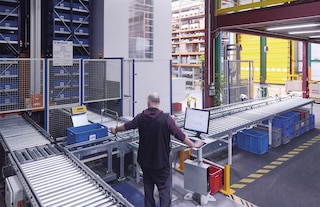
Zastosowanie cyklu Deminga (PDCA) w logistyce
Cykl Deminga, zwany również cyklem PDCA (ang. Plan, Do, Check and Act), jest metodą zarządzania jakością pozwalającą na prowadzenie strategii ciągłego doskonalenia w firmie, która ułatwia rozwiązywanie problemów w uporządkowany i systematyczny sposób.
Strategia ta składa się z czterech zasadniczych etapów: planowanie, wykonanie, sprawdzenie i korygowanie.
Nazwa cyklu pochodzi od nazwiska amerykańskiego konsultanta, który upowszechnił tę metodę pracy, Williama Edwardsa Deminga, chociaż jej opracowanie przypisuje się jego mentorowi, Walterowi Shewhartowi. W latach pięćdziesiątych XX wieku Deming, specjalista od systemów zarządzania jakością i ekspert w dziedzinie statystyki, podjął współpracę z gronem inżynierów i naukowców w celu zastosowania koła PDCA w japońskich przedsiębiorstwach. Jednak dopiero trzy dekady później jego metodologia ukierunkowana na jakość w ujęciu łącznym zadomowiła się w amerykańskim przemyśle.
Co to jest cykl Deminga?
Cykl Deminga, zwany również spiralą ciągłego doskonalenia, jest metodologią ukierunkowaną na doskonalenie procesu poprzez ustalanie i korygowanie przyczyn występujących problemów. Zwykle cykl Deminga przedstawiany jest w formie koła, ponieważ uważany jest za proces powtarzalny. Wygląda następująco:
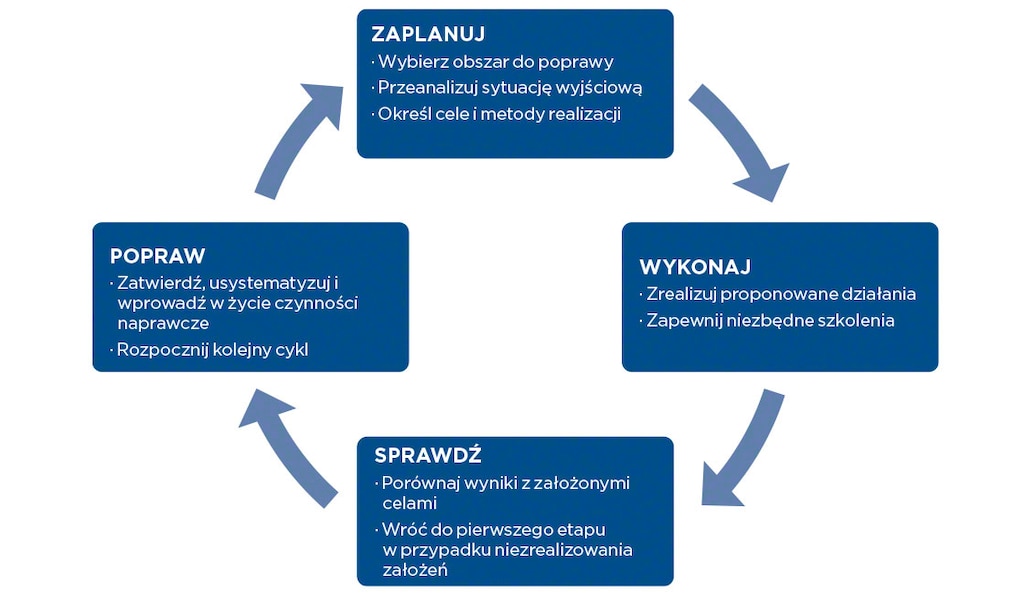
Cykl Deminga obejmuje: planowanie czynności umożliwiającej poprawę powtarzającego się problemu, kontrolowane wykonanie opracowanego rozwiązania, późniejszą analizę działania celem określenia rozbieżności między planem a realizacją oraz, na koniec, usystematyzowanie zmiany korygującej w celu ugruntowania nowego, zoptymalizowanego procesu w działalności firmy.
