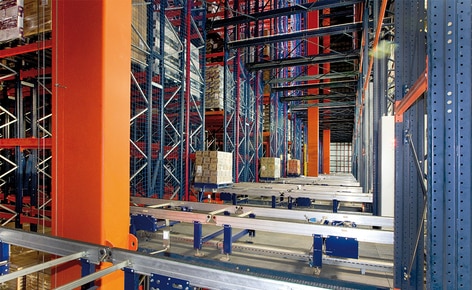
Znaczne zwiększenie pojemności oraz wydajności magazynu Grupo Siro – firmy z sektora spożywczego – dzięki budowie samonośnego automatycznego magazynu o wysokości 35,5 m
Automatyczny magazyn samonośny, który zabezpiecza obecne i przyszłe potrzeby firmy Grupo Siro
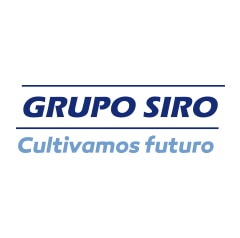
Mecalux dostarczył firmie Grupo Siro, jednemu z największych przędsiębiorstw w sektorze spożywczym w Hiszpanii, automatyczny magazyn samonośny. To innowacyjne centrum logistyczne o wyjątkowo imponujących rozmiarach wykorzystuje najnowsze technologie, dzięki czemu jest wydajnym rozwiązaniem magazynowym z dużym potencjałem.
Historia Grupo Siro
Grupo Siro jest jednym z wiodących producentów ciastek, makaronów, chleba tostowego, wyrobów piekarniczych i zbożowych na rynku hiszpańskim.
Firma powstała w 1991 roku, gdy Galletas Siro rozpoczęło współpracę z Danone. Od tej pory firma stawia na ciągły rozwój, stosując najnowsze technologie we wszystkich procesach i oferując w najlepszej cenie doskonałej jakości artykuły w najlepszej cenie.
Obecnie Grupo Siro produkuje ponad 300 różnych produktów. Dysponuje 13 zakładami produkcyjnymi, magazynem logistycznym, centrum badań, rozwoju i innowacji technologicznej, centrum kontroli półproduktów oraz dwoma biurowcami. Przedsiębiorstwo utworzyło także fundację Grupo Siro.
Zapotrzebowanie klienta
Ze względu na ogromne zapotrzebowanie swojego głównego klienta – sieci marketów Mercadona – w ostatnich latach firma bardzo się rozwinęła.
W pewnym momencie wzrost produkcji związany ze wzrostem popytu na produkty firmy wymusiły zwiększenie powierzchni magazynów, które znajdują się głównie wewnątrz fabryk. Aby utrzymać rytm produkcji, początkowo firma zdecydowała się na wynajem magazynów zewnętrznych, ale to utrudniało koordynację łańcucha logistycznego i powodowało wzrost kosztów operacyjnych.
Poszukując skutecznych rozwiązań odpowiadających zapotrzebowaniu Grupo Siro, zdecydowano o konieczności budowy nowego centrum logistycznego z siedzibą w Venta de Baños (Palencja). Zadanie to zostało powierzone firmie Mecalux. Budowie przyświecały dwie przesłanki: powiększenie pojemności magazynowej zakładów produkcyjnych oraz zwiększenie wydajności firmy.
Zaproponowane rozwiązanie
Dział techniczny firmy Mecalux we współpracy z działem logistycznym Grupo Siro przeanalizował szczegółowo zapotrzebowanie, ograniczenia oraz możliwości i zaoferował optymalne rozwiązanie – budowę samonośnego magazynu o wysokości 36 m, który będzie obsługiwany przez układnice i przenośniki oraz zarządzany przez oprogramowanie magazynowe Easy WMS firmy Mecalux.
Centrum logistyczne jest strategicznie zlokalizowane w zasięgu 3 km od czterech głównych zakładów produkcyjnych i mniej niż 100 km od pozostałych trzech, co znacznie ułatwia transport pomiędzy poszczególnymi jednostkami.
Przepływ ładunków jest stały i bardzo natężony, dlatego magazyn został wyposażony w dwie rampy odbiorcze znajdujące się z boku magazynu. Oddzielono je od dziewięciu ramp załadowczych, aby nie zakłócać tych dwóch procesów, ruchu w magazynie związanego z transportem oraz postoju ciężarówek.
