
Blechwarenfabrik: najnowocześniejsza w Europie fabryka opakowań metalowych
Blachwarenfabrik, producent opakowań metalowych, integruje procesy logistyczne w nowym centrum w Linburgu (Niemcy).

Blechwarenfabrik, niemiecki producent puszek aluminiowych, uruchomił nowy zakład w Limburgu, gdzie powstaje ponad 100 milionów metalowych opakowań rocznie. Pracą dwóch automatycznych magazynów połączonych z fabryką kieruje Easy WMS, m.in. zaopatrując produkcję w surowce i odbierając gotowe produkty.
Blechwarenfabrik: tradycja i innowacja
Blechwarenfabrik to jeden z największych w Europie producentów puszek i innych opakowań metalowych wykorzystywanych w różnych sektorach przemysłu, głównie w branży chemicznej.
- Rok założenia: 1872
- Liczba pracowników: 500
- Zdolność produkcyjna: ponad 100 milionów opakowań metalowych rocznie
- Zakłady produkcyjne: Niemcy, Polska, Dania i Rosja
POTRZEBY
|
ROZWIĄZANIA
|
KORZYŚCI
|
---|
Blechwarenfabrik, europejski lider w produkcji opakowań metalowych dla sektora chemicznego, zautomatyzował i scyfryzował logistykę, aby sprostać wzrostowi sprzedaży.
W mieście Limburg an der Lahn w zachodnich Niemczech firma dysponuje obiektem o powierzchni 22 000 m², w którym cały transport towaru jest w pełni zautomatyzowany – wózki samojezdne (AGV) łączą dwa automatyczne magazyny z liniami produkcyjnymi.
Wcześniej firma Blechwarenfabrik posiadała w Niemczech dwie fabryki, w których produkowała wszystkie opakowania metalowe (puszki na napoje, konserwy itp.). Ze względu na za małą powierzchnię obsługę logistyczną zapewniała jej firma zewnętrzna. „Surowce składowaliśmy w głównym magazynie, a gotowe produkty opuszczające linie produkcyjne transportowaliśmy do magazynu oddalonego o 5 km” – wyjaśnia Christoph Weber, Kierownik Techniczny.
Firma zdecydowała się jednak skupić logistykę w jednym miejscu, aby w ten sposób obniżyć koszty, a także zmniejszyć niekorzystny wpływ swojej działalności na środowisko oraz scentralizować wszystkie działania w jednym, doskonale zorganizowanym i wysoce zdigitalizowanym obiekcie. Blechwarenfabrik rozpoczął zatem realizację ambitnego projektu: budowę nowej siedziby w Offheim, dzielnicy Limburgu. W nowoczesnym obiekcie mieszczą się biura, 25 linii produkcyjnych i magazyny. Fabryka przetwarza rocznie 22 000 ton stali, z której powstaje ponad 100 milionów opakowań.
Centralizacja zarówno produkcji, jak i logistyki przebiegała etapami, ponieważ niezbędne było częściowe zmodyfikowanie procesu produkcyjnego w celu dostosowania go do nowej lokalizacji. Zespół techniczny Mecaluxu opracował rozwiązanie optymalnie spełniające potrzeby i wymogi firmy Blechwarenfabrik. Christoph Weber uważa, że „tak duży projekt nie jest łatwy do zrealizowania, ponieważ konieczne było uwzględnienie wielu szczegółów. Z pomocą Mecaluxu jednak przeniesienie całego procesu logistycznego do nowego obiektu przebiegło niezwykle sprawnie”.
Automatyzacja na rzecz zrównoważonego rozwoju i wydajności
Od początku było jasne, że nowy obiekt będzie realizował koncepcję przemysłu 4.0, wykorzystując technologię do automatyzacji i integracji produkcji i logistyki, aby połączyć je w jeden wydajnie działający mechanizm. „Dotychczas zarządzanie towarem odbywało się u nas ręcznie, a surowce były transportowane na produkcję za pomocą wózków widłowych. Ponadto mieliśmy kilka osobnych obiektów, co utrudniało logistykę” – wspomina Kierownik Techniczny.
