Wybór systemów magazynowych dopasowanych do potrzeb klienta wymaga rozpatrzenia wielu kryteriów. W tym artykule poddajemy analizie tylko podstawowe czynniki, ponieważ znajomość ich wpływu na ostatecznie wykorzystany rodzaj składowania ułatwi zrozumienie bardziej szczegółowych zagadnień w tej kwestii.
Istnieją cztery podstawowe kryteria:
- Potrzebna pojemność,
- Potrzebna szybkość,
- Różnorodność i rodzaje magazynowanych produktów,
- Całkowity koszt rozwiązania.
Poniżej wyjaśniono, w jaki sposób każde z nich wpływa na stworzenie obiektu.
Przykład instalacji, w której zastosowano rózne systemy magazynowania.
Potrzebna pojemność
W artykule Systemy magazynowe z bezpośrednim dostępem do palet, dotyczącym regałów paletowych, określono pojemności, jakie można osiągnąć w każdym systemie. Jak widać, system wjezdny zapewnia większą pojemność magazynowania, tzn. na dostępnej przestrzeni można zmieścić większą ilość towaru.
Warto zapoznać się z informacjami zawartymi w artykule Różnice w pojemności między systemami magazynowania, ponieważ w systemach wjezdnych mogą wystąpić duże różnice między pojemnością rzeczywistą a pojemnością efektywną z uwagi na dużą liczbę wolnych miejsc paletowych w normalnym przepływie pracy.
Natomiast regały paletowe zapewniają mniejszą pojemność rzeczywistą niż regały wjezdne, jednak jest ona bardzo zbliżona do pojemności efektywnej, pod warunkiem że zastosowano odpowiedni system zarządzania, ponieważ praktycznie nie ma wolnych miejsc paletowych w typowym przepływie pracy.
Maksymalną pojemność efektywną w magazynie paletowym zapewnia system łączący najlepsze cechy obu wyżej wymienionych wariantów: regały paletowe na ruchomych podstawach. Jeżeli stosowany jest właściwy system zarządzania, takie regały umożliwiają dużą pojemność rzeczywistą – podobną do pojemności, jaką zapewniają systemy wjezdne – oraz pojemność efektywną bardzo zbliżoną do pojemności rzeczywistej.
Magazyn firmy zajmującej się sprzedażą płytek podłogowych i ściennych.
Oprócz wykorzystania dostępnej powierzchni należy wziąć pod uwagę również przestrzeń pionową. Z tego powodu, jeżeli przepisy na to zezwalają, warto zastosować systemy magazynowania, które wykorzystują maksymalną wysokość obiektu lub zbudować wysokie, zautomatyzowane magazyny (jak widać na ilustracji powyżej).
Potrzebna szybkość
W wielu przypadkach konieczne jest wykonanie operacji w możliwie najkrótszym czasie, w szczególności jeżeli jest to obiekt duży lub średni. Liczba koniecznych operacji jest bezpośrednio związana z tym kryterium, a zatem z dodatkowym kosztem każdej zrealizowanej operacji.
Aby ustalić czas wykonania każdego zadania, należy obliczyć czas potrzebny na przebycie odległości między punktem początkowym a położeniem towaru i dodać do niego czas powrotu, chyba że jest to ruch połączony (wykorzystuje się przemieszczenie konieczne do zdjęcia towaru w celu odłożenia innego lub na odwrót). W takim przypadku poszczególne czasy mierzy się oddzielnie.
Jeżeli analizowane są różne operacje, okazuje się, że do obsługi towaru paletyzowanego najbardziej dynamicznym i najszybszym systemem magazynowania są regały przepływowe, a następnie regały typu push-back. Najszybszym wariantem są regały przepływowe grawitacyjne, następnie zaś regały paletowe. Pośrodku znajdują się rozwiązania na ruchomych podstawach oraz systemy z Pallet Shuttle, jednak rezultat zależy od liczby kolejnych operacji wykonywanych w każdym korytarzu.
Natomiast magazyny automatyczne są szybkie, jeżeli programowanie zadań jest prawidłowo zaplanowane.
