemieszczanie towaru w obu kierunkach.
Magazyn o wysokości 43 m i pojemności 83 000 palet jest ogromną konstrukcją, co w przypadku mroźni jest rzadkością. Dzięki zastosowaniu systemu Pallet Shuttle z układnicami możliwe jest przeprowadzenie dużej liczby operacji logistycznych.
Wydajna instalacja w Fustiñana
W centrum Fustiñana przetwarzana jest większość produktów firmy Congelados de Navarra. Żywność przechodzi przez szereg procesów, w większości zautomatyzowanych, celem zapewnienia najwyższej jakości przy jednoczesnym zachowaniu odpowiednich wartości odżywczych smaku oraz walorów estetycznych.
Wyjście z produkcji
Instalacja Mecalux rozpoczyna się od przejścia towaru przez tunel zamrażalniczy. Kanały utworzone z przenośników rolkowych umieszczone zostały tuż pod liniami do klasyfikacji. Puste opakowania (duże kartonowe i plastikowe ośmiokątne pojemniki na produkty luzem) transportowane są do strefy zsypów, gdzie umieszczane są w nich produkty.
Następnie wózek wahadłowy przenosi palety do wind, które transportują je na górną kondygnację, gdzie automatyczne owijarki zamykają opakowania, zabezpieczając produkt.
Palety po przejściu kontroli transportowane są przez system wózków podwieszanych do mrożni lub innych stref produkcji.
Projekt tego systemu transportu umożliwia rozmieszczenie niezbędnych wózków w każdym punkcie poprzez dynamiczne przypisanie. Ponadto dzięki możliwości skracania trasy nie każdy wózek musi pokonywać wszystkie jej odcinki.
Przyjęcia do mroźni
Palety przed wejściem do magazynu przechodzą przez system śluzy bezpieczeństwa SAS (Security Airlock System), który tworzy wstępną komorę. System ten utworzony jest z dwóch par drzwi – jednych do mroźni i drugich na zewnątrz – które nigdy nie są jednocześnie otwierane. Celem SAS jest uniknięcie gwałtownych skoków temperatury, skraplania i utraty zimna. Zainstalowany został on również przy wydawaniu palet do stref przetwarzania.
Mroźnie mają dwa poziomy komunikacyjne, na których znajdują się dwie linie przenośników: do przyjęć i do wydań.
Na górnej kondygnacji realizowane są przyjęcia towaru z produkcji oraz wydania palet, które kierowane są do strefy przetwarzania (pakowanie i mieszanie).
Na dolnej natomiast przeprowadzane są przyjęcia towaru z zewnątrz oraz wysyłki.
Charakterystyka mroźni
Dwie połączone mroźnie mają długość 140 m, szerokość 103 m oraz wysokość 35 m.
Łącznie w mroźniach znajduje się 14 korytarzy z regałami o podwójnej głębokości po każdej stronie, a pojemność składowania wynosi 63 000 palet.
Jest to magazyn samonośny, w którym regały utrzymują ciężar własny, okładziny ścian i dachu oraz składowanych artykułów. W górnej części regałów znajdują się wiązary dachowe, gdzie umieszczono urządzenia chłodnicze. Dzięki temu zapewniony jest stały przepływ powietrza oraz równomierne rozłożenie temperatury w całej instalacji.
W każdym korytarzu układnice dwukolumnowe przenoszą palety pomiędzy przenośnikami wejścia i wyjścia a miejscami na regale, jakie zostały przypisane przez system zarządzania magazynami Easy WMS firmy Mecalux zgodnie z wcześniej ustalonymi regułami.
W górnej części mroźni zaprojektowano pomosty i podesty do przeprowadzania prac konserwacyjnych urządzeń chłodniczych oraz układnic. Dostęp do nich znajduje się z zewnątrz magazynu.
Niższy poziom mroźni
Miejsce, z którego produkty przechodzą do strefy wysyłek, znajduje się poniżej poziomu mroźni. Pętla przenośników łączy korytarze z drzwiami prowadzącymi do komór wstępnych. W tych komorach składowane są palety oczekujące na załadunek do ciężarówek.
W komorze wstępnej, w której utrzymywana jest stała temperatura, segregowane są produkty należące do jednego zamówienia lub do tej samej ścieżki. Pozwala to na usprawnienie załadunku do ciężarówek. Komory te mieszczą 500 gotowych do wysyłki palet.
Komorę wstępną od strefy załadunku dzielą 3 systemy śluz bezpieczeństwa. Po przekroczeniu śluz palety wprowadzane są przez operatorów do ciężarówek.
W tej samej strefie znajdują się stanowiska przeznaczone do składowania produktów pochodzących spoza centrum produkcyjnego. Palety niespełniające kryteriów jakościowych składowane są na palecie bazowej. Paleta ta może mieć następujące wymiary: 800 x 1200 mm lub 1000 x 1200 mm.