Teraz produkcja i magazynowanie mieszczą się w jednym obiekcie, a transport wewnętrzny na jego terenie zapewnia 15 wózków samojezdnych, których obsługa odbywa się przy minimalnym udziale człowieka, gdyż ich pracą kieruje system zarządzania magazynem (WMS). Christoph Weber podkreśla, że „obsługa towaru, od przyjęcia do wysyłki, została zautomatyzowana”, i dodaje: „Dzięki współpracy z Mecaluxem posiadamy najnowocześniejszą fabrykę opakowań metalowych w Europie”.
Jednym z głównych celów firmy Blechwarenfabrik było ograniczenie wpływu jej działalności na środowisko. Według szacunków skoncentrowanie wszystkich procesów w jednym miejscu, a tym samym wyeliminowanie konieczności przemieszczania surowców i gotowych produktów pomiędzy zakładami produkcyjnymi i magazynami pozwoli zmniejszyć emisję gazów cieplarnianych o 2600 ton rocznie.
W nowym zakładzie przewidziano również miejsce na składowanie odpadów metalowych powstających podczas produkcji i przeznaczonych do recyklingu. Ponadto na dachu fabryki zamontowano 4100 paneli fotowoltaicznych, które wytwarzają energię elektryczną wykorzystywaną w procesach produkcji i magazynowania.
Sprawne połączenie logistyki i produkcji dzięki Easy WMS
W nowej siedzibie Blechwarenfabrik posiada dwa automatyczne magazyny: jeden mieści się w hali i służy do składowania surowców, drugi zaś to obiekt samonośny przeznaczony dla gotowych produktów. Magazyny samonośne charakteryzują się tym, że ich konstrukcję nośną tworzą regały, które poza ciężarem własnym i składowanego towaru muszą utrzymać ciężar okładziny ścian i dachu. Pracą obiektów kieruje opracowany przez Mecalux system zarządzania magazynem Easy WMS, który zarządza i optymalizuje procesy w obu magazynach.
„Połączenie produkcji i logistyki było jednym z największych wyzwań w tym projekcie. Udało się nam je zrealizować poprzez stopniowe przenoszenie procesu produkcyjnego do nowego obiektu, co pozwalało analizować i rozwiązywać wszelkie problemy na bieżąco” – wyjaśnia Uwe Wonsack, Dyrektor Operacyjny firmy Blechwarenfabrik.
Aby sprawnie łączyć logistykę i produkcję, firma wykorzystuje system Easy WMS. Oprogramowanie Mecaluxu jest zintegrowane z systemem ERP Infor, z którego korzysta Blachwarenfabrik, i z systemem zarządzania produkcją (MES). Narzędzia te wymieniają ze sobą dane, informując o zapotrzebowaniu, organizując zaopatrzenie produkcji oraz nadzorując i monitorując procesy. „Programy te wspierają nawzajem swoje działanie. Easy WMS dostarcza nam wszystkie informacje o składowanych produktach, takie jak aktualny stan magazynowy i dokładna lokalizacja” – zauważa Uwe Wonsack. ERP współpracuje także z innymi programami biorącymi udział w procesie produkcyjnym, np.: zarządzającym pracą robotów paletyzujących lub gromadzącym dane o przebiegu kolejnych etapów produkcji.
Easy WMS komunikuje się również z oprogramowaniem sterującym pojazdami AGV w celu zapewnienia przepływu ładunków pomiędzy magazynami a produkcją. Uwe Wonsack wyjaśnia, że „wózki samojezdne zaopatrują linie produkcyjne automatycznie. Kiedy Easy WMS otrzymuje zamówienie z produkcji, organizuje jego przygotowanie w magazynie. Wózki pobierają wówczas surowce i transportują je na odpowiednią linię. Proces jest prosty, szybki i efektywny”.