Budynek przylegający do magazynu składa się z parteru i pierwszego piętra, co zapewnia optymalną organizację operacji wykonywanych na każdym poziomie.
- Na dolnym piętrze odbywa się odbiór i wysyłka towarów. Tutaj również jest wydzielona szeroka strefa, w której na posadzce odbywa się przeładunek.
- Na górnym piętrze są wprowadzane do magazynu palety pochodzące z ramp znajdujących się na parterze. Tutaj również znajduje się stanowisko do kompletacji ładunków.
Magazyn
Magazyn ma 102 m długości, 57 m szerokości i 35,5 m wysokości (maksymalne wymiary dozwolone przez lokalne przepisy budowlane). Wewnątrz magazynu znajduje się osiem korytarzy z regałami podwójnej głębokości po obydwu stronach, każdy z 14 poziomami ładunkowymi różnej wysokości dostosowanej do wymiarów palet stosowanych w firmie Grupo Siro. Jest to pięć poziomów o wysokości 1400 mm na europalety, osiem o wysokości 2000 mm i jeden o wysokości 2500 mm. Średni ciężar jednostek ładunkowych wynosi 800 kg, natomiast maksymalny 1000 kg.
Każdy korytarz jest wyposażony w dwukolumnową układnicę z teleskopowymi widłami oraz kabinę serwisową znajdującą się na wózku podnoszącym. Urządzenie to odkłada palety na odpowiednie miejsce, które zostaje wyznaczone w zależności od ich rozmiaru i rotacji.
Automatyczną część magazynu stanowią również dwa układy przenośników. Jeden na parterze, tam są odkładane palety przeznaczone do wysyłki, i drugi na pierwszym piętrze, na wysokości 6,7 m. Łączy on wszystkie wejścia i wyjścia palet ze strefą kompletacji.
W górnej części magazynu pomiędzy wiązarami dachowymi zostały zainstalowane przewody klimatyzacyjne, które regulują temperaturę w całej instalacji i rozprowadzają powietrze.
Na zewnątrz budynku w tylnej części zostały umieszczone cztery urządzenia pompujące systemu przeciwpożarowego oraz zbiornik z wodą o pojemności dostosowanej do rozmiarów magazynu. Wewnątrz znajdują się zraszacze i czujniki, dzięki czemu jest eliminowane ryzyko pożaru.
Parter
Rozmieszczenie stref na parterze:
- Automatyczna rampa rozładowcza.
- Tradycyjna rampa rozładowcza.
- Rampa załadowcza (łącznie 9).
- Strefa kontroli wejść palet oraz podnośnik.
- Wyjścia palet z magazynu.
- Przeładunek na posadzce.
- Wytyczona trasa wózków LGV.
- Akumulacja pustych palet.
- Odbiór i przystosowanie palet wchodzących.
Wprowadzanie towaru
Wprowadzenie towarów pochodzących z kilku najbliższych centrów produkcyjnych odbywa się na rampach odbiorczych. Na jednej rampie ciężarówki są automatycznie rozładowywane, na drugiej rozładunek odbywa się przy pomocy wózków widłowych lub ręcznych wózków paletowych.
Strefa rozładunku może pomieścić towar z dwóch pełnych ciężarówek, tj. 66 palet. Te następnie są kierowane do strefy kontroli, w której jest oceniany ich stan.
Wszystkie palety obowiązkowo przechodzą przez strefę kontroli, gdzie sprawdzane jest, czy ich stan, waga i wymiary odpowiadają wymogom jakościowym w magazynie. Jeśli parametry palety są właściwe, system kontroli pozwala jej na przejście w stronę podnośnika, który przeniesie ją piętro wyżej, gdzie zostanie wprowadzona do automatycznego magazynu. Jeśli paleta nie przejdzie przez stanowisko kontroli, jest kierowana do jednej z trzech stref w zależności od wykrytego błędu. Są to:
- Stanowisko korygowania ładunku.
- Stanowisko z urządzeniem pionizującym, na którym są poprawiane występy, które przekraczają przewidziane limity.
- Stanowisko z urządzeniem do składowania palet na paletach bazowych: kiedy jednostki ładunkowe są ułożone na nośniku nieodpowiedniej jakości, wówczas na tym stanowisku umieszczane są pod nimi prawidłowe palety. Ładunki te wracają do strefy kontroli i są ponownie sprawdzane przed wysyłką na górne piętro.
