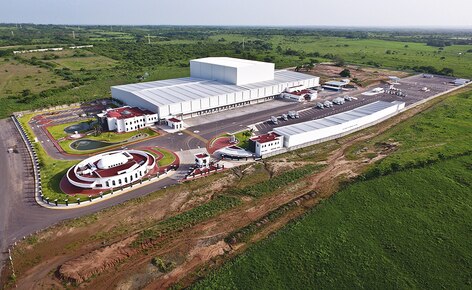
Osiem rozwiązań magazynowych optymalizuje dystrybucję produktów szybkozbywalnych w DECASA
DECASA, wiodący dystrybutor produktów szybkozbywalnych w Meksyku, buduje centrum logistyczne z systemami, które usprawnią proces przygotowywania zamówień
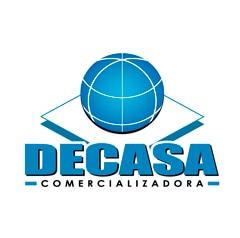
Centrum logistyczne DECASA w meksykańskim stanie Veracruz łączy w sobie kilka rozwiązań, między innymi automatyczny magazyn samonośny, półautomatyczny system Pallet Shuttle, antresole kompletacyjne do produktów na paletach i w kartonach oraz sortownię. W obiekcie, którego pojemność przekracza 36 500 palet, został również wdrożony informatyczny system zarządzania magazynem Easy WMS i program sterujący urządzeniami transportu bliskiego Galileo.
O firmie DECASA
W ostatnich latach DECASA notuje wzrost, który sprawił, że stała się najważniejszym w Meksyku dystrybutorem produktów szybkozbywalnych, osiągając 80% udziału w krajowym rynku.
Powstała w 1980 roku DECASA zawdzięcza swój sukces utalentowanym pracownikom, najnowocześniejszej technologii oraz najbardziej rozbudowanej infrastrukturze magazynowo-dystrybucyjnej w tej branży. Obecnie posiada w swojej ofercie 7000 produktów należących do kilku kategorii: artykuły spożywcze, chemia gospodarcza, środki pielęgnacji i higieny osobistej, karmy dla zwierząt, artykuły papiernicze, wina i słodycze.
DECASA współpracuje z ponad 350 dostawcami i zatrudnia 2700 pracowników, a jej obroty rosną niemal z dnia na dzień. Z sześciu centrów dystrybucyjnych zlokalizowanych w głównych meksykańskich ośrodkach handlowych (Veracruz, Puebla, Guadalajara, Torreón, Aguascalientes i Cortazar) wysyła ponad pięć milionów przesyłek miesięcznie, spośród których 90% trafia do odbiorców w ciągu 24 godzin od złożenia zamówienia.
DECASA prowadzi działalność również w innych formatach biznesowych, takich jak punkty samoobsługowe dla odbiorców końcowych oraz hurtownie dla detalistów typu cash and carry.
Potrzeby Klienta
DECASA potrzebowała nowego magazynu, który umożliwiałby zarówno składowanie szerokiego asortymentu różnorodnych produktów, jak i przygotowywanie zamówień.
Wychodząc naprzeciw tym potrzebom, Mecalux zaprojektował i dostarczył rozwiązanie składające się z kilku różnych systemów magazynowych dostosowanych do specyfiki i wymogów Klienta. Centrum logistyczne o powierzchni 22 000 m2 powstało w 200-hektarowym parku przemysłowo-handlowym Santa Rita zlokalizowanym w stanie Veracruz.
Projekt obiektu uwzględnia perspektywy rozwoju firmy, dlatego przewidziano w nim możliwość rozbudowy.
Rozwiązanie dostarczone przez Mecalux: osiem w jednym
Od samego początku Mecalux ściśle współpracował przy tym projekcie z osobami i podmiotami odpowiedzialnymi za budowę obiektu oraz dyrekcją ds. logistyki Klienta, aby znaleźć rozwiązanie najlepiej dopasowane do jego potrzeb. Rezultatem tej współpracy jest magazyn łączący różne systemy, w którym znalazło się osiem stref:
- Strefy 1 i 2: strefa składowania palet w stosach i strefa przeznaczona pod przyszłą rozbudowę. Palety z produktami o dużych rozmiarach są składowane jedna na drugiej na posadzce magazynu. Natomiast strefa o powierzchni 2000 m2 jest przeznaczona pod przyszłą rozbudowę w razie konieczności zwiększenia pojemności magazynowej.
- Strefa 3: automatyczny magazyn samonośny. Znajduje się w nim osiem korytarzy z regałami o podwójnej głębokości, które umożliwiają składowanie na łącznej powierzchni 4610 m2 ponad 28 000 palet – głównie zawierających produkty, które DECASA nabywa od swoich dostawców.