Różnorodność i rodzaje produktów
W tym kryterium adekwatność przyjętego rozwiązania opiera się na różnorodności referencji, liczby palet lub pojemników na produkt oraz na czasie przebywania towaru w magazynie.
Jeżeli towary są składowane na paletach oraz istnieje wiele referencji i niewiele palet dla każdej z nich, idealnym systemem magazynowania są regały paletowe statyczne, jednak inne dobre rozwiązanie polega na ich zamontowaniu na ruchomych podstawach.
W przypadku gdy sytuacja jest odwrotna, tzn. jest niewiele referencji i wiele palet dla każdej z nich, każdy system wjezdny jest odpowiedni. A jeśli ponadto towary będą składowane przez dłuższy czas bez zmiany położenia, również warto skorzystać z regałów wjezdnych.
Jeżeli towar jest magazynowany w pojemnikach lub jest układany luzem w szczególnych lokalizacjach, możliwe jest zastosowanie rozwiązań magazynowych dla poszczególnych produktów luzem, z wyjątkiem produktów nietypowych.
Oprócz powyższych założeń wyznacznikiem stosowanego systemu może być również rotacja. Dla produktów A (dużej konsumpcji) składowanych na paletach każdy system magazynowania jest dobry, głównie zaś system wjezdny. Zazwyczaj regały wjezdne są stosowane do produktów A, jednak należy wziąć pod uwagę, że na wykonanie manewrów potrzeba więcej czasu.
Odnośnie produktów B (średniej konsumpcji) najlepsze metody to regały paletowe, regały typu push-back oraz regały przepływowe o niewielkiej głębokości.
Całkowity koszt
Czwartym czynnikiem, jaki należy uwzględnić przy wyborze danego rozwiązania magazynowego, jest koszt związany z jego zamontowaniem i eksploatacją. Ostatecznym celem jest umożliwienie generowania zysków dla firmy.
Aby firma mogła być konkurencyjna, koszty związane z operacjami muszą być jak najmniejsze. Należy również oszacować okres zwrotu inwestycji (ROI), który również powinien być jak najkrótszy. Niektóre firmy zasadniczo nie podejmują pewnych inwestycji, jeżeli okres zwrotu inwestycji wynosi więcej niż trzy lata.
W związku z tym w większości przypadków wybiera się rozwiązanie, które zapewnia bardziej konkurencyjne ceny i krótszy okres zwrotu inwestycji. Ponadto klient powinien także posiadać odpowiednią zdolność finansową dla wybranego rozwiązania.
Dobór właściwego systemu magazynowania, najbardziej odpowiednie przepływy, sposób pracy, wybór lokalizacji magazynu itp. mają duże znaczenie odnośnie finansowania magazynu. Niemniej jednak czynnikiem, który ma największy wpływ na to kryterium, jest rozwiązanie przyjęte do realizacji kompletacji lub przygotowania zamówień.
Zamieszczona poniżej tabela przedstawia schematyczne porównanie różnych rozwiązań paletowych, jednak podano tylko te czynniki, które mogą mieć największy wpływ. Końcowa punktacja służy tylko do pomiaru zalet lub wad danego systemu, jednak nie oznacza to, że system, który otrzymał najwięcej punktów, jest zawsze najlepszy. W każdym przypadku jest jakiś system, który będzie bardziej odpowiedni od innego. Do opracowania tego porównania nie uwzględniono operacji kompletacyjnych tylko magazynowanie palet, dostępność i pojemność.
