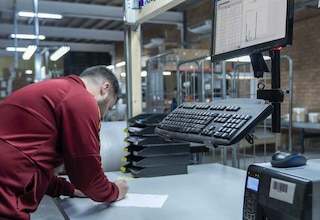
Proces ciągłego doskonalenia i jego zastosowanie w logistyce
Celem procesu ciągłego doskonalenia w logistyce jest zwiększenie jakości produktu lub wydajności procesu za pomocą ciągłej analizy kluczowych wskaźników i parametrów. Ta wywodząca się z Japonii technika zyskuje coraz większą popularność w zachodnich firmach. Proces ciągłego doskonalenia umożliwia zwiększenie efektywności przedsiębiorstw dzięki wdrażaniu niewielkich, lecz ciągłych zmian, których celem jest wyeliminowanie praktyk niezapewniających wysokiej rentowności oraz ujednolicenie stosowanych procedur.
W niniejszym artykule analizujemy, na czym polega proces ciągłego doskonalenia, jakie najważniejsze strategie stosowane są w jego ramach oraz w jaki sposób można go wykorzystać w sektorze logistyki.
Czym jest proces ciągłego doskonalenia?
Techniki ciągłego doskonalenia stanowią zbiór strategii, których celem jest doskonalenie i optymalizacja procedur, produktów lub usług za pomocą działań korygujących wynikających z dogłębnego poznania prowadzonych operacji oraz analizy danych.
Istnieje wiele sposobów wykorzystywania strategii ciągłego doskonalenia w celu zwiększania wydajności obiektu. Jednak pośród rozwiązań cieszących się największą popularnością warto wyróżnić metodę Kaizen lub 5S ze względu na prostotę, a zarazem skuteczność działania.
Proces ciągłego doskonalenia przy użyciu metody Kaizen
Kaizen (w języku japońskim „zmiana w celu poprawy”) to system opracowany przez m.in. japońskiego inżyniera Taiichiego Ohno na rzecz producenta samochodów Toyota po zakończeniu II wojny światowej. Celem systemu miało być zwiększenie konkurencyjności firmy, aby plasowała się ona na równi z amerykańskimi przedsiębiorstwami. Obecnie zaś stanowi powszechnie stosowany standard zarządzania przedsiębiorstwem na całym świecie.
U podstaw metody Kaizen leży założenie, zgodnie z którym pomimo poprawnej realizacji danego procesu zgodnie z wyznaczonym celem zawsze istnieje możliwość jego poprawy. Szczególnie w dziedzinie produkcji i logistyki strategia ta wykorzystuje szereg procedur do analizy funkcjonowania przedsiębiorstwa, wykrywania nieefektywnych obszarów działalności i wdrażania zmian. Wszystkim rządzi pięć zasad, znanych z języka japońskiego jako 5S:
- Seire (sortowanie): pierwszy proces w ramach metody Kaizen polega na selekcji czynności generującą prawdziwą wartość dodaną w zakresie danego produktu lub usługi (tzw. gemba).
- Seiton (systematyzacja): pracownik powinien dysponować wszelkimi przydatnymi narzędziami umożliwiającymi sprawną i wydajną pracę. Zasada seiton polega na uporządkowaniu wyposażenia roboczego w celu uniknięcia ruchu lub czynności zmniejszających wydajność pracy.
- Seiso (sprzątanie): określenie błędów i uporządkowanie stanowiska pracy mają kluczowe znaczenie dla wygody pracownika i maksymalnej wydajności wykonywanej przez niego pracy.
- Seiketsu (standaryzacja): po określeniu błędów należy ustanowić niezbędne zasady lub standardy umożliwiające zwiększenie efektywności prowadzonych procesów.
- Shitsuke (samodyscyplina): ten ostatni etap ma nadrzędne znaczenie dla skuteczności czterech poprzednich. Oznacza zaangażowanie całej organizacji na rzecz wdrożenia nowych zasad i przyjęcia filozofii ciągłego doskonalenia w celu zwiększenia wartości wszystkich wykonywanych czynności w firmie.
Metoda Kaizen stanowi idealną strategię umożliwiającą zwiększenie rentowności organizacji, określenie i wyeliminowanie wszelkich braków pod względem efektywności, a przede wszystkim wsparcie wszystkich działań przyczyniających się do generowania wartości.