- Strefa 4: system Pallet Shuttle. Na podeście znajdującym się naprzeciw ramp zostały zamontowane dwa poziomy regałów do składowania akumulacyjnego z półautomatycznym systemem Pallet Shuttle, które mieszczą 512 palet z produktami lekkimi i dużymi.
- Strefa 5: antresole do przygotowywania zamówień. W tej strefie znajdują się trzy pięciokondygnacyjne bloki regałów z pomostami: na trzech kondygnacjach odbywa się kompletacja zamówień, pozostałe dwie kondygnacje zaś służą do składowania zapasu produktów. Aby przygotować zamówienia, operatorzy umieszczają produkty na przenośnikach biegnących przez środek każdej kondygnacji.
- Strefa 6: regały paletowe. Tutaj odbywa się kompletacja produktów o mniejszej rotacji i składowany jest ich zapas.
- Strefa 7: sortownia. Głównym wyposażeniem tej strefy jest system przenośników łączący antresole kompletacyjne z ogromnym sortownikiem, który wychodzi na rampy załadunkowo-rozładunkowe.
- Strefa 8: rampy załadunkowo-rozładunkowe. Przed sortownikiem i magazynem półautomatycznym znajdują się rampy z 11 stanowiskami załadunkowymi i 10 stanowiskami rozładunkowymi.
Opis poszczególnych rozwiązań
Automatyczny magazyn samonośny
Na powierzchni 4610 m2 powstał automatyczny magazyn samonośny o wysokości ok. 30 m, który mieści ponad 28 000 palet o wymiarach 1000 x 1200 mm i maksymalnej wadze 1300 kg. Składowane są tutaj produkty dostarczone przez dostawców.
Po obu stronach ośmiu korytarzy mierzących 68 m długości zostały zamontowane regały o podwójnej głębokości i 14 poziomach ładunkowych. Zaletą regałów o podwójnej głębokości jest duża pojemność magazynowa.
Dwie układnice przenoszą towary z przedniej części magazynu do odpowiednich miejsc na regałach, natomiast wózek wahadłowy stanowi łącznik między korytarzami oraz stanowiskami przyjęć i wydań towarów.
Automatyczne układnice zwiększają wydajność magazynu, pozwalają zmniejszyć zasoby potrzebne do jego obsługi i ograniczają liczbę występujących błędów. Ich ruchami steruje program Galileo, natomiast zarządzanie procesami i czynnościami wykonywanymi przez układnice i ich integracja z pozostałymi systemami, w jakie wyposażony jest magazyn, to zadanie opracowanego przez Mecalux oprogramowania magazynowego Easy WMS.
Ponieważ składowane są tutaj palety ramowe (umożliwiające wejście wideł wózków ze wszystkich czterech stron), konstrukcja regałów, oprócz belek podłużnych, została wyposażona w belki poprzeczne, aby zapewnić bezpieczną obsługę palet przez układnice. Tego typu palety poprawiają stabilność w przypadku układania mniejszych palet na większych paletach bazowych.
Zanim towar wejdzie do automatycznego magazynu, trafia na stanowisko kontroli, gdzie sprawdza się, czy spełnia wymogi określone dla ładunków składowanych w magazynie.
Most transferowy
W większości magazynów o bardzo dużym przepływie towarów na każdy korytarz powinna przypadać jedna układnica. Jednakże w przypadku tego Klienta istotniejsze niż szybka rotacja towarów było ograniczenie kosztów, dlatego w obiekcie o ośmiu korytarzach pracują tylko dwie układnice.
Układnice zmieniają korytarz automatycznie za pomocą mostu transferowego usytuowanego na końcu korytarza. Urządzenie to przemieszcza się wraz z zakotwiczoną do niego układnicą, przenosząc ją z jednego korytarza roboczego do drugiego.
System ten spełnia wszelkie wymogi bezpieczeństwa. Jego konstrukcja nie dopuszcza możliwości wypadnięcia układnicy z dolnej szyny, gdy most transferowy nie jest prawidłowo ustawiony podczas jej transferu do innego korytarza.
Cechy magazynu samonośnego
Wybór magazynu samonośnego podyktowany był faktem, że tego typu obiekt zajmuje jedynie absolutnie niezbędną powierzchnię i kubaturę. Jego konstrukcję nośną tworzą regały, do których bezpośrednio przytwierdzona jest okładzina ścian i dachu. Przy projektowaniu takich magazynów należy uwzględnić wiele różnych czynników, takich jak ciężar składowanych towarów, obciążenia przenoszone przez urządzenia transportu bliskiego, parcie i ssanie wiatru, stopień aktywności sejsmicznej czy obowiązujące lokalnie przepisy budowlane.
Rury instalacji przeciwpożarowej, które zostały odpowiednio zabezpieczone przed przypadkowym uszkodzeniem, są zamontowane na regałach, dzięki czemu w razie pożaru woda skutecznie dociera do palet.
