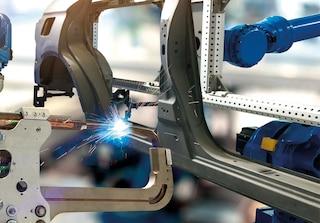
System MRP – sprawne zarządzanie procesem produkcyjnym
Planowanie zapotrzebowania materiałowego w procesie produkcji stanowi spore wyzwanie logistyczne dla każdego zakładu przemysłowego. Ile potrzeba surowców, kiedy należy je zamówić, w jakim terminie powinny zostać dostarczone, ile wyrobów wytworzyć w danym przedziale czasowym – to tylko kilka przykładowych problemów, na które producenci od kilku dziesięcioleci znajdują rozwiązanie przy użyciu systemów MRP (Material Requirements Planning).
W niniejszym artykule szczegółowo zajmiemy się zagadnieniem planowania zapotrzebowania materiałowego. Omawiamy, czym jest, jak działa, jakie przynosi korzyści i dlaczego planowanie jest tak istotne w procesie produkcji. Wyjaśniamy też, czym różnią się systemy MRP od ERP.
Czym jest MRP?
Systemy planowania zapotrzebowania materiałowego ułatwiają zarządzanie procesami produkcji. Pozwala to z wyprzedzeniem zaplanować czynności związane z zakupem surowców, wytwarzaniem produktów i dostarczaniem gotowych wyrobów do klientów.
Pierwsze tego typu systemy powstały w latach 70. ubiegłego wieku i od tamtego czasu cieszą się niesłabnącym zainteresowaniem. W książce Production Planning and Control: A Comprehensive Approach napisanej przez D.R. Kirana w 1975 roku liczbę przedsiębiorstw korzystających ze wsparcia systemu MRP przy optymalizacji procesu produkcji szacowano na ok. 700. Przez kolejnych sześć lat rosła ona w zawrotnym tempie 174% rocznie, aby w 1981 r. osiągnąć 8000.
Systemy MRP uważane są za fundament wielu nowoczesnych rozwiązań programistycznych powstałych z myślą o racjonalizacji procesów przemysłowych, m.in.: MRP II (Manufacturing Resource Planning), ERP (Enterprise Resource Planning), CRM (Customer Relationship Management), SRM (Supplier Relationship Management) czy MES (Manufacturing Execution System).
Program ułatwia organizację czynności produkcyjnych i usprawnia zarządzanie zapasami z uwzględnieniem specyficznych potrzeb przedsiębiorstwa. Efektywne planowanie zapotrzebowania materiałowego pozwala łatwiej osiągnąć podstawowy cel każdego producenta, tj. dysponowanie niezbędną ilością surowców do wytworzenia artykułów oraz dostarczenie gotowych produktów klientom w możliwie jak najkrótszym czasie i niewielkim kosztem.
Jak działa MRP?
Do prawidłowego działania system MRP wymaga kilku niezbędnych danych wejściowych:
- Główny harmonogram produkcji – w skrócie MPS (od Master Production Schedule) – określa, ile artykułów należy wyprodukować w danym czasie.
- Zestawienie materiałów – w skrócie BOM (od bill of materials) – określa, ile i jakich surowców potrzeba do wytworzenia gotowego produktu.
- Ewidencja zapasów – szczegółowe informacje dotyczące zaopatrzenia (dostępny stan magazynowy, ilości zamówionych surowców, odwołane zamówienia, czas oczekiwania na dostawę itd.). Dzięki niej uzyskujemy dostęp do wszystkich aktualnych danych o zasobach do bieżącego wykorzystania.
Na postawie powyższych informacji system planowania zapotrzebowania materiałowego pozwala opracować następujące dane wyjściowe:
- Zalecany główny harmonogram produkcji wskazujący daty rozpoczęcia i zakończenia poszczególnych procesów produkcyjnych, ilości surowców niezbędnych na każdym etapie oraz zestawienie materiałów (BOM). Dane te umożliwiają realizację głównego harmonogramu produkcji.
