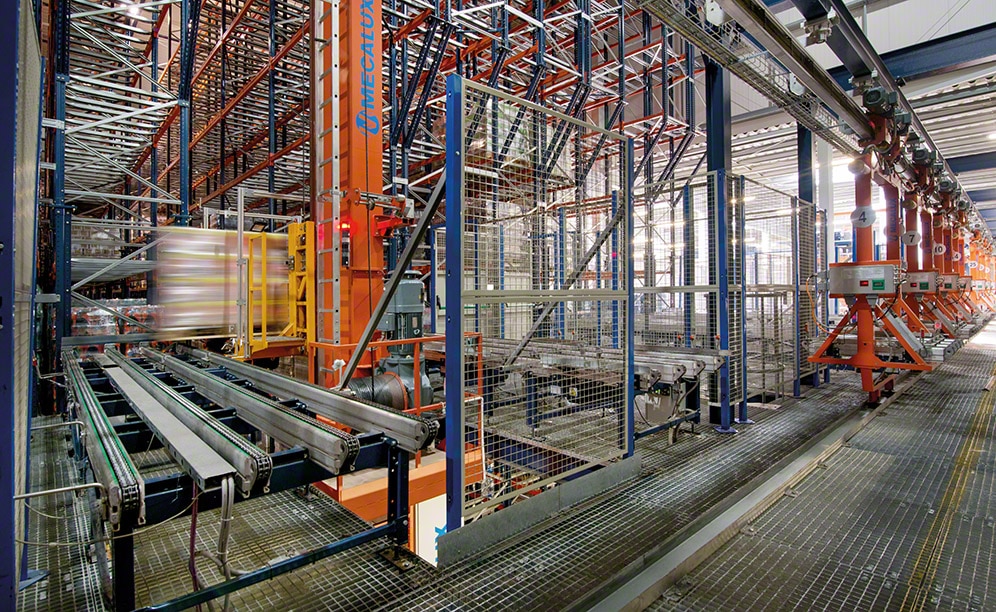
Automatyczny magazyn paletowy i system transportu podwieszanego dla firmy Sokpol
System transportu podwieszanego połączył automatyczny magazyn paletowy z centrum produkcyjnym firmy Sokpol
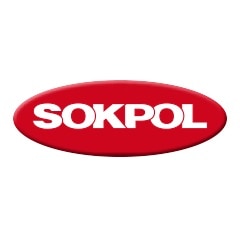
Sokpol to jeden z najbardziej znanych w Polsce producentów soków, nektarów, wód mineralnych i koncentratów. W jego zakładzie produkcyjnym w Myszkowie stosowane są najnowocześniejsze technologie zapewniające wysoką wydajność produkcji. Przy fabryce znajdują się dwa magazyny. Jeden z nich jest w pełni zautomatyzowany i mieści ponad 28 400 palet Euro lub 56 800 palet DHP. Przedsiębiorstwo wciąż się rozwija i stale monitoruje nowe trendy rynkowe dzięki czemu elastycznie dostosowuje swoje działania do zmieniających się potrzeb klientów.
O firmie Sokpol
Soki, napoje, nektary i musy owocowe Sokpolu należą do najbardziej popularnych w Polsce. Działająca od 1992 roku firma od początku swojego istnienia nieustannie opracowuje i wprowadza do sprzedaży nowe produkty.
W ostatnich latach Sokpol wzmocnił swoją obecność na rynkach zagranicznych, a jego produkty można spotkać na półkach sklepowych w wielu krajach Europy, a także Azji i w Stanach Zjednoczonych.
Potrzeby
Większość produktów Sokpolu powstaje w zakładzie produkcyjnym w Myszkowie. Lokalizacja ta sprzyja szybkiej i sprawnej dystrybucji do każdego zakątka Europy.
Początkowo przy zakładzie produkcyjnym znajdował się jeden magazyn przeznaczony do składowania gotowych produktów. Jednakże z czasem, w obliczu wzrostu produkcji, okazało się, że jest on niewystarczający.
W ostatnich latach znacznie powiększył się katalog produktów Sokpolu, a w związku z ekspansją na rynki zagraniczne wzrosła sprzedaż. Mecalux został wybrany jako dostawca rozwiązania, które pozwoli firmie przygotować się do dalszego rozwoju i sprostania wyzwaniom, jakie niesie przyszłość.