Półautomatyczny magazyn z systemem Pallet Shuttle
Na podeście usytuowanym na wysokości 5 m, naprzeciw magazynu automatycznego i częściowo nad rampami rozładunkowymi, zostały zamontowane dwa poziomy regałów do składowania akumulacyjnego z systemem Pallet Shuttle.
Konstrukcja regałów jest tak zaprojektowana, aby wózki Pallet Shuttle mogły swobodnie przemieszczać się w kanałach towarowych wewnątrz regałów, zapewniając stały przepływ towarów. Dzięki temu operatorzy nie muszą wjeżdżać wózkami widłowymi do korytarzy roboczych.
System Pallet Shuttle zwiększa częstotliwość wejść i wyjść towarów, natomiast podest pozwala maksymalnie wykorzystać kubaturę obiektu, zwielokrotniając powierzchnię użytkową magazynu.
Składowanie palet w stosach
Między magazynem automatycznym a antresolami do przygotowywania zamówień usytuowana jest strefa przeznaczona do składowania palet w stosie bezpośrednio na posadzce. Magazynowane są tutaj produkty o dużych rozmiarach.
Dzięki wytrzymałości produktów i ich opakowań możliwe jest układanie palet jedna na drugiej, co ma na celu optymalne wykorzystanie dostępnej powierzchni.
Regały paletowe
W magazynie firmy DECASA znajdują się również cztery bloki regałów paletowych o podwójnej głębokości, które są usytuowane między antresolami kompletacyjnymi. Łącznie mieszczą one 2890 palet z produktami o małej rotacji (typ C) i o dużych gabarytach. Na ich górnych poziomach dostępny jest zapas produktów składowanych w kartonach na regałach przepływowych.
Operatorzy zaczynają przygotowywanie zamówień od pobrania produktów bezpośrednio z palet, korzystając z wózków systemowych z ruchomą kabiną operatora, które są przeznaczone do kompletacji zamówień na wysokości. Pobrane produkty są następnie transportowane przed rampy załadunkowe, gdzie oczekują na uzupełnienie zamówień o produkty dostarczone z antresol kompletacyjnych.
Antresole do przygotowywania zamówień
Mając na uwadze, że główną potrzebą Klienta jest usprawnienie kompletacji zamówień, Mecalux wyposażył obiekt w trzy antresole o wysokości 10 m, które służą do przygotowywania zamówień na produkty o wysokiej i średniej rotacji (typ B i A). Strefa ta, wraz z automatycznym magazynem samonośnym, stanowi serce centrum dystrybucyjnego firmy DECASA.
Każda antresola składa się z pięciu kondygnacji, z których trzy przeznaczone są do kompletacji zamówień, a dwie do przechowywania zapasu produktów. Oto opis poszczególnych kondygnacji:
- Pierwsza kondygnacja. Tutaj odbywa się kompletacja najmniejszych produktów przechowywanych w kartonowych pudełkach. W tym celu zamontowano pięciopoziomowe regały przepływowe z bieżniami rolkowymi. Nachylenie bieżni powoduje, że towary ułożone na wyższym końcu przesuwają się pod wpływem grawitacji do przeciwległego, niższego końca, który znajduje się przy korytarzu kompletacyjnym. Przez środek każdej kondygnacji przebiega przenośnik.
- Druga i trzecia kondygnacja. Ich funkcje są podobne jak w przypadku pierwszej kondygnacji z tą różnicą, że na regałach przepływowych nie są składowane pudełka, lecz palety. Ten system magazynowania akumulacyjnego pozwala składować towary według zasady FIFO (First In, First Out – pierwsze weszło, pierwsze wyszło). Gwarantuje to doskonałą rotację produktów oraz optymalną kontrolę stanu magazynowego, a także przyspiesza proces przygotowywania zamówień. Operatorzy, którzy pracują w przydzielonych im sektorach, pobierają produkty bezpośrednio z palet i umieszczają je na głównym przenośniku. Gdy paleta jest pusta, umieszcza się ją na biegnącym w przeciwnym kierunku przenośniku pustych palet usytuowanym pod każdym kanałem rolkowym.
- Czwarta i piąta kondygnacja. Tutaj składowany jest zapas produktów wykorzystywanych do przygotowywania zamówień na trzech niższych kondygnacjach. Na obu kondygnacjach zamontowane są po dwa bloki regałów push-back mieszczących cztery palety na głębokość.
Wyprzedzając przyszłe potrzeby firmy, wygospodarowano obszar, w którym można umieścić czwartą antresolę.
Przenośnik spiralny
Na każdej antresoli kompletacyjnej przenośnik spiralny łączy przenośniki trzech niższych kondygnacji. Ma on 5 m wysokości i znajduje się na końcu przeciwległym do sortowni i strefy buforowej.