- Zalecany harmonogram zakupów określający daty przyjęcia zamówionych materiałów oraz terminy składania kolejnych zamówień zgodnie z wyznaczonym tempem produkcji.
W ten sposób system MRP gwarantuje utrzymanie minimalnego stanu zapasów niezbędnego do zapewnienia ciągłości produkcji, pozwalając zarazem wydajniej planować jej poszczególne etapy oraz procesy zakupu i dostawy materiałów.
Przykładowe planowanie zapotrzebowania materiałowego
Mając gotowy główny harmonogram produkcji i zestawienie materiałów, możemy określić, że do wytworzenia jednego gotowego produktu X potrzeba 2 jednostek materiału A i 1 jednostki materiału B. Z kolei do wytworzenia jednej jednostki materiału A potrzeba 3 sztuk elementu C, a do wytworzenia jednostki materiału B potrzeba 2 sztuk elementu C i 4 sztuk elementu D.
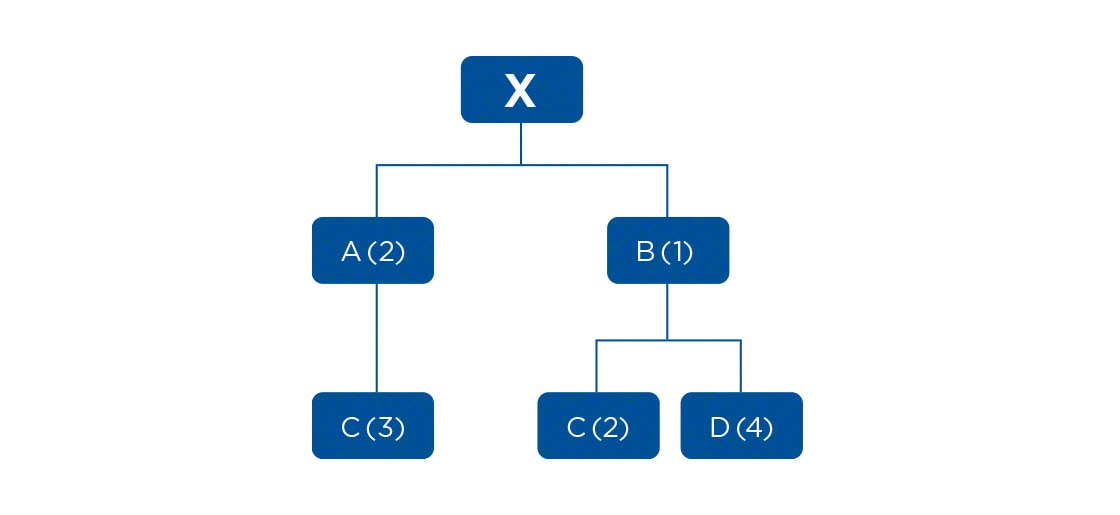
Następnie sporządzamy ewidencję zapasów (IRF, Inventory Record File) z uwzględnieniem dostępnych zasobów i czasów oczekiwania (lead time) na dostawy poszczególnych surowców:
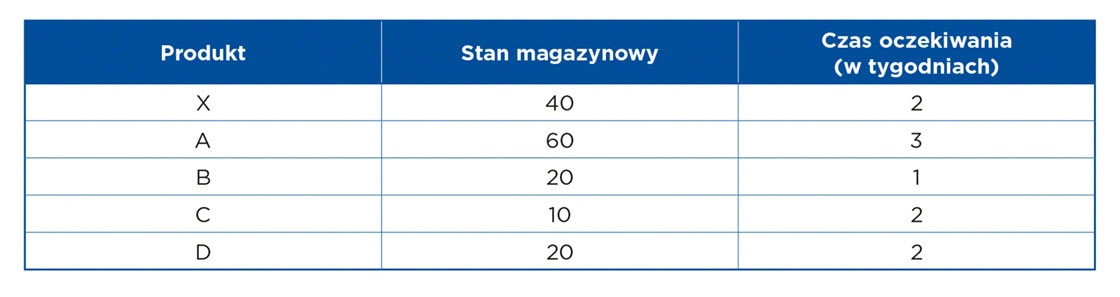
Zobaczmy więc, jak wygląda planowanie zapotrzebowania materiałowego przy założeniu, że musimy wyprodukować 100 jednostek produktu X w 10 tygodni:
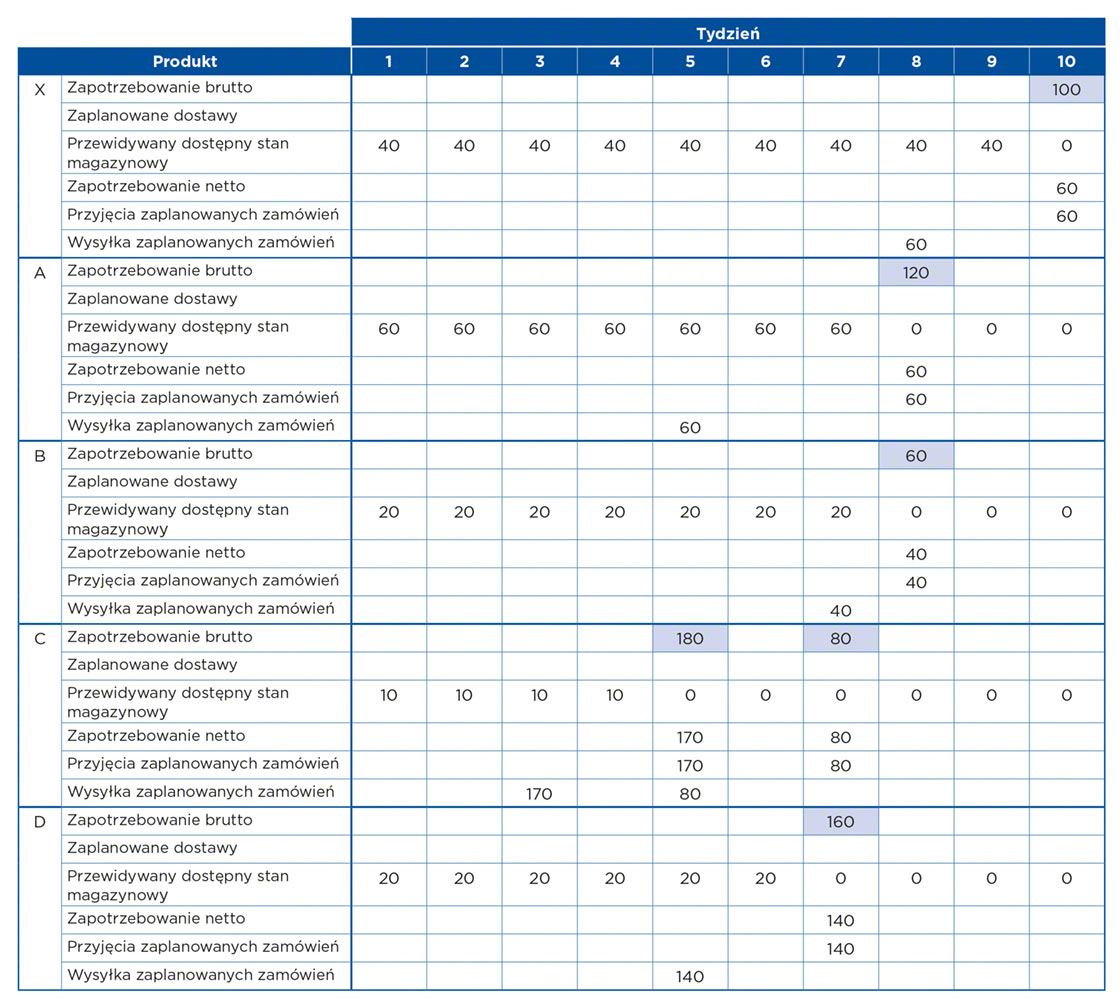
Z powyższej tabeli wynika, że aby zgromadzić 100 jednostek produktu X w 10. tygodniu, musimy wytworzyć 60 oprócz 40 już posiadanych na stanie. W ewidencji zapasów określiliśmy, że czas oczekiwania (lead time) na produkt X wynosi 2 tygodnie, co oznacza, że zamówienie należy złożyć w 8. tygodniu.