TABELA PORÓWNAWCZA RÓŻNYCH SYSTEMÓW MAGAZYNOWANIA |
Systemy magazynowania z dostępem bezpośrednim |
|
Regały
paletowe
|
Regały przesuwne |
Regały paletowe z podwójną głębokością |
Regały paletowe wąskokorytarzowe |
Regały paletowe automatyczne |
Regały paletowe automatyczne z podwójną głębokością |
Wykorzystanie powierzchni
|
2 |
5 |
3 |
3 |
3 |
4 |
Wykorzystanie
objętości
|
2 |
4 |
3 |
3 |
3 |
3 |
Dostęp do każdej palety |
5 |
5 |
2 |
5 |
5 |
4(A) |
Szybkość dostępu/operatywność
(liczba ruchów na godzinę) |
4 |
3 |
2(B) |
3 |
5(C) |
4(A) |
Rotacja stanu magazynowego |
4(D) |
4(D) |
2(B) |
4(D) |
5 |
4(A) |
FIFO |
FIFO |
FIFO (częściowy) |
FIFO |
FIFO |
FIFO (częściowy) |
Wysokość ostatniego poziomu (m) |
2 |
2 |
1 |
3 |
5 |
4 |
<10 |
<10 |
<8 |
<14 |
<45 |
<40 |
Szerokość korytarzy (m) |
3 |
2 |
3 |
4 |
5 |
5 |
2,20/3,50 (E) |
3,00/3,50 (E) |
3,00 (E) |
1,55/1,80(F) |
1,55 |
1,55 |
Inwestycja początkowa |
4 (niewielka) |
3 (średnia) |
4 (niewielka) |
3 (średnia) |
2 (duża) |
2 (duża) |
Urządzenia przeładunkowe (wózek) |
·Podnośnikowy
·Z wysuwanym masztem
·Z przeciwwagą
|
·Z wysuwanym masztem
·Z przeciwwagą
|
·Z wysuwanym masztem,
specjalny
|
·Systemowy trójstronny
·Systemowy dwustronny
|
·Układnica |
·Układnica |
Korzyści (punktacja średnia)* |
3,25 |
3,50 |
2,50 |
3,50 |
4,12 |
3,75 |
TABELA PORÓWNAWCZA RÓŻNYCH SYSTEMÓW MAGAZYNOWANIA |
Systemy magazynowania akumulacyjnego |
|
Regały paletowe
wjezdne
|
Push-back z wózkami |
Push-back z rolkami |
Półautomatyczny Pallet Shuttle |
Regały przepływowe z rolkami |
Pallet-Shuttle
z rozwiązaniem automatycznym
|
Regał przepływowe z rolkami z rozwiązaniem automatycznym |
Wykorzystanie powierzchni |
5 |
4 |
4 |
5 |
5 |
5 |
5 |
Wykorzystanie
objętości
|
5 |
4 |
4 |
4 |
4 |
4 |
4 |
Dostęp do każdej palety |
1 |
2 |
2 |
1 |
2 |
2 |
2 |
Szybkość dostępu/operatywność
(liczba ruchów na godzinę) |
2 |
3 |
3 |
3 |
4 |
4 |
5 |
Rotacja stanu magazynowego |
1 |
2 |
2 |
2 |
5 |
2 |
5 |
LIFO |
LIFO |
LIFO |
LIFO |
FIFO |
LIFO |
FIFO |
Wysokość ostatniego poziomu (m) |
2 |
1 |
1 |
2 |
3 |
3 |
4 |
<10 |
<7,5 |
<7,5 |
<10(E) |
<14(E) |
<40 |
<40(G) |
Szerokość korytarzy (m) |
2 |
2 |
2 |
2 |
3 |
4 |
4 |
3,00/3,50(H) |
3,00/3,50(H) |
3,00/3,50(H) |
3,00/3,50(H) |
1,80/3,50(H) |
1,55 |
1,55 |
Inwestycja początkowa |
4 (niewielka) |
3 (średnia) |
3 (średnia) |
3 (średnia) |
2 (duża) |
2 (duża) |
1 (bardzo duża) |
Urządzenia przeładunkowe (wózek) |
·Z wysuwanym masztem
·Z przeciwwagą
|
·Z wysuwanym masztem
·Z przeciwwagą
|
·Z wysuwanym masztem
·Z przeciwwagą
|
·Z wysuwanym masztem
·Z przeciwwagą
·Systemowy trójstronny
|
·Z wysuwanym masztem
·Z przeciwwagą
·Systemowy trójstronny
|
·Układnica |
·Układnica |
Korzyści (punktacja średnia)* |
2,75 |
2,62 |
2,62 |
2,75 |
3,50 |
3,40 |
3,75 |
PUNKTACJA: 1 (niska) – 6 (bardzo wysoka). W „Inwestycji początkowej” wartości zostały odwrócone.