Ponadto do zadań oprogramowania Mecaluxu należy gospodarka odpadami powstającymi w fabryce Blechwarenfabrik i zlecanie ich transportu do strefy recyklingu.
System zarządzania magazynem: identyfikowalność i precyzyjna kontrola
Easy WMS to narzędzie, które zapewnia pełną identyfikowalność produktów składowanych w magazynie. Monitoruje towar od momentu przyjęcia do magazynu surowców aż do chwili wysłania gotowych produktów do odbiorcy. Połączenie logistyki i produkcji za pomocą systemu Easy WMS przyniosło firmie Blechwarenfabrik wiele korzyści:
- Widoczność zapasów i zarządzanie nimi w czasie rzeczywistym. Easy WMS zna aktualny stan magazynowy i dokładną lokalizację każdego artykułu, zarówno surowców jak i wyrobów gotowych.
- Zaopatrzenie produkcji metodą just in time. Oprogramowanie zapewnia dostarczenie surowców na produkcję w wymaganym momencie i w wymaganej ilości.
- Zarządzanie listą produktów i zestawieniami materiałów. Każde zlecenie produkcyjne obejmuje surowce potrzebne do wytworzenia konkretnych produktów.
- Usprawnienie procesu produkcyjnego. Odpowiednia organizacja pracy i dokładna kontrola nad składowanymi materiałami i produktami owocują większą wydajnością i efektywnością produkcji.
- Praca bez papieru. Operatorzy zlecają dostarczenie potrzebnych im surowców, korzystając z terminali radiowych lub tabletów.
„Największą zmianą, jaką przyniósł w naszej pracy system Easy WMS, jest dokładna kontrola zapasów: teraz w każdej chwili wiemy, gdzie znajduje się dany produkt lub surowiec” – podkreśla Uwe Wonsack. Znajomość stanu magazynowego w czasie rzeczywistym jest niezbędna dla zapewnienia płynności procesu produkcyjnego, ponieważ umożliwia zaopatrywanie linii metodą just in time.
W pełni automatyczny łańcuch dostaw
Automatyzacja przyczynia się do obniżenia koszów i zwiększenia wydajności pracy magazynu. Firma Blechwarenfabrik zoptymalizowała i usprawniła przepływ ładunków na wszystkich etapach: przyjęcia, składowania, kompletacji i wysyłki.
Układnice, przenośniki paletowe i wózki samojezdne AGV zapewniają stały i kontrolowany ruch towaru. Każdego dnia na linie produkcyjne jest dostarczanych 600 palet z surowcami, a w tym samym czasie 1200 palet z 500 000 gotowych opakowań metalowych opuszcza produkcję, aby trafić do magazynu, następnie zaś do setek odbiorców w całej Europie.
➤ Magazyn surowców
Automatyczny magazyn o wysokości 11 m i długości 100 m składa się z dwóch korytarzy z regałami o pojedynczej głębokości po obu stronach. Mieści się na nich 2500 palet z blachą używaną do produkcji puszek.
Magazyn przyjmuje od dostawców średnio 125 000 arkuszy blachy dziennie. Pierwszą rzeczą, jaką zleca Easy WMS, połączony na stałe z systemem MES (Manufacturing Execution System), jest umieszczenie każdego arkusza na odpowiedniej palecie i we właściwej pozycji, w zależności od tego, jakie opakowanie i na której linii produkcyjnej ma zostać z niego wyprodukowane.
„Towar jest obsługiwany metodą FIFO, która polega na tym, że paleta umieszczona na regale jako pierwsza, opuszcza go również pierwsza. W ten sposób zapobiegamy starzeniu się produktów i możemy zapewnić ciągły przepływ towarów” – wyjaśnia Dyrektor Operacyjny.