Strefa mieszania i pakowania
Produkty skierowane do strefy przetwarzania przechodzą z komór przez górny poziom, po czym odbierane zostają przez system transportu podwieszanego.
Strefa przetwarzania znajduje się nieco wyżej w stosunku do pętli przenośników, dlatego też ta część magazynu została wyposażona w podnośniki. Tam też znajdują się leje zasypowe, w których dochodzi do mieszania produktów, a następnie ich pakowania
Po zakończeniu procesów przetwarzania palety są opuszczane za pomocą podnośników, a następnie za pośrednictwem systemu transportu podwieszanego trafiają do kolejnego miejsca docelowego.
Kierowanie opakowań na produkcję
Kierowanie pustych opakowań na produkcję jest kwestią kluczową dla poprawnego działania centrum produkcyjnego. Proces ten jest również zautomatyzowany.
Opakowania są przystosowywane w przeznaczonej do tego celu strefie: umieszczane na paletach, wykładane plastikowym workiem, dzięki czemu mrożone produkty nie mają kontaktu z kartonem, i oznaczane kodem RFID.
Opakowania przenoszone są za pomocą dwóch podnośników na poziom komunikacyjny, po czym za pomocą systemu wózków podwieszanych są transportowane do miejsc docelowych.
System transportu podwieszanego
System transportu podwieszanego jest najważniejszym punktem instalacji. Od niego zależne jest przemieszczanie się ładunków między wszystkimi strefami centrum produkcyjnego.
Wózki poruszają się wzdłuż podwieszanych pod sufitem szyn, z których dociera do nich energia zasilająca. Służą one także do przesyłania danych pozwalających na określenie położenia wózków w pętli. Sprawne działanie całego sytemu zapewniają liczne rozgałęzienia, skróty, strefy konserwacji oraz wózki oczekujące.
Wózki zapewniają sprawną obsługę oraz gwarantują nieprzerwany przepływ towaru. System ten stanowi optymalne rozwiązanie dla firm sektora spożywczego, do których należy Congelados de Navarra, ponieważ zdecydowanie ułatwia dotrzymanie wysokich wymogów higienicznych charakterystycznych dla tej branży.
Easy WMS – centrum systemu
Optymalne zarządzanie logistyczne
Oprogramowanie magazynowe opracowane przez firmę Mecalux zarządza wszystkimi procesami zachodzącymi wewnątrz instalacji, takimi jak: wejście towaru pochodzącego z produkcji lub z zewnątrz, przypisanie odpowiedniej lokalizacji, kontrola stanu magazynowego, składowanie i odbiór towarów, kierowanie palet do stref przetwarzania.
Easy WMS firmy Mecalux dba o terminowość i dokładność wszystkich operacji, które mają miejsce w magazynie, zapewniając ciągłość procesów zachodzących w strefie wyjścia z produkcji.
Dostarczanie ładunków do właściwych lokalizacji oparte jest na z góry określonych regułach oraz algorytmach, w których brane są pod uwagę cechy produktów oraz kryterium rotacji. Reguły, na których opiera się klasyfikacja stanu magazynowego w 14 korytarzach mroźni, konfigurowane są w oprogramowaniu Easy WMS. W oparciu o przyjęte normy produkty luzem znajdują się jak najbliżej strefy mieszania i pakowania, natomiast produkty gotowe znajdują się jak najbliżej strefy wysyłek.
System ERP Klienta, Oracle JD Edwards, odpowiedzialny jest za kontrolę zapotrzebowania strefy pakowania na produkty luzem. Easy WMS firmy Mecalux oblicza liczbę potrzebnych opakowań, a następnie wysyła je do miejsca docelowego zgodnie z ustalonymi regułami. System WMS przetwarza w ten sam sposób zamówienia kierowane do strefy mieszania i te kierowane do strefy pakowania.
Wysyłki odbywają się transportem drogowym. WMS generuje polecenia odbioru zamówień z określonych lokalizacji, po czym wysyła polecenie umieszczenia wybranych produktów w komorach wstępnych, gdzie palety oczekują na wprowadzenie do doków przeładunkowych. W momencie gdy do załadunku podstawiona zostaje ciężarówka, wydanie palet odbywa się w sposób automatyczny, a Easy WMS wskazuje operatorowi, do którego doku należy skierować poszczególny ładunek.
Komunikacja między systemami
Easy WMS pozostaje w stałej komunikacji z systemem zarządzającym produkcją MES oraz z centralnym systemem zarządzającym ERP, zapewniając tym samym prawidłowe funkcjonowanie magazynu Congelados de Navarra.
System MES przekazuje informacje do Easy WMS odnośnie każdego wyprodukowanego produktu, który będzie składowany w magazynie.
Towary przychodzące z pozostałych centrów logistycznych Klienta są rejestrowane za pośrednictwem ERP. System zarządza również procesem pakowania i wysyłki produktów składowanych luzem.