4 etapy koła Deminga stosowane w logistyce
W dalszej części artykułu szczegółowo omawiamy poszczególne etapy cyklu Deminga:
1. Planowanie
Celem tego etapu jest określenie problemu lub procesu wymagającego usprawnienia. W logistyce do zagadnień, które warto poddać cyklowi Deminga, możemy zaliczyć między innymi: błędy na etapach kompletacji i pakowania, opóźnienia w przygotowywaniu zamówień, wysoki odsetek zwrotów lub doręczanie uszkodzonych przesyłek. Dokładna kontrola magazynu wykorzystująca określone wskaźniki jest niezbędna w celu identyfikacji obszarów, które nie funkcjonują prawidłowo.
Ten etap cyklu Deminga można podzielić na trzy procesy podrzędne:
1. Określenie obszaru poprawy i analiza sytuacji wyjściowej: należy położyć nacisk na przyczyny prowadzące do powstania problemu i gruntownie przeanalizować jego pochodzenie. W tym celu może być przydatna zasada Pareta. Mimo że zwykle stosowana jest w odniesieniu do klasyfikacji towaru w magazynie za pomocą analizy ABC, zasada ta może sprawdzić się również do ustalenia priorytetów w przypadku danego problemu logistycznego. Zazwyczaj większość negatywnych skutków danego zdarzenia (ok. 80%) ma ograniczoną liczbę przyczyn (ok. 20%).
2. Zdefiniowanie wymiernych celów: cele powinny być szczegółowe, możliwe do osiągnięcia, istotne i ukierunkowane na efekty. Należy również wyznaczyć przedział czasowy poświęcony ich ocenie. Cele mogą opierać się na danych historycznych odnotowanych przez firmę na podstawie kluczowych wskaźników efektywności (KPI) lub też na danych sektorowych pozyskanych w procesie zestawiania parametrów w odniesieniu do konkurencji (benchmarking).
3. Opracowanie planu działania: obejmuje analizę i wybór optymalnych rozwiązań umożliwiających skorygowanie sytuacji, wyznaczenie osób odpowiedzialnych za poszczególne działania oraz wskazanie terminów realizacji. Plan może powstać jako test pilotażowy, który następnie, w przypadku osiągnięcia zadowalających rezultatów, zostanie wdrożony w pozostałych obszarach firmy.
2. Wykonanie
Etap „wykonania” w ramach cyklu Deminga znany jest również jako etap testowy. Polega na realizacji wybranego działania i wyeliminowaniu przyczyn powstałego problemu. Aby etap ten przebiegł bez zakłóceń, warto przygotować wytyczne dla zaangażowanych w ten proces pracowników i zapewnić im niezbędne szkolenie, a także odnotować wszelkie odchylenia od planowanych założeń.
3. Weryfikacja
Polega na ocenie efektów w drodze porównania realizacji z opracowanym planem. Zgromadzone dane zwykle przedstawiane są za pomocą wykresów i diagramów przy użyciu narzędzi do prezentacji danych. Istotne jest przestrzeganie wyznaczonych uprzednio terminów, aby nie przeprowadzić analizy zbyt szybko i uniknąć wyciągania pochopnych wniosków.
Po dokonaniu oceny efektów istnieją dwie możliwości:
- Cel został osiągnięty, zatem można przejść do kolejnego etapu (weryfikacji) cyklu Deminga. Należy koniecznie zweryfikować pozostałe wskaźniki, aby uniknąć „niepożądanych skutków”, tzn. upewnić się, że nie powstały nowe lub nie pogłębiły się dotychczasowe problemy w innych obszarach.