Rozwiązanie
Na podstawie wymogów przedstawionych przez Sokpol, Mecalux zaprojektował i zbudował magazyn automatyczny mieszczący ponad 28 400 palet Euro lub 56 800 palet DHP. Jest to bardzo nowoczesne i funkcjonalne rozwiązanie, które gwarantuje wysoką wydajność i spełnia oczekiwania inwestora.
Obiekty Sokpolu zlokalizowane są na dużej powierzchni, a nowy magazyn jest oddalony od zakładu produkcyjnego. Konieczność transportu ładunków na takie odległości z wykorzystaniem standardowych środków transportu wewnętrznego wiąże się z bardzo dużymi kosztami, które należało zminimalizować.
W tym celu Mecalux zbudował łącznik w postaci krytej estakady na wysokości 5 m, wyposażony w system transportu podwieszanego. Gotowe produkty wychodzące z fabryki szybko i sprawnie trafiają przez pierwszy magazyn i łącznik do nowego magazynu.
Magazyn 1
Pierwszy magazyn został zbudowany tuż obok fabryki. Jest on wyposażony w półautomatyczny system składowania palet z wózkami radio-shuttle. Pełni funkcję bufora (magazynu krótkoterminowego składowania), w którym oczekują na wysyłkę do odbiorców głównie produkty o dużej rotacji.
System ten doskonale sprawdza się w przypadku pozycji asortymentowych, na które popyt jest masowy, a więc zamawianych w dużej liczbie palet. Pozwala maksymalnie wykorzystać całą dostępną przestrzeń i uzyskać tym samym dużą pojemność magazynową. Jego obsługa jest prosta i wymaga minimalnego udziału operatorów. Umożliwia to ciągłą i efektywną obsługę przyjęć i wydań ładunków.
Obsługa towaru odbywa się z zastosowaniem metody FIFO (first in, first out – pierwsze weszło, pierwsze wyszło) w dwóch korytarzach roboczych: w jednym towary umieszczane są na regałach, a w drugim z nich pobierane, dzięki czemu te dwie czynności ze sobą nie kolidują.
Przed rampami znajduje się strefa buforowa, gdzie na posadzce gromadzone są palety przygotowane do wysyłki, co ma na celu usprawnienie ich załadunku na ciężarówki.
Magazyn jest dwukondygnacyjny. Na każdej odbywają się inne procesy.
Dolna kondygnacja
Na dolnej kondygnacji znajduje się właściwy magazyn, połączony bezpośrednio z fabryką, dzięki czemu operatorzy mogą bez przeszkód przemieszczać towary z jednej hali do drugiej.
Za pomocą wózka wysokiego podnoszenia operator odbiera paletę i umieszcza ją w wyznaczonym przez system zarządzania magazynem kanale towarowym. Następnie radio-shuttle transportuje paletę do pierwszego wolnego miejsca w tym kanale.
Magazyn 1 wyposażony jest również w system przenośników, który zaczyna swój bieg przy wyjściu z produkcji, a jego zadaniem jest transport towarów przeznaczonych do składowania w magazynie 2. Palety z produktami są przemieszczane do dwóch wind, którymi następnie są dostarczane na górną kondygnację, gdzie zamontowany jest system transportu podwieszanego.
Przy rampach znajduje się trzecia winda. Jest to w obszar, w którym kompletowane są zamówienia na produkty pochodzące zarówno bezpośrednio z produkcji, jak i z magazynu. Strefa ta wyposażona jest w roboty kompletacyjne z wymiennymi głowicami, dzięki czemu jest w pełni adaptowalna do bieżących potrzeb firmy.
Zanim palety dotrą do windy, przechodzą przez stanowisko kontrolne, gdzie sprawdza się ich stan, wagę i wymiary pod kątem spełniania wymogów jakości obowiązujących w magazynie automatycznym.
Obszar przenośników i wind jest zabezpieczony przed dostępem osób nieupoważnionych w zasięg działania tych urządzeń, przez ogrodzenia z paneli siatkowych, bariery optyczne i drzwi z systemem kontroli dostępu.
Górna kondygnacja
System transportu podwieszanego przebiega wzdłuż jednego z boków magazynu 1 w kiedunku łącznika prowadzącego do magazynu 2.
Zastosowanie tego typu rozwiązania pozwoliło maksymalnie wykorzystać powierzchnię magazynu i zapobiec zakłócaniu innych operacji odbywających się w nim.
Łącznik z systemem transportu podwieszanego
Budowa łącznika nadziemnego to rozwiązanie, które pozwoliło skomunikować wszystkie trzy budynki, tym bardziej że magazyny 1 i 2 dzieli ulica.
