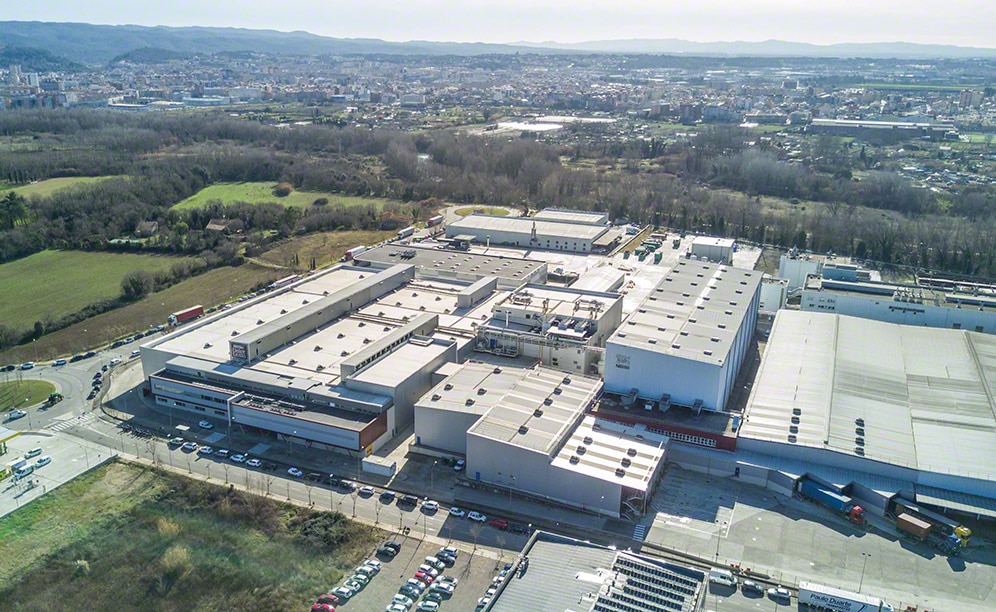
Szybszy przepływ towarów w fabryce Nestle dzięki zastosowaniu urządzeń transportu automatycznego
Efektywny system transportu bliskiego w zakładzie produkcyjnym Nestlé w Gironie
Fabryka kawy Nescafé zlokalizowana w katalońskiej Gironie jest jednym z największych na świecie zakładów produkcyjnych należących do Nestlé. Obiekt podlega stałej rozbudowie wraz ze zmieniającymi się potrzebami rynku, dlatego współpraca Mecaluxu i Nestlé trwa od 1990 roku. Obejmuje projektowanie i wdrażanie najskuteczniejszych rozwiązań, których celem jest usprawnianie procesu logistycznego niezbędnego dla rozwoju Nestlé.
O firmie Nestlé
Nestlé, największy na świecie koncern z branży spożywczej, prowadzi sprzedaż w około 190 krajach na świecie. Oferta Nestlé obejmuje ponad 8000 marek takich produktów jak m.in. odżywki dla dzieci, wody mineralne, płatki śniadaniowe, kawa rozpuszczalna, herbata, mleko w proszku, wyroby cukiernicze, czekolady oraz karmy dla zwierząt.
Nestlé posiada obecnie dziesięć fabryk w pięciu regionach autonomicznych Hiszpanii. Zakłady te wyróżniają się wysoką wydajnością – aż 44% ich produkcji trafia na rynki innych krajów.
Jedną z nich jest fabryka w Gironie, która powstała już w 1968 roku. Produkuje się tutaj kawę rozpuszczalną Nescafé, a od 2009 roku również kapsułki Dolce Gusto. W ostatnich latach obiekt odnotowuje znaczący wzrost produkcji i jest dziś największą na świecie fabryką kawy rozpuszczalnej należącą do Nestlé.
Pod istniejącą od 1938 roku marką Nescafé na przestrzeni lat powstało wiele innowacyjnych produktów o różnych smakach, na każdą kieszeń i na każdą okazję.
Współpraca Mecaluxu i Nestlé
Współpraca obu firm rozpoczęła się w 1990 roku, kiedy to Mecalux zbudował w girońskiej fabryce automatyczny magazyn samonośny do składowania palet.
Obiekt mierzy 25 m wysokości i 107 m długości. W siedmiu korytarzach z regałami o pojedynczej głębokości po obu stronach mieści się 16 380 palet z gotowymi produktami przeznaczonymi do wysyłki.
Kilkanaście lat później, w 2006 roku, Mecalux zbudował nieopodal drugi magazyn samonośny o wysokości 21 m. Składa się on z dwóch korytarzy z regałami o pojedynczej głębokości i mieści 740 kontenerów z surowcami.