- Cel nie został osiągnięty: jeżeli przyczyną jest nieodpowiednia realizacja opracowanego planu, należy wrócić do poprzedniego etapu i szczegółowo przeanalizować jego przebieg. W przypadku odrzucenia takiej możliwości należy przejść do początku koła Deminga i ponownie przeanalizować przyczyny prowadzące do występowania problemu.
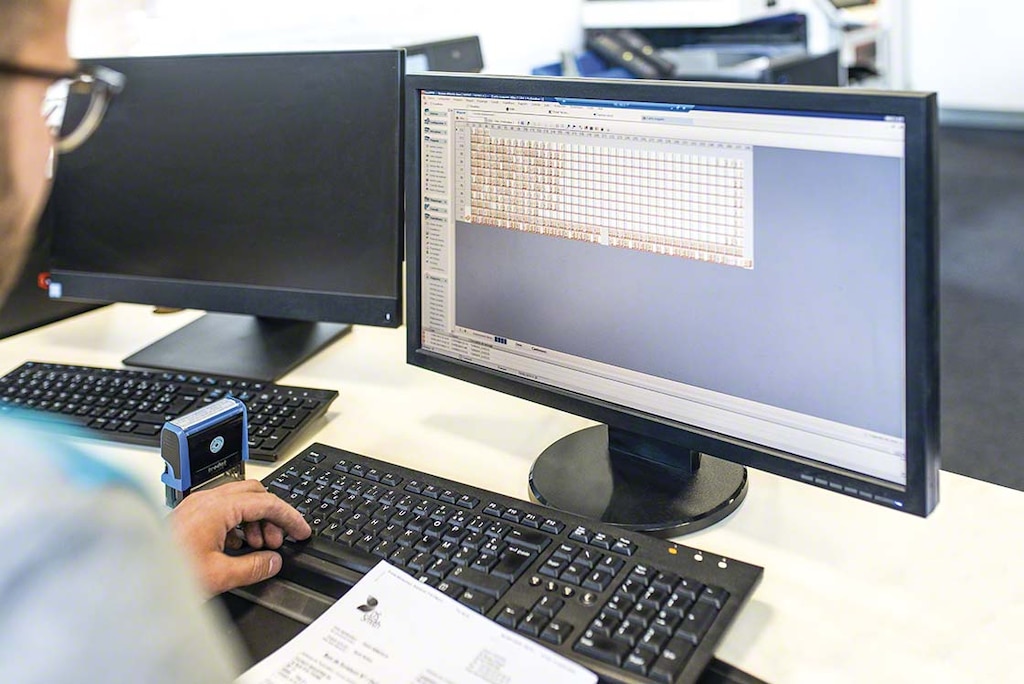
4. Dostosowanie
Po zweryfikowaniu skuteczności cyklu należy udokumentować zmianę, ujednolicić ją i objąć kontrolą. Zaleca się udostępnić personelowi wszystkie niezbędne informacje, organizując na przykład kilka sesji szkoleniowych. W celu dokładnego monitorowania nowych procesów należy również określić KPI podlegające szczegółowej kontroli.
Ponadto po zweryfikowaniu użycia nowych narzędzi, należy zalecić ich powszechne stosowanie. Dla przykładu, jeśli test pilotażowy przy użyciu urządzeń do kompletacji głosowej (pick by voice) zakończy się sukcesem w postaci ograniczenia liczby błędów popełnianych podczas przygotowywania zamówień, warto przekazać kierownikom logistyki, aby polecili wszystkim operatorom wykorzystywanie tych narzędzi.
Zalety cyklu Deminga
Poniżej wskazujemy najistotniejsze korzyści wynikające z zastosowania cyklu Deminga:
- Dostarcza jednolitą metodykę możliwą do zastosowania w dowolnym obszarze firmy w celu rozwiązywania powtarzających się problemów.