W łączniku zamontowany został system transportu podwieszanego – Monorail. Poruszające się z prędkością 100 m/min wózki zapewniają stały, szybki i sprawny przepływ towarów.
System ten tworzą przymocowane do sufitu szyny, po których przemieszczają się indywidualnie sterowane wózki transportujące palety. Rozwiązanie to jest skalowalne, co oznacza, że umożliwia zwiększenie przepustowości i wydajności poprzez dodawanie wózków w miarę rozwoju lub bieżących potrzeb firmy.
W magazynie Sokpolu wykorzystuje się głównie europalety i półpalety. Aby móc je transportować, zarówno wózki systemu transportu podwieszanego, jak i przenośniki wyposażone są w cztery szyny łańcuchowe.
Wśród największych zalet systemu transportu podwieszanego można wymienić wydajność, dużą dostępność i niski współczynnik awaryjności.
System transportu podwieszanego przebiega przez całą przednią część magazynu 2, dostarczając lub odbierając palety transportowane przenośnikami wejściowymi i wyjściowymi z korytarzy układnic. Na końcu jego trasy została utworzona strefa serwisowa, do której kierowane są wózki wymagające konserwacji lub napraw. W strefie tej odbywają się także postoje wózków.
System ten został bardzo starannie zaprojektowany, z uwzględnieniem dynamiki i wielkości przepływu towarów między obydwoma magazynami. Z tego powodu zostały utworzone dwa skróty, dzięki którym wózki nie muszą pokonywać całej trasy.
Magazyn 2
Magazyn automatyczny, o wysokości 15,5 m, składa się z dziewięciu korytarzy z regałami o podwójnej głębokości po obu stronach.
Towary są umieszczane na regałach z zastosowaniem kryterium rotacji (kategorie A, B i C). Produkty o największej rotacji zajmują przednią część magazynu, natomiast towary, na które zapotrzebowanie jest mniejsze, składowane są w głębi obiektu. Taki sposób klasyfikowania i rozmieszczenia towarów służy optymalizacji ruchów układnic i przyczynia się do zwiększenia wydajności.
Układnice jednokolumnowe przemieszczają się wzdłuż każdego korytarza z prędkością 160 m/min w poziomie i 38 m/min w pionie.
Układnice pobierają palety z przenośników wejściowych i umieszczają je na regałach w miejscach wyznaczonych przez system zarządzania magazynem Easy WMS opracowany przez Mecalux. W przypadku wydań towarów z magazynu układnice wykonują te same czynności, lecz w odwrotnej kolejności.
Przednia część magazynu składa się z dwóch kondygnacji. Na górnej pracuje system transportu podwieszanego oraz odbywają się przyjęcia i wydania towaru. Na dolnej kondygnacji znajdują się szafy zasilające i sterownicze oraz wejścia do stref serwisowych. Rozdzielnie elektryczne wysyłają i odbierają sygnały oraz zasilają urządzenia magazynowe, czyli układnice, przenośniki, windy oraz system transportu podwieszanego.
Do magazynu przylega niższy, również dwukondygnacyjny budynek. Na każdej kondygnacji odbywają się inne procesy.
Górna kondygnacja
Jest to antresola, na której znajdują się stanowiska kompletacyjne.
Wózki systemu transportu podwieszanego dostarczają tutaj palety potrzebne do przygotowania zamówień. Przenośnik wejściowy wyposażony jest w stół hydrauliczny, na którym umieszcza się palety dostarczone za pomocą wózków paletowych.
Dolna kondygnacja
Na dolnej kondygnacji znajdują się strefa wysyłek i strefa buforowa. Palety z produktami trafiają tutaj z górnej kondygnacji dwiema windami. Następnie za pomocą dwóch wózków wahadłowych umieszczane są w odpowiednim kanale przepływowym.
Przemieszczające się po szynach podwójne wózki wahadłowe, dostarczają z magazynu skompletowane palety. Ładunki te umieszczane są na przenośnikach grawitacyjnych, które zasilają rampy załadowcze.
Strefa buforowa wyposażona jest w 40 kanałów przepływowych o lekkim nachyleniu. Palety przemieszczają się po nich samoczynnie, od wejścia do przeciwległego końca usytuowanego od strony ramp. Rolki na końcu kanału są dzielone, co umożliwia wykorzystanie różnego rodzaju wózków widłowych do pobierania palet.