* Średnia uzyskana z ośmiu zmiennych numerycznych.
(A) Z WMS i modułem relokacji.
(B) Z WMS i zarządzaniem A-B-C może być większa.
(C) Zaprogramowana operacja.
(D) Z odpowiednim WMS.
(E) Zależy od wózka.
(F) Zależy od tego, czy jest to wózek systemowy dwustronny, czy trójstronny.
(G) Należy koniecznie zapewnić bardzo dobrą jakość palet.
(H) Zależy od wózka i synchronizacji w korytarzu.
Połączenie kryteriów
Często tworzone są obiekty, w przypadku których uwzględniono kilka wyżej wymienionych kryteriów. Zazwyczaj wdrażane są także różne systemy magazynowania odpowiednie dla danego typu produktu.
W artykule Systemy mieszane przedstawiono kilka przykładów, w których połączono regały paletowe, regały na ruchomych podstawach, regały wjezdne, systemy przepływowe, a także zamontowano przenośniki rolkowe w celu skrócenia czasu manewrów.
Połączenie kryteriów i rozwiązań magazynowych umożliwia stworzenie wyjątkowych obiektów, maksymalnie dostosowanych do konkretnych potrzeb wykorzystujących je firm.
Optymalizacja kryteriów w magazynach automatycznych
Tabele powyżej pokazują, że automatyczne systemy magazynowania mają wpływ na optymalizację podstawowych kryteriów. Jedyną wadą jest ich większy koszt początkowy, ale oferują wiele korzyści, takich jak duża pojemność magazynowa, większa wysokość konstrukcyjna, idealna kontrola i zarządzanie, wysoka wydajność przyjęć i wydań (w pełni zautomatyzowanych), minimalne zapotrzebowanie personelu, większa dostępność do produktów, łatwiejsza rotacja itd.
Magazyn firmy zajmującej się dystrybucją produktów kosmetycznych.
Systemy automatyczne mogą być stosowane tylko do lokalizacji towarów, do transportu wewnętrznego lub do obu tych celów. Zazwyczaj występuje ta druga możliwość, ponieważ znacznie zwiększa się liczba ruchów możliwych do wykonania, a ponadto operatorzy tylko zajmują się załadunkiem i rozładunkiem samochodów ciężarowych lub kontenerów.
W całkowicie zautomatyzowanych rozwiązaniach montowane są odpowiednie przenośniki w strefie doków. Przenośniki te na ogół są przygotowane do pracy z wózkami paletowymi. System ten jest stosowany w obszarze wydań oraz przyjęć, jednak w przypadku przyjęć konieczne jest wprowadzenie stanowisk do kontroli wymiarów i palet w celu zapewnienia sprawnej pracy maszyn i urządzeń automatycznych.
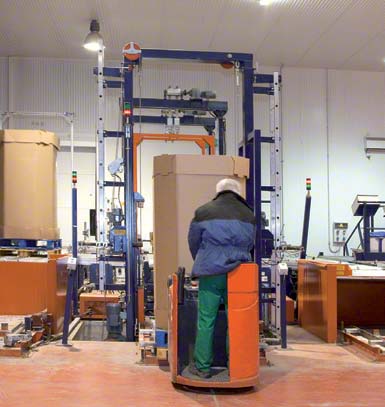 |
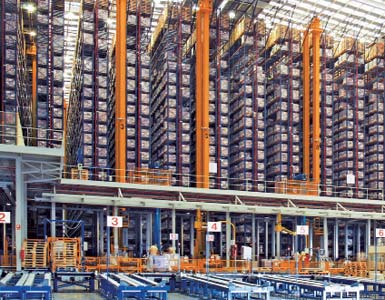 |
Wejście do stanowiska kontroli w magazynie automatycznym |
Magazyn automatyczny |