Posadzka magazynu jest jego kluczowym elementem, ponieważ stanowi podstawę całej instalacji. Wszystkie operacje wewnątrzmagazynowe przeprowadzane są na posadzce, dlatego tak ważne jest zwrócenie szczególnej uwagi na wszystkie aspekty z nią związane, począwszy od rodzajów obciążeń, które będzie ona przenosić, po podłoże czy warstwę wykończeniową.
Rodzaje obciążeń
Należy wziąć pod uwagę, że nie wszystkie obciążenia przenoszone przez posadzkę są jednakowe. Istotne jest, aby podstawa była w stanie wytrzymać bardzo duże obciążenia dwojakiego rodzaju: statyczne i dynamiczne.
Obciążenia statyczne
Obciążenia generowane pod słupami regałów to bardzo intensywne obciążenia, skoncentrowane na bardzo małej powierzchni i równomiernie rozłożone na całym ruszcie fundamentowym posadzki magazynu. Są one bardzo kłopotliwe dla większości budowniczych, ponieważ osiągają wartości 7–8 ton (a nawet znacznie wiecej) i są skupione na powierzchni przekroju słupa około 80 lub 100 cm2.
![]() |
![]() |
|
Przykład obciążeń generowanych na słupach regałów. | Analiza powierzchni w procesie budowy magazynu. |
Obciążenia dynamiczne
Obciążenia dynamiczne, wytwarzane przez urządzenia przeładunkowe przemieszczające się po bardzo wąskich korytarzach, są również bardzo duże i zależą od używanego typu maszyny. W najbardziej skrajnym przypadku, tzn. w przypadku układnicy, jej masa może przekraczać 18 t i skupiać się na minimalnej powierzchni, czyli na kole nośnym. Nacisk ten jest w łatwy sposób minimalizowany, ponieważ obciążenie rozkłada się na całej szynie prowadzącej, po której przesuwa się maszyna.
W innego rodzaju urządzeniach przeładunkowych najcięższe obciążenia występują, gdy urządzenia te są zatrzymane. Przykładem mogą być wózki trójstronne, które wywierają największy nacisk na podłogę w momencie układania lub podnoszenia ładunku na maksymalną wysokość, gdy widły są rozsunięte na bok. W tym momencie nacisk wywierany na koła nośne jest tak duży, że może przekraczać granice wytrzymałości posadzki, a nawet samych kół i ich łożysk. Obciążenie to jest przekazywane bezpośrednio na boki korytarza.
Pozostałe maszyny, takie jak wózki widłowe z przeciwwagą, wytwarzają największy nacisk na posadzkę podczas rozładunku, gdy opierają się na tylnych kołach, ponieważ to właśnie w tej części znajduje się przeciwwaga. Gdy wózek jest załadowany, następuje wyrównanie obciążenia w przedniej części (na zasadzie dźwigni) i chociaż zwiększa się masa całkowita, jest ona rozłożona na całej powierzchni maszyny. W takim przypadku obciążenie również skupia się na małej powierzchni, tzn. na oponach.
Co oznacza zwrot „odpowiednia nawierzchnia“?
Nawierzchnia (i jej fundamenty) jest elementem nośnym i przenoszącym obciążenia od powierzchni posadzki w dół, aż do poziomu podglebia. Odnosi się to zarówno do obciążeń dynamicznych wytwarzanych przez maszyny w ruchu, jak i do obciążeń statycznych generowanych przez słupy regałów. Odpowiednia nawierzchnia to nawierzchnia posiadająca twardość i stabilność konieczne do wykonania powyższych zadań.