Galileo
Magazyn Congelados de Navarra posiada wiele zróżnicowanych rozwiązań automatycznych, które optymalizują jego pracę. Moduł sterujący Galileo firmy Mecalux zapewnia prawidłową pracę wszystkich urządzeń elektromechanicznych, które realizują czynności magazynowe w zakresie transportu i manipulacji ładunkami.
Zadaniem modułu Galileo jest: sterowanie ruchem urządzeń mechanicznych (układnic, przenośników, wózków podwieszanych itp.), kontrola urządzeń automatycznej identyfikacji (skanery, czytniki RFID itp.) oraz rejestracja ewentualnych błędów czy wypadków. Ponadto system Galileo jest zintegrowany z oprogramowaniem magazynowym Easy WMS.
Dodatkowo zastosowanie systemu informatycznego SCADA umożliwia stały nadzór nad przebiegiem wszystkich procesów technologicznych w obiekcie, w ramach których są gromadzone i przedstawiane niezbędne dane.
Rozbudowa
Centrum produkcyjne zostało zorganizowane w sposób, który umożliwia jego ewentualną rozbudowę o dodatkowe pomieszczenia chłodnicze, w zależności od potrzeb rynkowych i celów przedsiębiorstwa.
Easy WMS to uniwersalne i elastyczne oprogramowanie magazynowe, które można modyfikować oraz rozbudowywać o dodatkowe moduły w miarę zmieniających się potrzeb przedsiębiorstwa.
Aby zagwarantować poprawne funkcjonowanie nowo wybudowanej chłodni, system Easy WMS zostanie rozbudowany o dodatkowy moduł umożliwiający obsługę automatycznego systemu Pallet Shuttle z wózkami wahadłowymi.
Wizja przyszłości
Benito Jiménez, założyciel Congelados de Navarra, zdecydował się zautomatyzować wszystkie procesy zachodzące w magazynie – począwszy od produkcji, a skończywszy na składowaniu. Proces ten obejmował również włączenie automatycznych rozwiązań do wewnątrzzakładowego systemu transportu ładunków i komunikacji między poszczególnymi strefami.
Optymalizacja pojemności składowania, ograniczenie liczby personelu oraz efektywna wydajność to niektóre z wielu korzyści, jakie uzyskała firma Congelados de Navarra dzięki automatyzacji swoich centrów produkcyjnych w Arguedas i Fustiñana.
Firma Mecalux była zaangażowana w realizację wielu projektów Congelados de Navarra. Jej doświadczenie i zaangażowanie pozwoliły zaprojektować indywidualne rozwiązania magazynowe, które w efektywny sposób zaspokoiły wszelkie potrzeby logistyczne Klienta. Wynikiem tej współpracy było powstanie w miejscowości Fustiñana jednego z najnowocześniejszych i najbardziej rozwiniętych technologicznie centrów logistycznych w Europie.
Galeria
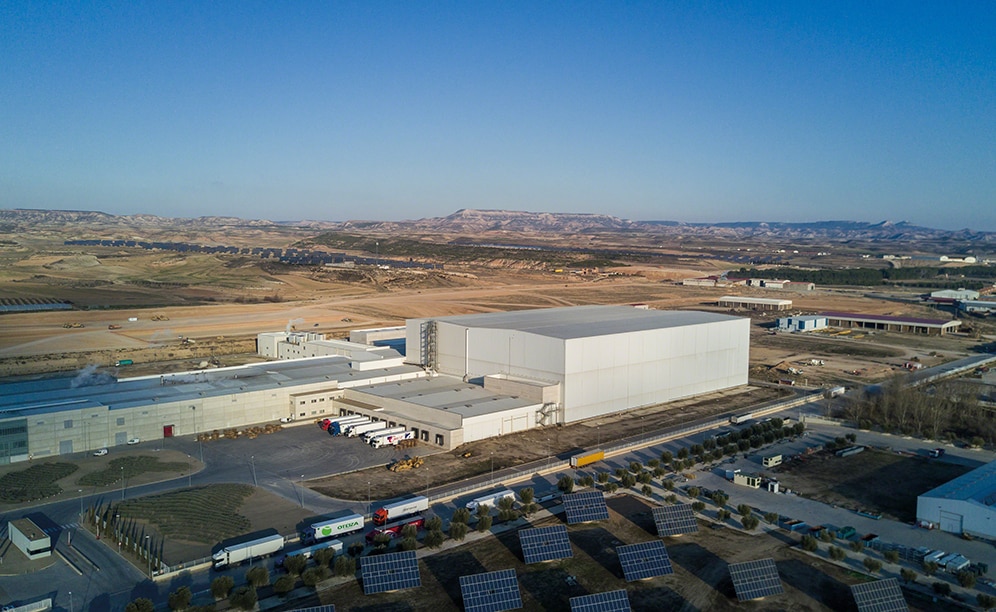
Zapytaj eksperta