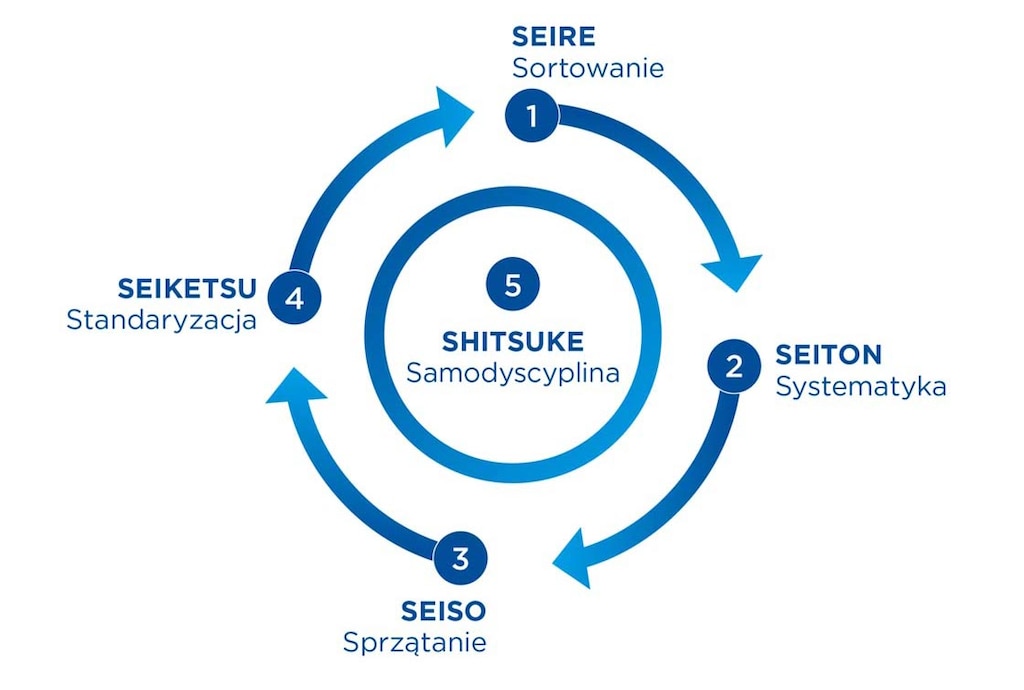
Inne sposoby ciągłego doskonalenia – od PDCA po Six Sigma
Oprócz metody 5S istnieją inne strategie i narzędzia stosowane do ciągłego doskonalenia. Ich założeniem jest optymalizacja prowadzonych procesów przy wykorzystaniu generowanych informacji. Oto dwie inne ważne metody stosowane w celu standaryzacji procesu ciągłego doskonalenia:
- Cykl Deminga (PDCA): PDCA stanowi skrót angielskiego zwrotu „Plan, Do, Check, Act”. Ta cykliczna strategia opisuje cztery niezbędne kroki w celu wykrywania nieefektywnych sposobów pracy, planowania rozwiązań, a ostatecznie poprawy rentowności wszystkich operacji prowadzonych w magazynie.
- Six Sigma: technika ta polega na eliminacji błędów popełnianych podczas doręczania produktu gotowego klientowi. Celem strategii jest osiągnięcie maksymalnie 3-4 błędów na milion możliwości, gdzie za błędy uznaje się wszelkie zdarzenia mające wpływ na poziom zadowolenia klienta.
- Metodologia Lean: strategia Lean polega na identyfikowaniu wszystkich etapów niedostarczających wartości dodanej produktom końcowym w celu uzyskania maksymalnej jakości produktu.
W toku ciągłego doskonalenia nie trzeba decydować się tylko na jedną metodę, ponieważ nie istnieją rozwiązania lepsze i gorsze. Wszystkie wzajemnie się uzupełniają, a każde dostarcza określonych korzyści w innych warunkach, dlatego należy je stosować jednocześnie. Nadrzędnym celem jest doskonalenie: ograniczenie nieefektywnych sposobów pracy, wprowadzenie progresywnych zmian i zapewnienie prawidłowego wdrażania nowych praktyk w całej organizacji.
