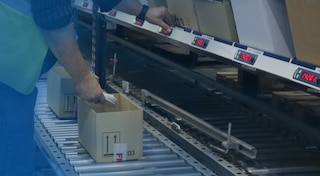
5 przykładów zastosowania metody Poka-Yoke
Poka-Yoke to jedna z technik ciągłego doskonalenia, która ma dwa podstawowe cele. Po pierwsze – zapobieganie nieumyślnym błędom w procesach produkcyjnych i logistycznych, po drugie – korygowanie nieprawidłowości w razie wykrycia ewentualnych problemów.
Przedsiębiorstwa pracujące w modelu sprzedaży omnichannel muszą przygotować wiele zamówień dziennie i dostarczyć je w jak najkrótszym terminie. Dlatego kierownicy magazynów starają się za wszelką cenę zapobiegać pomyłkom, które mogłyby spowodować opóźnienia, a w efekcie zaszkodzić wizerunkowi firmy.
W jaki sposób Poka-Yoke może pomóc wyeliminować pomyłki podczas kompletacji? W niniejszym artykule przybliżamy ten temat na pięciu praktycznych przykładach.
Czym jest Poka-Yoke?
Opracowana w japońskiej fabryce Toyoty w 1960 roku metoda Poka-Yoke oznacza w dosłownym tłumaczeniu „odporność na błędy”. To technika ciągłego doskonalenia pozwalająca uniknąć pomyłek w dowolnym procesie produkcyjnym czy logistycznym.
Poka-Yoke obejmuje m.in. strategie racjonalizacji i optymalizacji procesów w magazynie czy zakładzie produkcyjnym, których przykładem może być zasada 5S zaczerpnięta z metody Kaizen.
Technika ta stosowana jest również przy projektowaniu przedmiotów użytkowych w taki sposób, aby wyeliminować możliwość popełnienia błędu. Dobrze widać to na przykładzie kabli USB do ładowania urządzeń i przesyłu danych. Można je podłączyć tylko w jeden sposób – inaczej nie spełniałyby swojej funkcji.
Metodę Poka-Yoke opracował i z powodzeniem wdrażał japoński inżynier Shigeo Shingo. Jej celem była eliminacja z procesów produkcyjnych operacji nieefektywnych poprzez wprowadzenie praktyk upraszczających pracę i pozwalających skupić się na wykonywanych zadaniach.
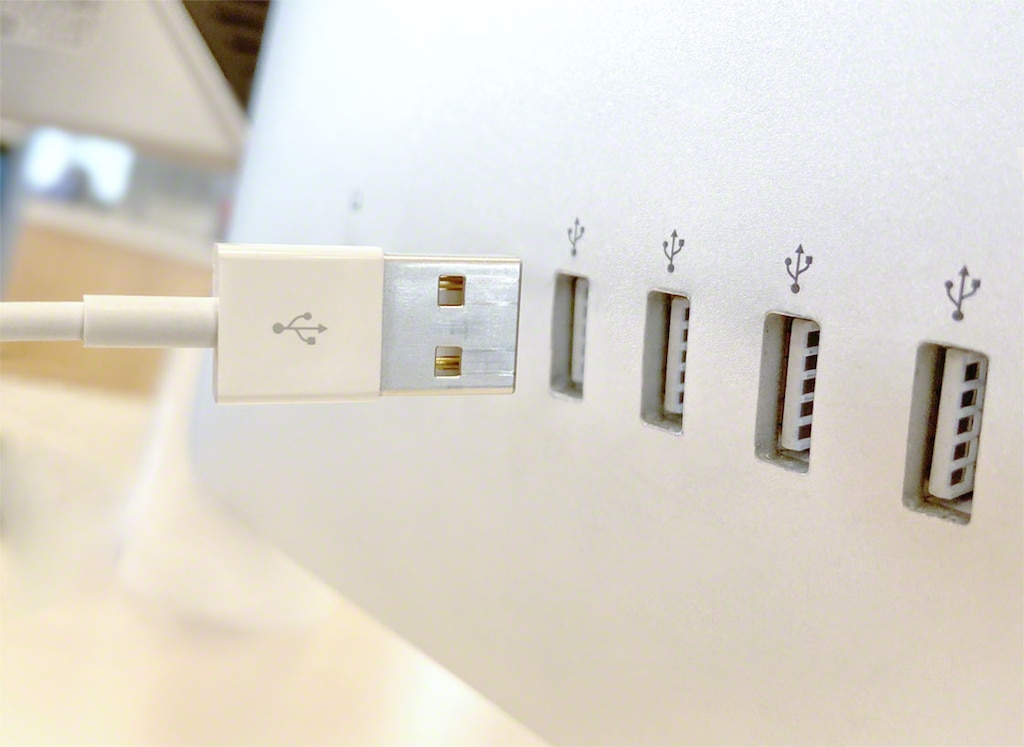
Jak wprowadzić Poka-Yoke?
Jak skutecznie zastosować metodę Poka-Yoke w zakładzie produkcyjnym lub w magazynie? Najlepiej zacząć od gruntownej analizy poszczególnych procesów. Należy przy tym rozpatrzyć kolejno wszystkie ich etapy, zwracając szczególną uwagę na te momenty, w których najłatwiej o błąd.