Easy WMS
Z uwagi na wielkość centrum produkcyjno-magazynowego Sokpolu bardzo istotną kwestię stanowiło zapewnienie niezawodnego systemu informatycznego. Opracowany przez Mecalux system zarządzania magazynem Easy WMS kieruje wszystkimi czynnościami odbywającymi się w magazynie, w tym m.in. przyjęciami towarów z tutejszej hali produkcyjnej i z innych fabryk, wyznaczaniem miejsc do składowania, kontrolą nad stanem magazynowym, pobieraniem palet i ich transportowaniem do strefy wysyłek.
Aby zapewnić składowanie towaru w odpowiednich lokalizacjach na regałach, program Easy WMS wykorzystuje reguły i algorytmy, które uwzględniają cechy i tempo rotacji produktów.
System ten wskazuje, które produkty w danym momencie powinny opuścić magazyn. Następnie są one przemieszczane do strefy buforowej, gdzie oczekują na załadunek.
Prawidłowe funkcjonowanie obiektu zapewnia stała komunikacja Easy WMS z systemem zarządzania przedsiębiorstwem (ERP) stosowanym przez Sokpol, a także z modułem sterującym Galileo również opracowanym przez Mecalux.
Galileo steruje ruchem wszystkich urządzeń automatycznych (przenośników, układnic, wind i systemu transportu podwieszanego) pracujących w obu magazynach, a także rejestruje ewentualne nieprawidłowości w ich pracy. Dostarcza w czasie rzeczywistym informacji o każdym z urządzeń, a za pomocą systemu SCADA potrafi symulować procesy zachodzące w zautomatyzowanym obiekcie.
Korzyści dla Klienta:
- Efektywny system transportowy: system transportu podwieszanego łączy oba magazyny z zakładem produkcyjnym, zapewniając odpowiedni przepływ towarów.
- Bezpieczeństwo obiektu: urządzenia elektromechaniczne wyposażone są w zabezpieczenia zapobiegające wypadkom i uniemożliwiające dostęp osobom nieupoważnionym.
- Optymalna organizacja składowania: rozmieszczenie składowanych towarów w sposób uwzględniający ich cechy i rotację przekłada się na większą wydajność magazynów.
Magazyn automatyczny firmy Sokpol | |
---|---|
Urządzenia: | System transportu podwieszanego |
Urządzenia: | Windy |
Urządzenia: | Układnice |
Urządzenia: | Wózek wahadłowy |
Urządzenia: | Przenośniki |
Urządzenia: | Kanały przepływowe strefy buforowej |
Galeria
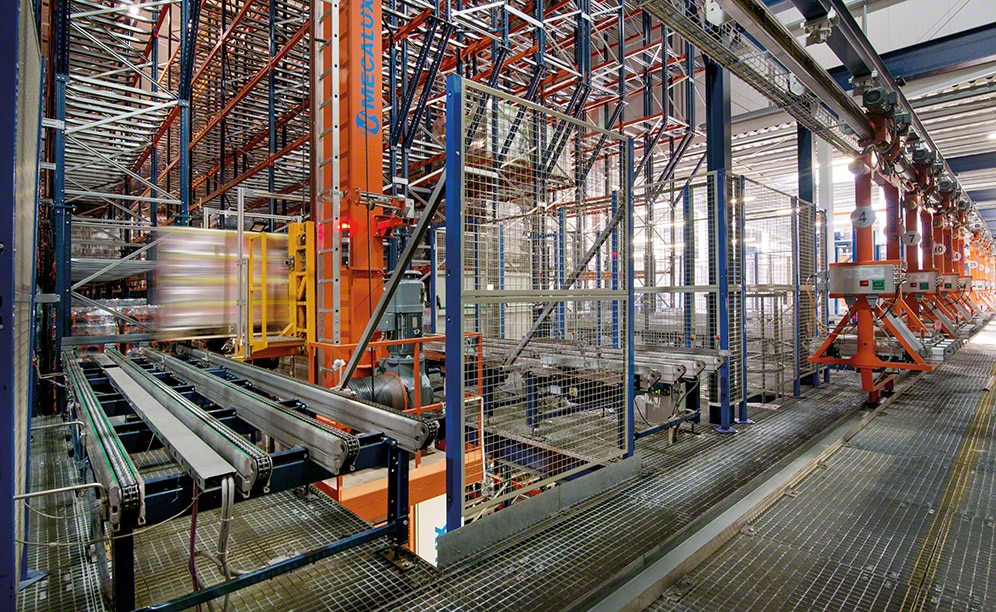
Magazyn automatyczny firmy Sokpol może pomieścić 28 400 palet
Zapytaj eksperta