Jeśli palety nie można naprawić, jest ona transportowana do strefy wyjścia i jest wyrzucana z układu przenośników.
Palety, które zostały naprawione, wracają na stanowisko kontroli i są ponownie sprawdzane, czy spełniają wymagania magazynu.
Zagwarantowanie dobrego stanu towarów wprowadzanych do automatycznego magazynu jest niezbędne, dlatego należy sprawdzić, czy towar nie wystaje więcej, niż jest to dozwolone.
Wyjścia z magazynu / Wysyłki
Wózki sterowane laserowo (LGV), przemieszczając się wzdłuż zaprogramowanej trasy, obsługują palety wychodzące z magazynu, pobierając je z punktów wyjścia w każdym korytarzu i przenosząc do strefy palet oczekujących na załadunek wyznaczonej w jednej z dziewięciu ramp.
Wózki odczytują swoją trasę, wysyłając sygnał laserowy, który odbija się od lusterek umieszczonych przy trasie. System magazynowy dokładnie zna pozycję wózka i w momencie niskiego poziomu naładowania akumulatorów wydaje wózkowi polecenie kierowania się w stronę stacji ładującej. Jest to proces całkowicie zautomatyzowany i nie wymaga on interwencji operatora.
Jedynie załadunek ciężarówek wykonują operatorzy. Przy pomocy ręcznych wózków paletowych wprowadzają towary do pojazdów wyznaczonych przez oprogramowanie magazynowe w zależności od numeru zamówienia, trasy, klienta itp.
Za pomocą terminalu radiowego operator zatwierdza każdą operację i potwierdza wykonane zlecenie.
Pierwsze piętro
Wejście do magazynu
Towar pochodzący z ramp odbiorczych po przejściu przez stanowisko kontroli jest wysyłany na pierwsze piętro za pomocą podnośnika. Wówczas główny przenośnik rozprowadza jednostki ładunkowe do poszczególnych przenośników, które prowadzą do różnych korytarzy magazynowych. Układ przenośników porusza się w jedną stronę. Po nim również przemieszczają się palety, które wychodzą z korytarzy i są kierowane w stronę stref kompletacji.
Rozmieszczenie stref na pierwszym piętrze:
- Podnośnik.
- Przenośniki do transportu wewnętrznego.
- Przenośniki na wejściu lub wyjściu każdego korytarza.
- Wózek wahadłowy strefy kompletacji.
- Stanowiska kompletacji.
- Strefa z owijarką i stanowiskiem korekty.
- Główny przenośnik na wejściu do magazynu.
Strefa kompletacji
W magazynie utworzono dwa połączone stanowiska kompletacji, na których operator może przygotowywać dwa zamówienia jednocześnie. Gdyby wymagało tego zapotrzebowanie firmy Grupo Siro, strefę tę w przyszłości można rozbudować.
Stanowiska kompletacji znajdują się na przenośnikach. Po obu stronach operatora umieszczone są hydrauliczne stoły podnośnikowe, które zapewniają ergonomiczną pozycję podczas obsługi ładunku. Dzięki temu przygotowanie zamówień odbywa się w dużo bardziej sprawny sposób.
Każde stanowisko kompletacji jest wyposażone w strefę akumulacji. Zainstalowano sztaplarki i podajniki palet oraz przystosowano strefę buforową palet, które wyszły z magazynu i nie mają wolnego przyporządkowanego miejsca na przenośniku.
Po kompletacji zamówienia paleta jest włączana do układu przenośników i po przejściu przez stanowisko z owijarką ponownie jest wprowadzana do magazynu, w którym jest składowana do momentu, aż system nie wyda polecenia wysyłki.
Oprogramowanie
Magazyn jest zarządzany za pomocą oprogramowania Easy WMS firmy Mecalux. Oprogramowanie to stale komunikuje się z systemem ERP Grupo Siro celem kontrolowania, koordynowania i informowania o wszystkich procesach logistycznych, które odbywają się wewnątrz magazynu.
Oprogramowanie magazynowe pełni następujące funkcje:
- Kompleksowe zarządzanie procesami realizowanymi w magazynie.
- Zarządzanie wejściami i wyjściami towarów znajdujących się w rampach załadowczych i rozładowczych.
