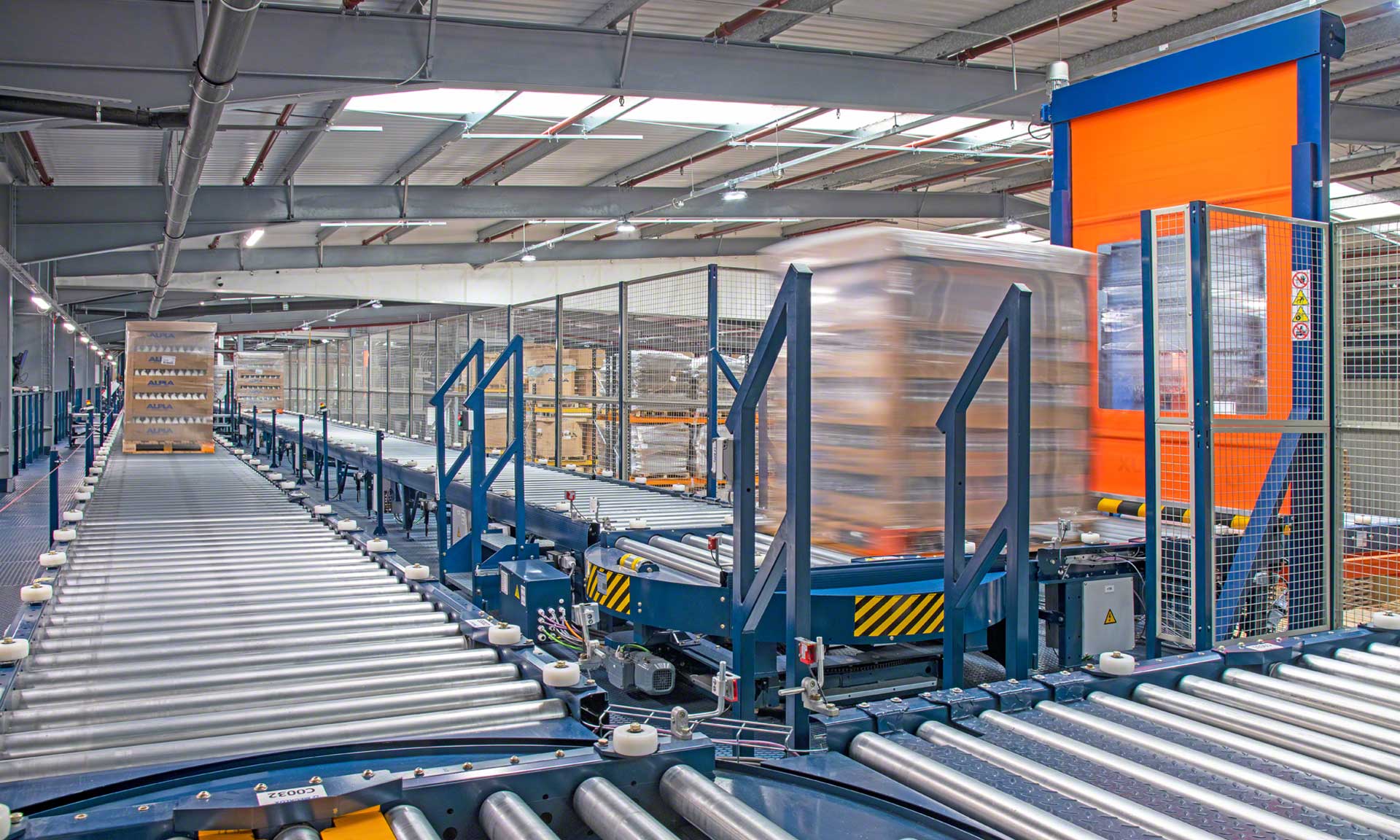
ALPLA zainstalowała automatyczny system transportu w swojej fabryce w Golborne
ALPLA producent opakowań z tworzyw sztucznych, przenosi 2500 palet dziennie, dzięki automatycznym przenośnikom.
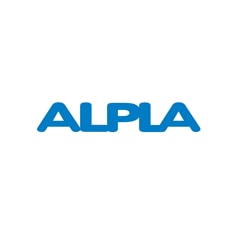
Firma ALPLA zainstalowała automatyczne przenośniki, aby połączyć magazyn z fabryką w swoim centrum produkcyjnym w Golborne. Dzięki wdrożeniu tego rozwiązania, światowy lider w dziedzinie projektowania i produkcji opakowań z tworzyw sztucznych, może transportować 2500 palet dziennie.
ALPLA: innowacyjne systemy opakowaniowe
Założona w Austrii firma ALPLA jest światowym liderem w projektowaniu i produkcji najwyższej jakości rozwiązań opakowaniowych z tworzyw sztucznych. Jej produkty są stosowane w wielu branżach, m.in. spożywczej, farmaceutycznej i kosmetycznej. Niezwykle ważnym elementem strategii firmy jest prowadzenie zrównoważonej i przyjaznej dla środowiska działalności dzięki własnym zakładom recyklingu.