Easy WMS czuwa nad prawidłowym zaopatrzeniem linii produkcyjnych, sprawdzając, ile arkuszy jest potrzebnych do poszczególnych zleceń produkcyjnych i w jakiej pozycji mają się znajdować. Jeśli w magazynie nie ma wystarczającej liczby arkuszy blachy w odpowiedniej pozycji, zleca pobranie innych i ich obrócenie za pomocą specjalnej maszyny.
Następnie, na podstawie poleceń Easy WMS, samojezdne wózki AGV odbierają arkusze z dwóch stanowisk wydawania towaru z magazynu i automatycznie dostarczają je na regały paletowe znajdujące się w pobliżu linii produkcyjnych.
Regały te pełnią rolę bufora, ponieważ surowiec jest na nich składowany tymczasowo, do momentu, w którym będzie potrzebny na liniach produkcyjnych. Gdy opuści bufor, trafia tutaj następna partia, przygotowana do kolejnego zlecenia.
➤ Linie produkcyjne
Kiedy rozpoczyna się proces produkcyjny, Easy WMS zleca samojezdnym wózkom AGV dostarczenie surowców i półproduktów na odpowiednie linie.
Jednym z półproduktów, których dostawa jest wymagana, są korpusy puszek (zwane bodies). Nie składuje się ich w magazynie automatycznym, lecz bezpośrednio na regałach paletowych przy liniach produkcyjnych. Easy WMS monitoruje również te artykuły i we właściwym momencie zleca ich wysyłkę na produkcję.
Na produkcji operatorzy mogą komunikować się z systemem Easy WMS, aby np. zamówić puste palety, zgłosić wadliwe zapasy lub zwrócić nadwyżkę surowców do magazynu.
Dyrektor Operacyjny podkreśla, iż „bardzo ważne jest to, że operatorzy na liniach produkcyjnych nie muszą wykonywać drugorzędnych zadań i mogą w pełni skupić się na swojej głównej pracy. Odciąża ich Easy WMS, któremu za pomocą terminala radiowego zlecają dostarczenie surowców”.
Easy WMS kieruje również odbiorem odpadów produkcyjnych przez wózki AGV, które automatycznie przewożą je do strefy recyklingu.
➤ Magazyn gotowych produktów
Automatyczny magazyn samonośny o pojemności 18 000 palet ma wysokość 31 m i składa się z czterech korytarzy z regałami o podwójnej głębokości po obu stronach.
W ciągu godziny z linii produkcyjnych do magazynu jest dostarczanych ok. 80 palet z gotowymi produktami. Jednostki ładunkowe przechodzą przez stanowisko kontroli, gdzie sprawdza się, czy ich wymiary są zgodne z wymogami miejsc składowania.
Następnie Easy WMS wyznacza dla każdej palety miejsce składowania, wykorzystując reguły i algorytmy, które uwzględniają takie parametry jak pozycja asortymentowa i szybkość rotacji.
Jeśli chodzi o realizację zamówień, ERP powiadamia Easy WMS, które palety mają zostać wysłane do odbiorców. Co godzinę magazyn opuszcza 100 palet, z których część Easy WMS kieruje bezpośrednio na odpowiednie rampy załadunkowe, część zaś do strefy kompletacji. Zdaniem Uwe Wonsacka „wysyłka przebiega bardzo płynnie”.
Stanowisko kompletacyjne jest usytuowane w przedniej części magazynu. Zamówienia przygotowuje się tutaj metodą „produkt do operatora”, co oznacza, że operatorzy nie muszą przemieszczać się po obiekcie, aby pobrać produkty, lecz po prostu oczekują na stanowisku, aż dostarczą im je automatyczne urządzenia. Wówczas pobierają z odpowiednich palet wymaganą liczbę kartonów, które umieszczają na innych paletach według zamówień.