Skoro do wytworzenia każdej jednostki produktu X potrzeba 2 jednostek produktu A, w 8. tygodniu musimy mieć do dyspozycji 120 jednostek produktu A. Biorąc pod uwagę, że obecnie mamy ich na stanie 60, zapotrzebowanie netto na produkt A wynosi 60 jednostek. Uwzględniając czas oczekiwania na dostawę, zamówienie musimy złożyć z trzytygodniowym wyprzedzeniem.
W ten sam sposób określamy zapotrzebowanie netto na produkty B, C, D i F wraz z terminami składania zamówień.
Zalety korzystania z systemu MRP
Planowanie zapotrzebowania materiałowego pozwala określić ilość potrzebnych do produkcji surowców i elementów oraz liczbę gotowych wyrobów.
Efektywne planowanie zapotrzebowania materiałowego przynosi następujące korzyści:
- Pełna dostępność surowców niezbędnych do produkcji.
- Dotrzymanie terminów dostaw.
- Ograniczenie poziomu przechowywanych zapasów surowców i gotowych wyrobów do niezbędnego minimum.
- Lepsza organizacja produkcji, dostaw i zakupów.
- Redukcja kosztów.
System MRP pozwala skutecznie rozwiązać wiele problemów, z którymi regularnie borykają się zakłady produkcyjne, w szczególności związanych z organizacją zakupu surowców. Zakup niedostatecznej ilości czy ewentualne pomyłki w zamówieniach grożą opóźnieniem w realizacji dostaw. Z drugiej strony zamówienie zbyt dużej ilości materiałów oznacza nieunikniony wzrost kosztów magazynowania.
Różnice między MRP i MRP II
Na początku lat 80. ubiegłego wieku MRP (Material Requirements Planning) wyewoluowały w o wiele bardziej zaawansowane narzędzia informatyczne, tj. systemy planowania zasobów produkcyjnych, określane skrótem MRP II (Manufacturing Resource Planning). Przyjrzyjmy się najistotniejszym zmianom, jakie przyniosła ta ewolucja:
- Oprócz kwestii ściśle związanych z zarządzaniem materiałami do produkcji, systemy MRP II pomagają usprawnić pracę innych działów przedsiębiorstwa, m.in. handlowego czy finansowego.
- W przeciwieństwie do MRP, który opiera się na głównym harmonogramie produkcji, MRP II uwzględnia popyt i inne tendencje rynkowe.
- W skutecznym planowaniu MRP II bazuje na aktualnej sytuacji przedsiębiorstwa, podczas gdy MRP opiera się na zgromadzonym dotychczas doświadczeniu.
- MRP jest systemem otwartym, a MRP II – zamkniętym. W praktyce oznacza to, że może ponownie korzystać z wygenerowanych przez siebie danych, aby jeszcze lepiej dostosować planowanie do bieżącej sytuacji.
MRP II jako wszechstronniejszy następca MRP nie tylko determinuje wolumen oraz termin wyprodukowania danej partii, ale określa, jakie zasoby, w jakich ilościach i na jakim etapie będą potrzebne do zapewniania ciągłości produkcji.
Różnice między systemami MRP i ERP
Wprowadzone do użytku na początku lat 90. systemy ERP (Enterprise Resource Planning) stanowią dalsze rozwinięcie rozwiązań MRP w postaci integracji wszystkich obszarów działalności przedsiębiorstwa.
Innymi słowy, podczas gdy MRP to odrębne oprogramowanie, ERP stanowi połączenie systemów informatycznych używanych przez wszystkie działy przedsiębiorstwa, pracujących w oparciu o wspólną, scentralizowaną bazę danych. Dzięki takiemu rozwiązaniu każdy dział ma dostęp do aktualnych danych i może kontrolować przepływ pracy, eliminować ewentualnie błędy i komunikować się z pozostałymi działami.