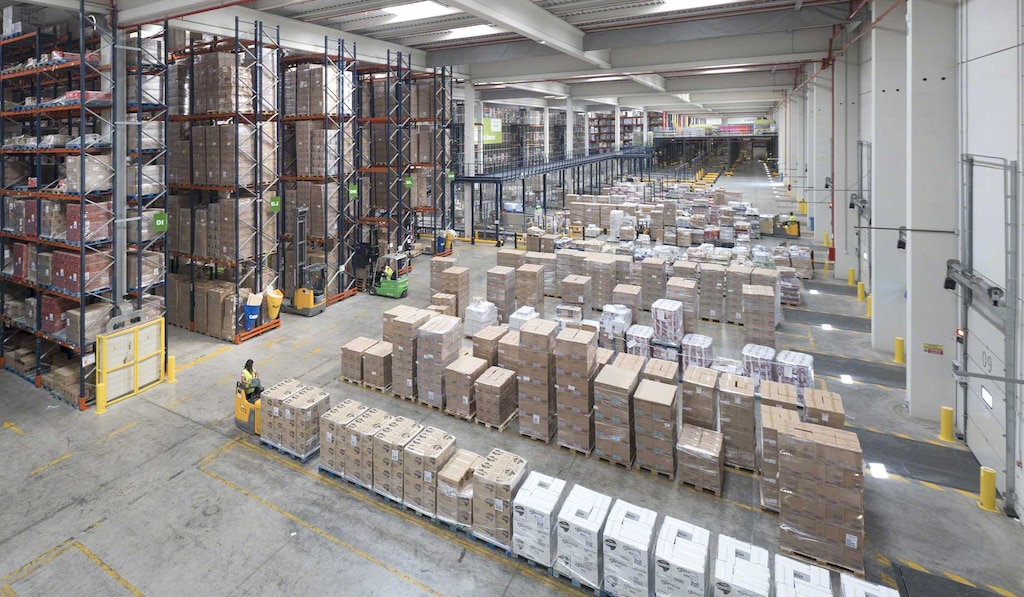
Marnotrawstwo – muda, mura, muri
Techniki ciągłego doskonalenia obejmują nieustanną analizę procesów w celu zapewnienia maksymalnej rentowności poszczególnych etapów. Przykładowo pojęcia muda, mura i muri nawiązują do strategii identyfikacji błędów i marnotrawionych surowców podczas produkcji.
System ten, zwany również 3M systemu produkcyjnego firmy Toyota, wykorzystuje analizę błędów i marnotrawionych zasobów w ramach danego procesu produkcyjnego w celu wprowadzania zmian w organizacji, aby zagwarantować bezbłędną produkcję i jak najlepsze wrażenie klienta z jakości produktu i poziomu obsługi. Oto trzy kluczowe założenia systemu:
- Muda (marnotrawstwo): pojęcie to obejmuje błędy prowadzące do zużycia zasobów bez generowania wartości dodanej w ramach produktu końcowego. Pierwotnie metodologia stosowana przez firmę Toyota dotyczyła 7 aspektów marnotrawstwa, które zwykle można zaobserwować w zakładzie produkcyjnym: zbędne ruchy, nadmierne zapasy, powtarzalne czynności, nadmierna produkcja, przestoje pomiędzy liniami produkcyjnymi, zbyt duża liczba procesów (procedury niezapewniające wartości dodanej) oraz nieefektywny transport.
- Mura (nieregularność): kierownik produkcji musi wykryć wszelkie zaburzenia równowagi, przerwy lub zmiany w zakresie nakładów roboczych, pociągające za sobą nadmierne koszty obsługi linii produkcyjnych. Niezbędna jest zatem dokładna kontrola wydajności procesów produkcyjnych w celu wykrywania wad, błędów lub niezgodności. Jak wyeliminować wykryte nieprawidłowości? Przez wdrożenie metodologii dostosowujących produkcję do zapotrzebowania, na przykład metody Kanban lub just-in-time.
- Muri (przeciążenie): połączenie muda i mura (marnotrawstwa i błędów) skutkuje powstaniem muri, które w języku japońskim oznacza stres. Niewłaściwe planowanie skutkuje zmęczeniem operatorów lub nawet powstawaniem wąskich gardeł na liniach produkcyjnych.
Skrupulatne stosowanie reguł 3M firmy Toyota umożliwia wyeliminowanie nieracjonalnego gospodarowania zasobami podczas produkcji oraz zmian i braków równowagi w zakresie nakładów roboczych. Wszystko to, czyli likwidacja muda i mura, przekłada się na wyeliminowanie muri, czyli stresu i niestabilności na liniach produkcyjnych.
Zalety wdrożenia procesu ciągłego doskonalenia w logistyce magazynowej
W jaki sposób proces ciągłego doskonalenia może wspomóc działalność logistyczną i codzienną pracę magazynu? Oto główne zalety:
- Gwarancja wysokiej jakości produktu/usługi: wdrożenie techniki ciągłego doskonalenia gwarantuje skuteczność realizacji takich etapów, jak produkcja czy logistyka, co prowadzi do zapewnienia lepszego doświadczenia klientom.
- Ograniczenie kosztów logistycznych: strategia ta umożliwia przechowywanie optymalnej ilości zapasów w magazynie, skrócenie czasu realizacji dostaw zaopatrzenia (tzw. lead time), priorytetowe traktowanie najbardziej wydajnych operacji i wyeliminowanie tych, które nie zapewniają wartości dodanej.