Operatorzy mają do dyspozycji monitor i terminale radiowe, by móc śledzić polecenia Easy WMS, który krok po kroku kieruje ich pracą. Dzięki tym urządzeniom posiadają oni dokładne informacje, które produkty mają pobrać i gdzie dostarczyć, a jedną z korzyści osiągniętych przez Blechwarenfabrik jest minimalizacja ryzyka błędów w zamówieniach.
Palety, które trafiają do wysyłki bez etapu kompletacji, są etykietowane i kierowane do właściwej rampy. W celu przyspieszenia załadunku utworzono strefę buforową, w której palety są grupowane na posadzce według zamówień i tras.
Wydajność produkcji i logistyki w erze przemysłu 4.0
Firma Blachwarebfabrik zwiększyła tempo rozwoju dzięki technologii. Dynamicznie wkroczyła w erę przemysłu 4.0, dzięki czemu uzyskała dokładniejszą kontrolę nad procesami produkcyjnymi i logistycznymi, co przekłada się na zwiększenie efektywności obsługi klientów. Dzięki automatyzacji firma zwiększyła wydajność produkcyjną i jest w stanie wyprodukować ponad 100 milionów opakowań rocznie, ale także posiada bardziej zrównoważony łańcuch dostaw.
Automatyczne urządzenia transportu wewnętrznego oraz system zarządzania magazynem Easy WMS łączą fabrykę z magazynami, by zaopatrywać linie produkcyjne metodą just in time, a następnie sprawnie odbierać gotowe produkty i wysyłać je do odbiorców. Cyfryzacja i automatyzacja to połączenie, które dla firmy Blechwarenfabrik oznacza sukces i bez wątpienia umożliwi jej dalszy rozwój.
Kiedy planowaliśmy nowy zakład produkcyjny, wiedzieliśmy, że wszystkie procesy będą się w nim odbywać automatycznie. Dzięki Mecaluxowi dysponujemy logistyką na najwyższym poziomie.
Galeria
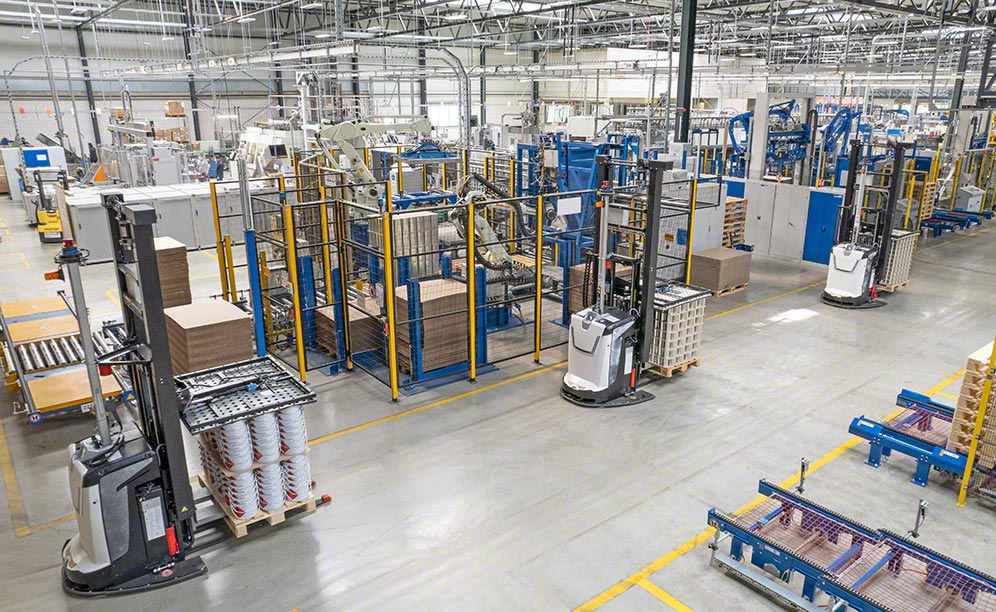
Automatyczny magazyn surowców firmy Blachwarenfabrik w Limburgu (Niemcy)
Zapytaj eksperta