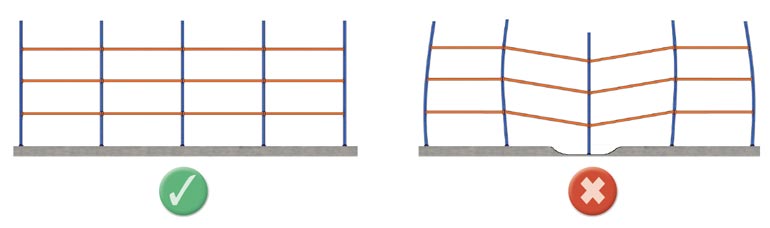
Czynnością niezbędną jest odpowiednia analiza wypoziomowania nawierzchnhi w celu zapewnienia prawidłowego funkcjonowania magazynu.
Wykończenie powierzchni musi być odpowiednio wypoziomowane w granicach i tolerancjach związanych ze stosowaniem danego rodzaju obiektu, ze specjalistycznymi urządzeniami i określonym systemem magazynowym. Osiągnięcie tych celów i właściwości jest zadaniem projektantów i wykonawców budowy.
Znaczenie podłoża
Przed rozpoczęciem układania posadzki magazynu konieczne jest zbadanie podłoża lub warstwy nośnej, na której będzie się ona opierać. Podłoże jest bardzo zmienne i mogą występować bardzo duże różnice między poszczególnymi miejscami, nawet jeżeli znajdują się one bardzo blisko siebie i w obrębie tej samej przestrzeni. Dlatego różnice między określonymi punktami w jednym pomieszczeniu mogą być znaczne.
Najważniejsze parametry, na które należy zwrócić uwagę w podłożu, to wytrzymałość na ściskanie, skłonność do poślizgu i możliwość absorpcji wody. Aby poznać wartości tych czynników w określonym miejscu i sprawdzić, jak zmieniają się na różnych głębokościach, konieczne jest przeprowadzenie badania w miejscu budowy.
Należy koniecznie upewnić się, czy podłoże magazynu zapewnia odpowiednie zachowanie obciążenia umieszczanego na posadzce spoczywającej na podłożu. W zależności od uzyskanych wyników niezbędnych badań należy wybrać dokładne miejsce i strefę, w której zostanie wzniesiony obiekt.
Cechy tej istotnej części gleby mają decydujący wpływ na fundamenty. Do wykonania fundamentów można wykorzystać proste poduszki podporowe lub pasy o większej lub mniejszej szerokości oraz, w skrajnych przypadkach, cały ruszt fundamentowy. Czasami cechy podłoża zmuszają do zmiany położenia słupów regałów magazynowych, aby pokrywały się one z miejscami gwarantującymi bezpieczeństwo.
Skład posadzki
Na podłożu wykonuje się posadzkę, która składa się z warstwy nośnej z silnie zagęszczonej mieszanki gwarantującej wytrzymałość na obciążenia. Warstwa ta składa się z dowolnego rodzaju materiału, tzn. z materiału naturalnego lub zasypki. Na warstwie nośnej układa się płytę betonową zapewniającą wytrzymałość na nacisk.
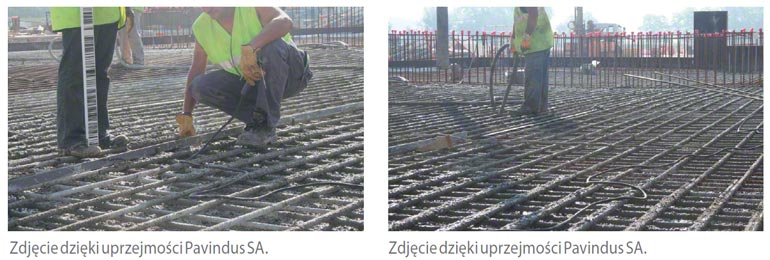
Innym sposobem na rozwiązanie problemu potencjalnych pęknięć i bardzo częstego zwijania jest zastosowanie wzmocnienia z lekkiej siatki metalowej ułożonej blisko powierzchni. Jest to bardzo powszechna praktyka, która umożliwia wykonanie dłuższych płyt z mniejszą liczbą szczelin dylatacyjnych.