- Zapewnia oszczędność czasu na etapie poszukiwania najskuteczniejszego rozwiązania.
- Zawiera zbiór kompleksowych instrukcji niezbędnych do zapewnienia pełnej realizacji danego przedsięwzięcia.
- Gwarantuje szczegółową analizę najczęstszych błędów w celu ich wyeliminowania.
- Służy do kontroli i dokumentowania wdrażania nowych procesów.
- Cykl Deminga stanowi przewodnik postępowania umożliwiający wyeliminowanie przyczyn problemu, niezależnie od zmian zachodzących na poziomie personelu.
- Sprzyja pracy zespołowej dzięki aktywnemu udziałowi wszystkich zaangażowanych osób.
W jaki sposób cykl Deminga poprawia jakość procesów logistycznych firmy?
W sektorze logistyki jakość oznacza zaspokajanie potrzeb klienta bez kompromisów w obszarze poziomu obsługi, po możliwie najniższych kosztach. Kluczem do sukcesu jest wypracowanie optymalnej równowagi między poziomem kosztów a jakością świadczonych usług.
Koszty jakości i konsekwencje jej braku
Zgodnie z tą koncepcją istnieją dwa rodzaje kosztów:
- Koszty jakości – są związane z utrzymaniem wymaganego przez klientów poziomu obsługi. Przykładowo, są to nakłady ponoszone w związku z wdrożeniem planu konserwacji zapobiegawczej w magazynie z myślą o odpowiedniej ochronie wykorzystywanych systemów.
- Koszty braku jakości – powstają w wyniku niezapewnienia odpowiedniej jakości procesów. Przykładem mogą być straty wynikające z przestojów lub awarii maszyn.
Narzędzia umożliwiające skuteczne zarządzanie magazynem
Poprawa jakości jest stałym celem procesów logistycznych, ponieważ przekłada się na zwiększenie wydajności. Dążeniem wielu przedsiębiorstw jest eliminacja czynności powtarzanych bez potrzeby. Operacje powinny być wykonywane „raz, a dobrze”. W tym kontekście wdrożenie cyklu Deminga do czynności magazynowych w istotny sposób zwiększa wydajność procesów logistycznych firmy.
Optymalizacja wszystkich procesów zachodzących w obiekcie może zostać przeprowadzona poprzez wdrożenie cyklu Deminga oraz unowocześnienie systemów i wyposażenia. Dzięki instalacji systemu WMS do zarządzania magazynem można usprawnić zastosowanie tej metody, ponieważ oprogramowanie to automatycznie gromadzi i przetwarza ogromne ilości informacji.
Ponadto narzędzia takie jak program Supply Chain Analytics Software ułatwiają analizę tych danych za pomocą paneli sterowania i spersonalizowanych wykresów, przyczyniając się do zwiększenia wydajności kluczowych etapów takich jak przyjęcia i wydania towaru, przygotowywanie zamówień czy zarządzanie asortymentem.
Innowacje technologiczne zwiększają efekty cyklu Deminga
Kluczowym celem zapewnienia jakości w logistyce jest ciągłe doskonalenie obsługi przy maksymalnym ograniczeniu kosztów. Warto wspomnieć, że dwóch na dziesięciu respondentów ankiety „Supply Chain Digital and Analytics Survey” przeprowadzonej przez Deloitte wskazało ograniczenie kosztów logistycznych jako nadrzędny cel warunkujący dobór narzędzi do analizy danych.
Monitorowanie procesów pozwala na kontrolę prawidłowego przebiegu cyklu Deminga, który może sprawdzić się jeszcze lepiej przy zastosowaniu systemów informatycznych. Poznaj już dziś korzyści płynące z wykorzystywania systemu zarządzania magazynem. Skontaktuj się z nami, a zaprezentujemy Ci sposób działania systemu przy użyciu spersonalizowanej wersji demonstracyjnej.