Magazyn ten jest dostosowany do wielkości i innych cech składowanych tu kontenerów o wymiarach 1210 x 1060 x 1810 mm. Przyjęcia i wydania towaru odbywają się automatycznie za pomocą przenośników, które transportują kontenery bezpośrednio na koniec korytarzy. Kontenery nie mają płóz, dlatego aby ułatwić ich przemieszczanie na przenośnikach, ustawia się je na paletach.
Półki regałów są natomiast wyposażone w specjalne podstawy, dzięki czemu kontenery mogą być na nich składowane bez konieczności stosowania palet.
Nescafé Dolce Gusto
W 2005 roku Nestlé wprowadziło do sprzedaży kapsułki z kawą i herbatą do ekspresów ciśnieniowych. Pierwsza fabryka kapsułek Nescafé Dolce Gusto powstała w Wielkiej Brytanii. Dobre przyjęcie produktu w Hiszpanii zaowocowało decyzją o rozpoczęciu produkcji w Gironie, aby zapewnić szybsze dostawy kapsułek na hiszpański rynek.
Nestlé rozbudowało więc zakład produkcyjny w Gironie i obok istniejącego obiektu powstała w 2009 roku fabryka kapsułek Nescafé Dolce Gusto. Dzięki współpracy z Mecaluxem zakład został rozbudowany i dostosowany do nowych wymagań stawianych przez Nestlé. Prace odbywały się w kilku etapach.
Pierwszy etap
Nestlé zwróciło się do Mecaluxu o wykonanie połączenia nowej fabryki kapsułek Nescafé Dolce Gusto z magazynem gotowych produktów za pomocą wydajnego systemu transportu bliskiego, który zapewniłby stały przepływ ładunków z fabryki do magazynu. Projekt był sporym wyzwaniem, ponieważ wymagał połączenia dwóch hal oddzielonych od siebie ulicą. Mecalux zaproponował więc budowę łącznika w postaci krytej estakady na wysokości 6 m, która połączyłaby oba budynki za pomocą poprowadzonego wewnątrz niej systemu przenośników.
Rozwiązanie to nie przeszkadza w normalnej komunikacji na powierzchni, a produkty nie są narażone na niekorzystne warunki meteorologiczne. Przenośniki rolkowe transportują towar z prędkością 20 m/min. Są w pełni zautomatyzowane, a ponieważ funkcjonują przy minimalnym udziale operatorów, pozwalają wyeliminować błędy, jakie zwykle towarzyszą ręcznej obsłudze procesów.
Drugi etap
W 2011 roku zostały zamontowane dodatkowe dwie windy łączące obie kondygnacje zakładu.
Do wind towar jest dostarczany przenośnikami poprowadzonymi górą na wytrzymałej konstrukcji zapewniającej ich stabilność.
Dzięki temu możliwe było maksymalne wykorzystanie przestrzeni dostępnej w obiekcie. Pozwoliło to również zapobiec kolidowaniu transportu z innymi czynnościami odbywającymi się w fabryce.
Trzeci etap
W 2012 roku, z uwagi na wzrost sprzedaży kapsułek Dolce Gusto, Nestlé stanęło przed koniecznością zwiększenia intensywności przepływu palet z fabryki do magazynu produktów gotowych.
W tym celu Mecalux dostarczył kolejną windę, która została zamontowana przy wyjściu z linii produkcyjnej, dzięki czemu uzyskano dwukrotnie większy przepływ palet.
Windy, które mogą transportować po dwie palety (jedna za drugą), w relatywnie krótkim czasie obsługują ładunki z produktami schodzącymi z linii produkcyjnej.
Czwarty etap
Kolejnym etapem współpracy było wykonanie połączenia zakładu produkcyjnego z halą wysyłek, tak aby można było kierować tam gotowe produkty bezpośrednio, z pominięciem magazynu.
Mecalux zainstalował dodatkowe wyjście w systemie przenośników wychodzących z fabryki, które biegną łącznikiem w kierunku magazynu. Palety z towarem nie trafiają jednak do magazynu, lecz do windy, która zwozi je w dół do hali wysyłkowej.
Automatyzacja hali wysyłkowej pozwoliła zwiększyć wydajność wszystkich odbywających się tutaj czynności za pomocą następujących rozwiązań:
- Strefa układania palet na paletach bazowych – wózek wahadłowy dostarcza palety do sześciu przenośników, którymi są one kierowane do automatycznego urządzenia służącego do ustawiania mniejszych palet z towarem na większych paletach bazowych.
- Kanały buforowe – inny wózek wahadłowy odbiera palety ustawione na paletach bazowych i dostarcza je do sześciu przepływowych kanałów buforowych utworzonych z przenośników rolkowych o lekkim spadku. System ten służy do grupowania palet według zamówień lub tras.