- Rok założenia: 1955
- Rynki: 45 krajów
- Liczba zakładów produkcyjnych: 177
- Liczba pracowników: 22 100
- Obroty: 4 000 000 000 EUR w 2021 roku
POTRZEBY
|
ROZWIĄZANIA
|
KORZYŚCI
|
---|
Jak zapewnić automatyczne połączenie magazynu z zakładem produkcyjnym, gdy oba budynki dzieli odległość 70 m i ulica? Firma ALPLA, jeden z największych producentów opakowań, aby sprostać temu wyzwaniu, zdecydowała się na współpracę z Mecaluxem. „Poprzez zastosowanie rozwiązania w postaci automatycznych przenośników i wind paletowych znacząco obniżyliśmy nie tylko koszty transportu bliskiego, ale również emisję dwutlenku węgla, dzięki czemu nasza działalność jest bardziej zrównoważona i przyjazna dla środowiska” – zauważa Liam Grimwood, Dyrektor Techniczny w fabryce firmy ALPLA w Wielkiej Brytanii.
ALPLA, obecna w 45 krajach, osiągnęła w 2021 roku obroty w wysokości 4 mld euro, notując wzrost o 8,4% w stosunku do roku poprzedniego. W Wielkiej Brytanii, gdzie w Golborne, nieopodal Manchesteru, od kilku lat posiada nowoczesny zakład produkcyjny, realizuje ambitny plan dynamicznego rozwoju.
Kompleks logistyczny składa się z dwóch budynków – fabryki i magazynu – oddzielonych od siebie drogą publiczną. Dyrektor Techniczny wspomina: „Wcześniej w znacznym stopniu polegaliśmy na wykorzystaniu ciężkich pojazdów do transportu towaru z zakładu produkcyjnego do magazynu”.
Wraz ze wzrostem produkcji naturalnie rosło natężenie ruchu ciężarówek między budynkiem produkcyjnym i magazynem. Sytuacja ta zwiększała zarówno koszty operacyjne, jak i zanieczyszczenie powietrza w okolicy. „Potrzebowaliśmy systemu, który pomógłby skomunikować oba obiekty poprzez automatyczne połączenie i transport z zakładu produkcyjnego do magazynu, co pozwoliłoby nam na rezygnację z używania ciężkich pojazdów” – wyjaśnia Dyrektor techniczny Liam Grimwood.
Rozwiązaniem zapewniającym takie połączenie obu budynków była budowa łącznika na wysokości 8 m nad ulicą z poprowadzonym w nim automatycznym przenośnikiem. Dyrektor Techniczny fabryki wymienia powody, dla których jako wykonawcę wybrano Mecalux: „Ze względu na doświadczenie tej firmy w realizacji takich projektów, a także wiedzę zespołu technicznego i kierownika projektu, którzy przez cały czas służyli nam fachową radą”.
Automatyczny system transportowy
„Za pomocą automatycznego systemu transportowego, który pracuje całodobowo przez siedem dni w tygodniu, każdego dnia przemieszczamy około 2500 palet” – podkreśla Liam Grimwood.
Zainstalowany przez Mecalux system składa się z podwójnej pętli przenośników, które transportują towar z produkcji do magazynu. Jak wyjaśnia Dyrektor Techniczny, „jego główną funkcją jest transport palet z kartonowymi tacami zawierającymi butelki, pudła, pojemniki i metalowe kontenery z preformami z politereftalanu etylenu”. Wybrane rozwiązanie może transportować do 5000 palet dziennie, co oznacza, że ALPLA w przyszłości podwoiłaby liczbę ruchów między zakładem produkcyjnym a magazynem.
Przenośnik to automatyczny system transportu bliskiego, w którym elementem nośnym jest bieżnia rolkowa. Ładunek umieszcza się na bieżni, a tworzące ją rolki, obracając się, przesuwają go do celu. Napęd urządzenia stanowią silniki elektryczne, dzięki którym towar jest przemieszczany w sposób kontrolowany i bezpieczny. Przenośniki rolkowe pozwalają zaoszczędzić czas i zwiększają efektywność transportu w przypadku ciągłego przemieszczania dużej ilości towaru tą samą trasą.
Oprócz przenośników w obiektach zainstalowano siedem automatycznych wind, które zapewniają pionowy transport palet. Umożliwia to zniwelowanie różnicy pomiędzy przenośnikami znajdującymi się na poziomie posadzki a tymi, które znajdują się w nadziemnym łączniku. W ten sposób palety z towarem mogą całkowicie automatycznie pokonać całą trasę z fabryki do magazynu.