Można także wykonać zbrojenie ze stalowych prętów, które zwiększą wytrzymałość warstwy utwardzonej pomimo nieuniknionych skurczów i osuwania betonu podczas procesu. Bez względu na to, czy zastosuje się zbrojenie, nieuniknione jest pojawienie się pęknięć na utwardzonych płytach, nawet pomimo zachowania szczególnej ostrożności podczas budowy. Jeżeli pęknięcia powstają w sposób przypadkowy i niekontrolowany, brak możliwości wykonania odpowiedniego wypełnienia – z uwagi na ich nieregularność – zawsze powoduje wahania obciążeń.
Często celowo powoduje się powstawanie pęknięć, aby otwory pojawiły się w określonych miejscach, które będzie można obserwować i kontrolować. Odbywa się to poprzez przepiłowanie płyty wzdłuż określonego pasa, wykonując cięcie na głębokość od jednej czwartej do jednej trzeciej grubości warstwy. W ten sposób pęknięcie rozwija się w określonej pozycji i łatwo można je wypełnić w prosty i czysty sposób.
Szczeliny w posadzce
Szczeliny, które znajdują się na posadzce obiektów, mogą być spowodowane przez różne przyczyny: mogą je tworzyć poszczególne paski wzdłuż nawierzchni, mogą być skutkiem konstrukcji – powstają pod koniec dnia pracy i na początku kolejnego dnia – mogą być wykonane w celu ominięcia słupów lub ścian albo mogą być spowodowane przez cięcia piłą. Bez względu na ich przyczynę szczeliny te powodują problemy, ponieważ mogą poszerzyć się przez ciągłe przejazdy wózków widłowych.
Szczeliny powinny być połączone lub przyśrubowane do konstrukcji warstwy nośnej, aby ruchy nie były przenoszone pod sąsiednimi płytami. W szczelinach dylatacyjnych śruby powinny być odpowiednio wbudowane i umieszczone równo w jednej linii. Śruby te muszą mieć wolny koniec ślizgowy wyposażony w tuleję z tworzywa sztucznego osadzoną w jednej z płyt.
Ponadto szerokość szczelin dylatacyjnych powinna być proporcjonalna do grubości płyty, jednak nie może przekraczać 10 mm. Chociaż można je wykonać w dowolnym miejscu, należy unikać miejsc, w których występują bardzo duże obciążenia skupione, tzn. w pobliżu słupów regałów.
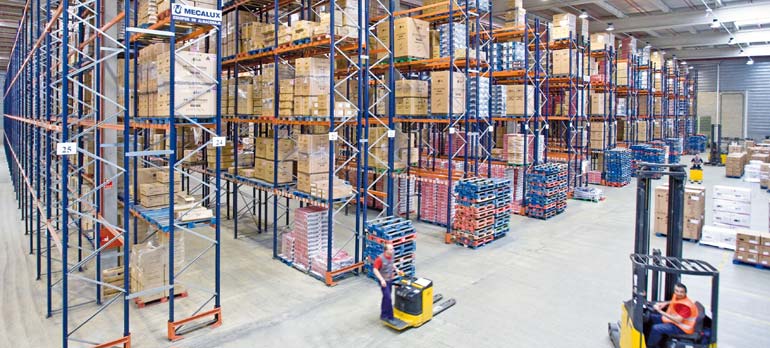
Magazyn firmy zajmującej się elektroniką użytkową.
Warstwa wykończenia
Nad warstwą nośną i płytą układa się trzecią warstwę, tzn. wykończenie. Jest to warstwa jednolita i tworzy ona właściwą powierzchnię roboczą. Zazwyczaj warstwa wykończenia składa się z mieszanki z cementu granulatowego o grubości około 50 mm. Gładkość, twardość i właściwości robocze tego materiału są najbardziej odpowiednie do zapewnienia wytrzymałości posadzki na warunki występujące podczas użytkowania urządzeń w magazynie.