- Strefa buforowa na posadzce – naprzeciwko kanałów buforowych została utworzona strefa buforowa, gdzie palety są przygotowywane do załadunku na ciężarówki. Pozwala to wyeliminować konieczność oczekiwania na wyjście towaru z magazynu.
Piąty etap
Obok hali wysyłkowej usytuowany jest magazyn worków kontenerowych, tak zwanych big bag, zawierających surowce. Dla ułatwienia transportu i składowania worki te umieszczane są na paletach.
Palety trafiają do magazynu przenośnikami, przechodząc przez stanowisko kontrolne, gdzie sprawdza się ich stan oraz wagę i wymiary pod kątem spełniania wymogów jakości obowiązujących w magazynie.
Następnie winda dostarcza je na górną kondygnację, gdzie znajdują się dwa bloki regałów wjezdnych.
Regały te mają wysokość 6,5 m i są podzielone na trzy poziomy. Każdy poziom tworzą szyny nośne wykonane ze stali galwanizowanej o wysokiej wytrzymałości, na których umieszczane są palety z workami big bag.
Oprogramowanie sterujące
Z uwagi na wielkość zakładu produkcyjnego Nestlé zasadnicze znaczenie ma oprogramowanie, które koordynuje pracę wszystkich automatycznych urządzeń.
Mecalux wdrożył w obiekcie moduł sterujący Galileo, który kieruje ruchem przenośników, wózków wahadłowych i wind, gwarantując ich ciągłą i prawidłową pracę.
Galileo wyposażony jest w bardzo intuicyjny interfejs i za pomocą systemu SCADA symuluje proces produkcyjny w zautomatyzowanym obiekcie.
Program jest połączony na stałe z systemem zarządzania magazynem i systemem planowania zasobów przedsiębiorstwa (ERP) i komunikuje się z nimi w obu kierunkach, wymieniając dane, dzięki czemu zakład produkcyjny Nestlé osiąga maksymalną wydajność wszystkich procesów.
Korzyści dla Klienta:
- Efektywny system transportowy: przenośniki zapewniają bardzo szybkie przemieszczanie towaru do poszczególnych stref zakładu produkcyjnego i magazynu.
- Szybki przepływ towaru: automatyczny system przenośników i wind pozwala uzyskać odpowiedni przepływ ładunków.
- Bezpieczeństwo: ruchome elementy urządzeń transportowych są odpowiednio zabezpieczone, co zapobiega wypadkom i uniemożliwia dostęp osób nieupoważnionych.
Galeria
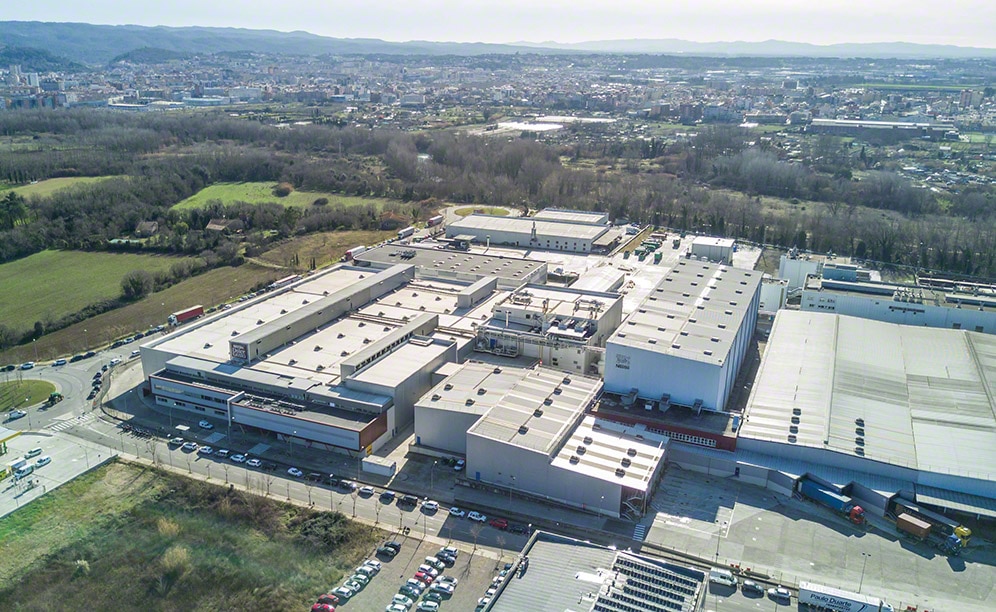
Mecalux zbudował w girońskiej fabryce automatyczny magazyn samonośny do składowania palet
Zapytaj eksperta