- Efektywność obsługi: takie metody jak Kaizen lub PDCA umożliwiają wyeliminowanie zbędnych manewrów i wyznaczenie najbardziej optymalnych tras kompletacji, gwarantując zwiększenie wydajności operatorów.
Oprócz wspomnianych usprawnień zastosowanie powyższych systemów ułatwia wdrożenie strategii pull flow w obiekcie. Co to oznacza? Strategia ta zakłada prowadzenie czynności w magazynie na zasadzie JIT (just-in-time), a zatem w momencie wystąpienia zapotrzebowania po stronie klienta, unikając nieefektywnych operacji oraz ryzyka zgromadzenia zapasu nadmiernego lub pogorszenia jakości towaru w wyniku długotrwałego składowania.
Firma Mecalux posiada w tym zakresie wiele rozwiązań towarzyszących wdrażaniu metod ciągłego doskonalenia (Kaizen czy PDCA), jak np. moduł Supply Chain Analytics Software. Jest to zaawansowana funkcja oprogramowania Easy WMS umożliwiająca kierownikowi ds. logistyki gromadzenie licznych danych dotyczących magazynu i uporządkowanie tych informacji w celu określenia istotnych KPI logistycznych oraz pomiaru wpływu przyjętej strategii ciągłego doskonalenia.
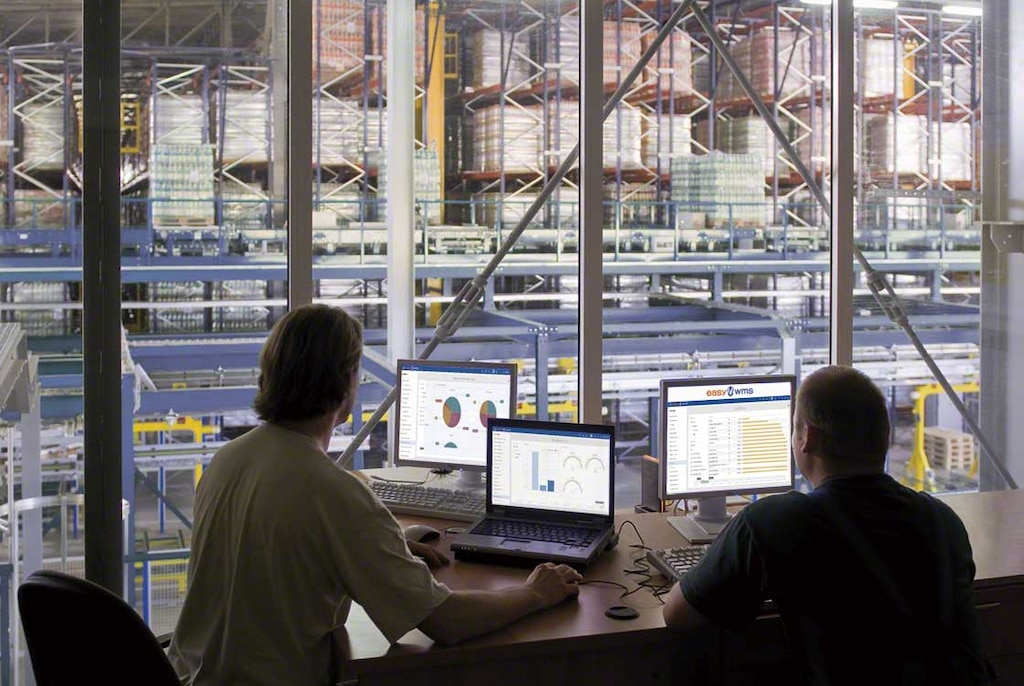
Proces ciągłego doskonalenia w logistyce gwarancją konkurencyjności
Ewolucja branży logistycznej z roku na rok nabiera tempa. Powstaje szereg technologii, których zadaniem jest wprowadzenie ciągłych ulepszeń zwiększających konkurencyjność przedsiębiorstw i podnoszących efektywności ich codziennej pracy.
Pierwszym krokiem w kierunku poprawy wydajności łańcucha dostaw jest monitorowanie i analiza KPI magazynu w celu określenia braków i eliminacji procesów nieefektywnych. Wdrożenie strategii ciągłego doskonalenia w firmie jest jedynym sposobem na ograniczenie kosztów logistycznych i optymalizację wykorzystania dostępnych zasobów.
Jeżeli chcesz zmaksymalizować wydajność swojego magazynu, skontaktuj się z nami, a nasi specjaliści znajdą rozwiązanie, które pozwoli efektywnie zarządzać procesami logistycznymi w Twojej organizacji.