Beton granulitowy układa się na mokrą płytę betonu przemysłowego, tworząc jeden blok i łącząc szczeliny. W takiej sytuacji powstaje pytanie: czy należy wykonać warstwę wykończenia razem z płytą, tym samym powodując, że problemy i zabiegi z nią związane, w szczególności szczeliny, będą także dotyczyć warstwy wykończenia? Czy też należy wykonać oba elementy oddzielnie?
Warstwę tę można ułożyć w sposób niezależny i oddzielny na suchą płytę, jednak w takim przypadku grubość suchej płyty musi wynosić co najmniej 125 mm. Następnie należy ułożyć nową warstwę betonu, w której wystąpią te same problemy związane z kruchością i zwijaniem płyty głównej, ponieważ powierzchnia wykończenia zachowuje się i kurczy w sposób niezależny. Aby tego uniknąć, należy zastosować nową warstwę lub membranę oddzielającą, która będzie tworzyć cienką warstwę bez widocznych szczelin. Dodanie mieszanek bitumicznych lub kopolimerów umożliwia wykonanie wyjątkowo cienkich mieszanek betonowych.
Jeżeli stosowane są żywice syntetyczne, można utworzyć warstwę o grubości zaledwie 3 mm, która stanowi nawierzchnię o doskonałym wykończeniu. Jeżeli natomiast celem jest wykonanie bardziej komfortowej powierzchni, można użyć żywicy o większej sprężystości, tzn. o większej zdolności elastycznej do absorbowania deformacji i do odkształcania się po zaprzestaniu wywierania nacisku.
Należy jednak pamiętać, że niektóre warstwy utworzone przez specjalne mieszanki mogą nie mieć stabilności lub pełnych właściwości granulitu. Dotyczy to w szczególności zastosowania nieodpowiednich żywic do usunięcia wad górnej warstwy. Mieszanki te mogą się okazać nie tylko niestabilne, ale także bardzo drogie.
Posadzki magazynów wymagają zatem bardzo starannego przygotowania i konserwacji zapobiegawczej w trakcie ich użytkowania. W ten sposób można zapobiec i usunąć wady oraz uszkodzenia szczelin spowodowane przez koła wózków widłowych przejeżdżających po nich. Tak wymagające warstwy wykończenia nie są konieczne w magazynach automatycznych, ponieważ nie przemieszczają się w nich wózki.
Ułożenie posadzki
Powyżej wyjaśniono podstawowe pojęcia i elementy tworzące posadzkę. W dalszej części opisano sposób jej wykonania. Po przygotowaniu fundamentów i wypoziomowaniu warstwy nośnej należy ustalić, jaki typ ramy będzie stosowany oraz wybrać metodę ułożenia posadzki. Poszczególne metody różnią się w zależności od tego, czy posadzka ma mieć niski czy wysoki wskaźnik tolerancji.
Metoda ułożenia posadzki opiera się na wykorzystaniu belki zagęszczającej, obsługiwanej przez dwóch operatorów, których zadaniem jest idealne osadzenie betonu w ramie. W tym czasie inni operatorzy wyrównują powierzchnię walcem. Jest to typowa metoda budowy, jednak nawet jeżeli walec może ułatwić wygładzenie powierzchni, to jednak nie zapewnia wymaganego spłaszczenia.
Nie należy wylewać zbyt dużej ilości betonu, aby ciężkie grudy i domieszki nie wpadły do dolnej części nawierzchni lub warstwy. Aby zapewnić wąskie tolerancje na powierzchni wykończenia bez konieczności wykonywania dodatkowych prac, w betonie nie może być nierównych powierzchni, a w warstwie nośnej dołków.