- Strategiczne umieszczanie jednostek ładunkowych w odpowiednich miejscach na regale.
- Kontrola stanu magazynowego w czasie rzeczywistym.
- Zaprogramowanie zlecenia wyjścia towaru i jego późniejszego załadunku na ciężarówkę za pomocą terminala radiowego.
- Optymalna organizacja pracy w zależności od etapu kompletacji.
- Bezpośredni kontakt z firmą logistyczną Grupo Siro.
- Zarządzanie wszystkimi głównymi danymi (artykuły, właściciele, dostawcy, klienci itp.).
Korzyści dla Klienta:
- Oszczędność kosztów operacyjnych: wyeliminowanie magazynów zewnętrznych oraz centralizacja operacji wykonywanych w centrum logistycznym przyczyniają się do wzrostu wydajności i szybkiego zwrotu z inwestycji.
- Maksymalna pojemność: duża wysokość magazynu oraz zastosowanie układnic pozwoliło na zwiększenie powierzchni magazynowej Grupo Siro stosownie do wzrostu produkcji.
- Całkowicie zautomatyzowane zarządzanie magazynem: wszystkie operacje związane z przyjęciem, magazynowaniem, kompletacją i wysyłką artykułów w firmie Grupo Siro są zarządzane przez oprogramowanie magazynowe Easy WMS, dzięki czemu zwiększona jest wydajność całego łańcucha logistycznego.
- Wzrost bezpieczeństwa: automatyczne magazyny zapewniają maksymalną ochronę operatorów i artykułów, co przekłada się na wydajność procesów odbywających się w magazynie i bezpieczeństwo personelu.
Automatyczny magazyn samonośny dla Grupo Siro | |
---|---|
Pojemność magazynowa: | 40 320 palet |
Wymiary palet: | 800 x 1200 x 1400 / 2000 / 2500 mm |
Maksymalny ciężar palet: | 1000 kg |
Liczba regałów podwójnej głębokości: | 16 |
Liczba korytarzy: | 8 |
Liczba układnic: | 8 |
Liczba poziomów ładunkowych: | 14 |
Długość magazynu: | 101 m |
Szerokość magazynu: | 57 m |
Wysokość magazynu: | 33,5 m |
Galeria
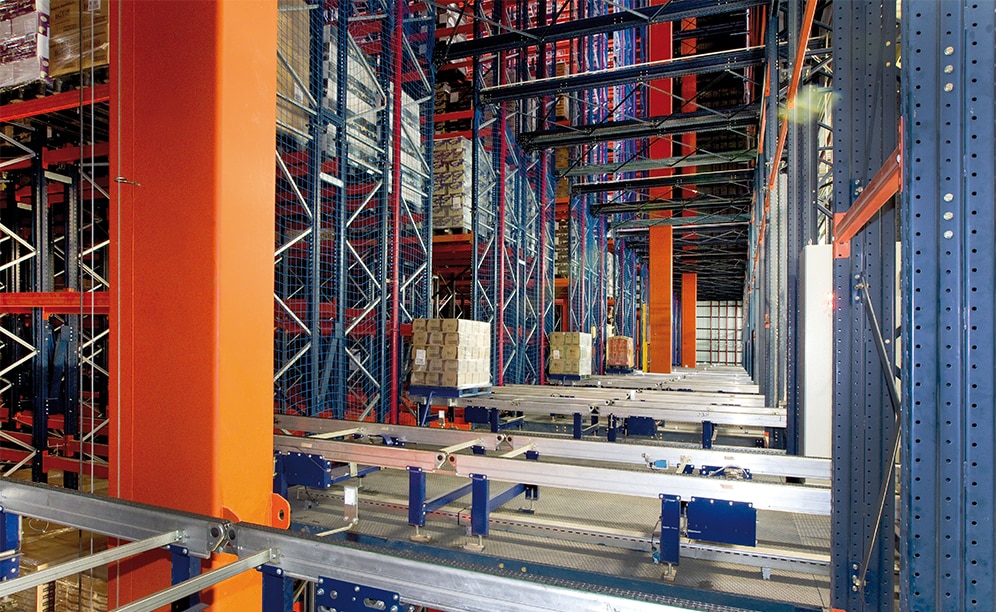
Zapytaj eksperta