Przenośnik pierwszej i drugiej kondygnacji transportuje kartony do przenośnika spiralnego, natomiast przenośnik trzeciej kondygnacji łączy się z przenośnikiem prowadzącym do sortowni.
Sortownia
Strefa ta składa się z czterech pętli przenośników (po jednym z każdej antresoli kompletacyjnej), przenośnika, na którym umieszczane są kartony odrzucone z powodu problemów z identyfikacją zamówienia, oraz sortownika, który rozdziela zamówienia według trasy i według kolejności załadunku.
Wszystkie zamówienia dostarczone z trzeciej kondygnacji antresol kompletacyjnych wchodzą do sortownika poprzez system podajników. Przy sortowniku znajduje się 11 ramp załadunkowych z przenośnikami rolkowymi i taśmowymi.
Easy WMS i Galileo, czyli zarządzanie i sterowanie
Easy WMS to rozbudowane, wszechstronne i elastyczne oprogramowanie, którego zadaniem jest kontrolowanie, koordynowanie i zarządzanie wszystkimi ruchami, czynnościami i procesami odbywającymi się w magazynie.
Ma on na celu optymalizację zarządzania przepływem towarów i dokumentów oraz śledzenie procesów logistycznych od przyjęcia towaru do jego wydania.
Natomiast oprogramowanie Galileo steruje wszystkimi ruchami wykonywanymi przez poszczególne urządzenia transportu bliskiego, a zatem jest ono odpowiedzialne za prawidłowe przemieszczanie towarów między kolejnymi strefami magazynu.
Korzyści dla Klienta:
- Optymalna pojemność magazynowa: na powierzchni 22 000 m2 możliwe jest składowanie 36 650 palet.
- Perspektywiczność: w razie potrzeby istnieje możliwość rozbudowy magazynu o przeznaczony do tego celu obszar 2000 m2.
- Większa wydajność: poszczególne rozwiązania zastosowane w magazynie pozwalają zwiększyć przepływ towarów i umożliwiają przygotowywanie większej liczby zamówień.
- Efektywne zarządzanie: dzięki opracowanemu przez Mecalux systemowi zarządzania magazynem Easy WMS i programowi sterującemu urządzeniami magazynowymi Galileo możliwe jest sprawne zarządzanie wszystkimi czynnościami i procesami odbywającymi się w obiekcie.
Centrum logistyczne DECASA w Meksyku – Magazyn automatyczny | |
---|---|
Pojemność magazynowa: | 28 500 palet |
Wymiary palety: | 1000 x 1200 x 1600 mm |
Maksymalna waga palety: | 1300 kg |
Wysokość magazynu: | 34 m |
Galeria
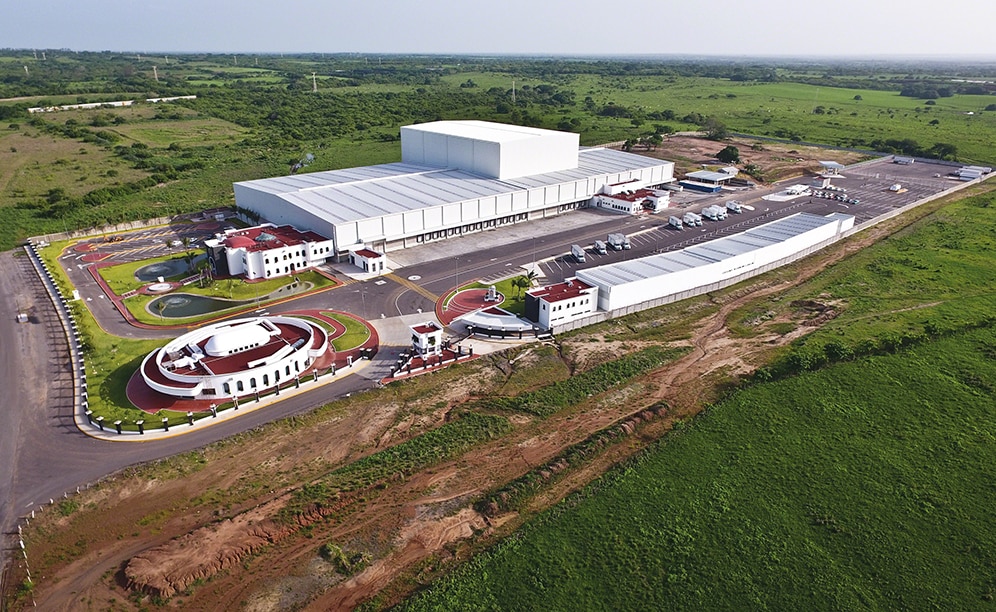
Na powierzchni 4610 m² powstał automatyczny magazyn samonośny o wysokości ok. 30 m, mieszczący ponad 28 000 palet
Zapytaj eksperta