Należy zachować szczególną ostrożność, aby posadzka była układana przy zachowaniu odpowiedniego wypoziomowania. W przeciwnym razie zapewnienie wymaganych tolerancji jest stopniowo coraz trudniejsze na każdym etapie budowy. Na tę okoliczność ma także wpływ stosowana rama. Posadzkę o stosunkowo niskiej wytrzymałości można wykonać z drewna, jednak jeżeli konieczne są wysokie tolerancje, należy zastosować przynajmniej metalowe boki. Precyzja w prostoliniowości i wyrównaniu terenu zależy bowiem od stosowanej ramy. Im większy jest jej stopień niezawodności, tym lepsze są rezultaty.
Wykonanie odpowiedniej posadzki zależy nie tylko od zastosowania właściwej ramy, lecz także od innego podstawowego czynnika, tzn. od personelu obsługującego oraz jego umiejętności posługiwania się mechanicznymi urządzeniami do zagęszczania i wykończenia.
Typowy sposób wykonania tradycyjnej posadzki polega na ułożeniu pasów betonowych, które znikają w miarę wylewania betonu.
W systemie tym mogą wystąpić dwa problemy w przypadku posadzki o dużej tolerancji:
- Nieuporządkowany dostęp do stref wypełnienia podczas procesu kontroli.
- Fizyczna trudność wykonania pasów. Dlatego konieczne może być zastosowanie wąskich i wydłużonych pasków.
Obecnie możliwe jest wykonanie pasów o długości 9–15 m w miejscach, w których posadzka ma bardzo wysoki wskaźnik tolerancji. Do tego celu niezbędny jest wysoko wyspecjalizowany personel oraz zastosowanie belek zagęszczających, specjalnie zaprojektowanych do tej pracy. Bez względu na to, czy pasy będą wąskie, czy szerokie, najczęściej stosowana metoda polega na wykonaniu naprzemiennych pasów wylewanych i zakrywanych. Resztę uzupełnia się po krótkim okresie utwardzania.
Wytrzymałość, porowatość, łączenie i trwałość posadzki
Oprócz wyżej wymienionych cech konstrukcyjnych, posadzki magazynów muszą posiadać inne właściwości umożliwiające zastosowanie ich do celów, do jakich są przeznaczone.
- Muszą być zatem odporne na ścieranie zgodnie z wymaganiami normy UNE 41008, która wprowadza skalę Mohsa od 0 do 10.
- Muszą być także odporne na ściskanie i wytrzymywać wartości powyżej 500 kg/cm2 w strefach ogólnych. W zależności od stosowanych urządzeń wymagana wytrzymałość posadzki może wynosić nawet 800 kg/cm2 na szynach. Wymagania dotyczące wytrzymałości na zginanie zazwyczaj wynoszą około 150 do 250 kg/cm2.
- Ponadto posadzka musi być odporna na działanie takich czynników jak oleje, smary oraz węglowodory, ponieważ są stosowane w wózkach widłowych i mogą powodować plamy na posadzce. Dopuszczalna porowatość musi być bardzo mała, poniżej 3%.
- Posadzka musi tworzyć jednolitą strukturę razem z warstwą nośną, aby zapobiec osuwaniu się ziemi i ruchom spadkowym, które powodują nierówności na powierzchni.
- Posadzka musi być także trwała i odporna na zużycie. Jednakże nieuniknione jest tworzenie się kolein wraz z upływem czasu, spowodowanych ciągłym ruchem kół (o dużej masie) po tej samej drodze. Koleiny mogą osiągnąć dużą głębokość i spowodować awarie w obiekcie oraz związane z nimi zagrożenia.
Wybranie firmy specjalizującej się w wykonawstwie posadzek wykorzystywanych do wózków wąskokorytarzowych niewątpliwie jest najlepszą gwarancją optymalnego i trwałego obiektu. Oszczędności w tym względzie mogą poważnie zaszkodzić całemu obiektowi. Bardzo kosztowny projekt może zakończyć się niepowodzeniem z powodu oszczędności dokonanych na jednym z pozornie mniej ważnych aspektów, który jednak w praktyce ma duże znaczenie.