Na początku przenośnika, dokładnie w miejscu, gdzie palety z towarem opuszczają linie produkcyjne, zostało zamontowane automatyczne stanowisko kontrolne. Ma ono na celu sprawdzanie czy paleta nie jest uszkodzona i czy towar nie wystaje poza jej obrys, gdyż w przeciwnym razie transport przenośnikiem byłby niemożliwy z uwagi na bezpieczeństwo urządzenia i towaru. Na stanowisku tym kontrolowane są także wymiary i waga ładunków pod kątem parametrów regałów, na których będą składowane.
Główne elementy przenośników rolkowych
- Rolki – metalowe rury, w których znajdują się oś i dwa łożyska. Umieszczone jedna za drugą, tworzą bieżnię, stanowiącą element nośny. Ładunek jest przemieszczany w wyniku obracania się rolek.
- Rama i nogi – konstrukcja, na której umieszczona jest bieżnia rolkowa, wyznaczająca kierunek jej biegu. Są wykonane ze stali, której rodzaj zależy od nośności urządzenia.
- Elektryczne elementy napędowe – bieżnia jest wprawiana w ruch przez zespół elementów elektrycznych oraz silników i skrzynek zasilających. Moc zależy od wymaganej prędkości i od ciężaru transportowanych ładunków.
- Zabezpieczenia – elementy mechaniczne i czujniki, takie jak ograniczniki i fotokomórki, zapewniające bezpieczeństwo urządzenia, a także umożliwiające stałe monitorowanie położenia ładunku i przekazywanie informacji do oprogramowania sterującego.
Efektywne połączenie logistyki i produkcji
„Fabryka ALPLA w Golborne ma ugruntowaną pozycję i perspektywy dalszego rozwoju” – podkreśla Liam Grimwood. Aby wciąż umacniać swoją obecność na rynku brytyjskim, firma stosuje w logistyce system lean management, który polega na promowaniu działań stanowiących wartość dodaną dla przedsiębiorstwa w celu maksymalizowania przepływu produktów i minimalizowania kosztów.
Rozwiązanie Mecaluxu pozwoliło firmie ALPLA poprawić efektywność logistyki dzięki automatycznemu połączeniu magazynu z fabryką. W dzisiejszych czasach doskonała synchronizacja logistyki i produkcji jest niezbędna dla zapewnienia sprawnej i elastycznej realizacji zamówień odbiorców. Dzięki wdrożonemu rozwiązaniu łańcuch dostaw firmy ALPLA jest wydajny, elastyczny i optymalnie przygotowany na wyzwania, jakie niesie przyszłość.
Dzięki automatycznemu systemowi transportowemu Mecaluxu, choć transportujemy teraz około 2500 palet dziennie przez 24 godziny na dobę 7 dni w tygodniu, obniżyliśmy koszty i emisję dwutlenku węgla.
Galeria
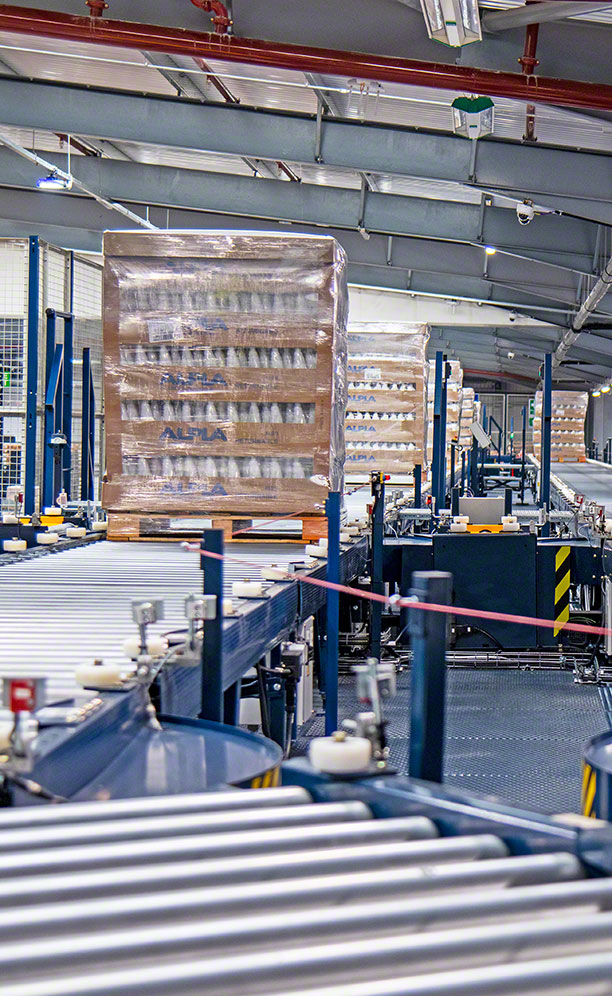
Automatyczne przenośniki paletowe w centrum logistycznym ALPLA
Zapytaj eksperta