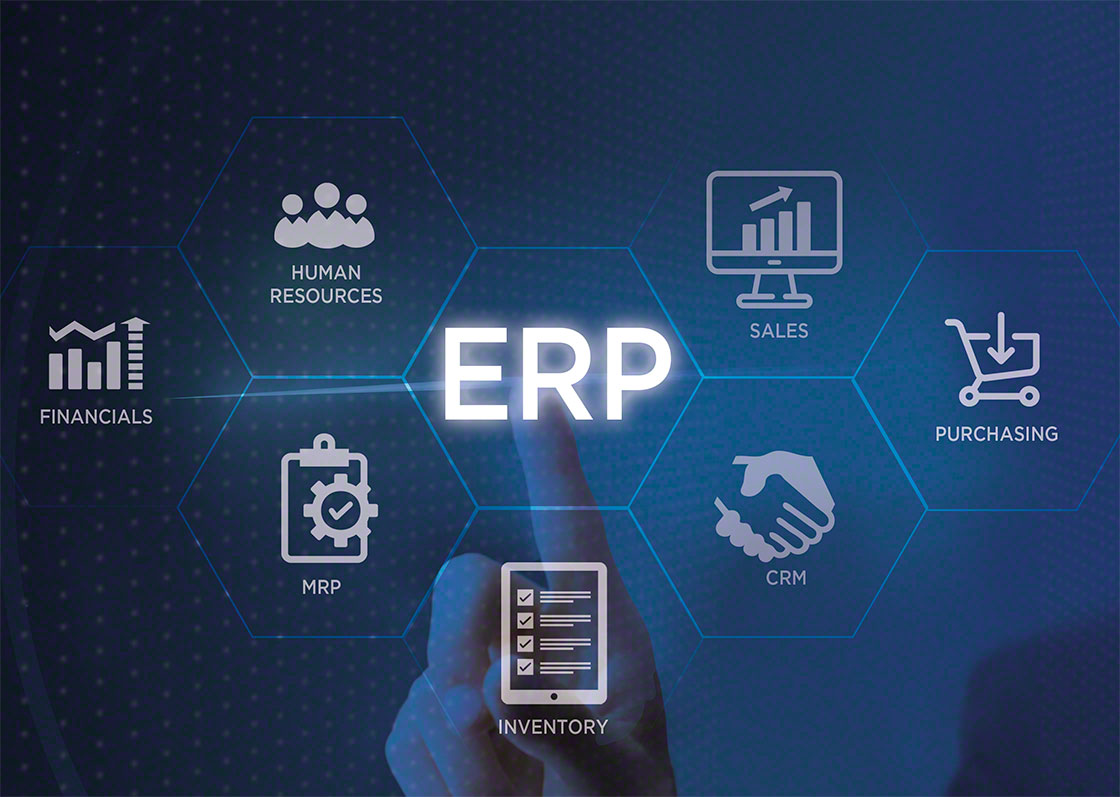
MRP w kontekście rozwoju technologii
Po pięciu dekadach użytkowania nie ulega wątpliwości, że systemy planowania wyznaczyły zupełnie nową jakość w procesie produkcji. Dzięki zastosowaniu nowoczesnej technologii ich podstawowa funkcja – czyli przewidywanie potrzeb celem zabezpieczenia odpowiedniej ilości surowców i materiałów – może zapewnić większą wydajność całego łańcucha dostaw.
Mecalux od zawsze stawia na najnowocześniejsze rozwiązania technologiczne, zarówno w gospodarce magazynowej, jak i w zarządzaniu logistycznym, czego doskonałym przykładem jest system Easy WMS, który może współpracować i obustronnie wymieniać dane z dowolnym ERP, pozwalając wyraźnie poprawić efektywność pracy magazynu.
Jeżeli chcesz dostosować działalność swojego przedsiębiorstwa do bieżących trendów rządzących łańcuchem dostaw, skontaktuj się z nami.