Następnie należy przyjąć stosowne podejście Poka-Yoke, czyli albo rozwiązanie pozwalające całkowicie wykluczyć pomyłkę, albo przynajmniej zminimalizować prawdopodobieństwo jej popełnienia. Zdarzają się też błędy, których nie da się uniknąć. W takim przypadku należy opracować metody ich wykrywania i reagowania, aby ograniczyć ich ewentualne negatywne skutki.
Na koniec trzeba jeszcze raz przeanalizować proces, aby sprawdzić, czy wdrożenie Poka-Yoke przyniosło oczekiwane rezultaty.
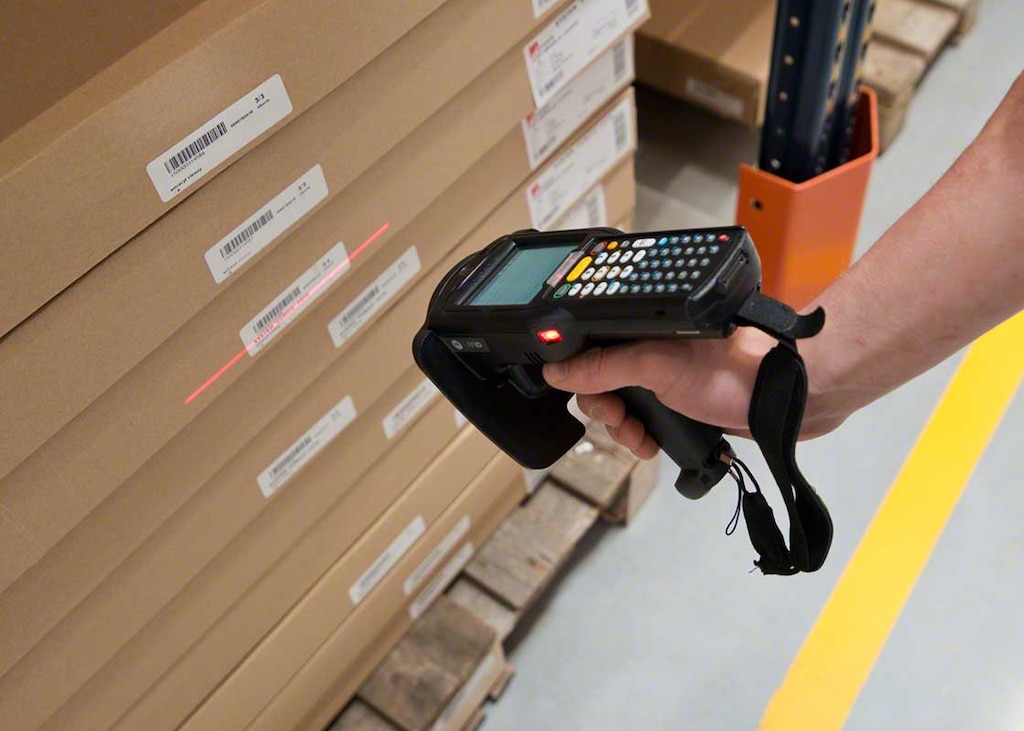
Rodzaje Poka-Yoke
Wyróżniamy cztery rodzaje Poka-Yoke:
- Wprowadzenie odpowiedniej kolejności w procesie. Jeżeli nie uda się jej zachować, nie można zakończyć zadania i przejść do kolejnego procesu.
- Informowanie. Prosta, czytelna i bezpośrednia informacja pomaga w bezbłędnej realizacji zadań.
- Grupowanie. Polega na przygotowaniu zestawów wszystkich materiałów i detali niezbędnych do wykonania danej czynności. Dzięki temu pracownicy nie muszą tracić czasu na szukanie potrzebnych elementów – wszystko mają ręką.
- Ograniczenia fizyczne wprowadzone w budowie lub sposobie funkcjonowania urządzeń, aby zapobiec pomyłkom. Dobrym przykładem są tutaj zmywarki do naczyń i kuchenki mikrofalowe, których nie da się uruchomić bez wcześniejszego zamknięcia drzwiczek lub wprowadzenia stosownych ustawień (temperatura, czas, program itp.).
Wszystkie wymienione praktyki mają na celu eliminację błędów przy powtarzalnych czynnościach lub procesach, w których łatwo o pomyłkę z braku wiedzy lub w wyniku chwilowego rozkojarzenia. Dzięki temu pracownicy zamiast tracić czas na usuwanie skutków błędów, mogą skupić się na wykonywaniu zadań.
Pięć przykładów Poka-Yoke w logistyce
Na początek zaznaczmy, że nie ma sztywnych reguł projektowania Poka-Yoke. Powodzenie przedsięwzięcia zależy od inwencji osób zaangażowanych w dany proces.
W dalszej części artykułu zaprezentujemy, jakie praktyki Poka-Yoke najczęściej stosuje się w magazynie. W branży logistycznej technika ta jest jednym z istotnych elementów tzw. Lean logistics, czyli metody nastawionej na optymalizację procesów generujących największą wartość dodaną celem ograniczenia kosztów.
Przykład 1: Określenie kolejności przy użyciu oprogramowania magazynowego
Informatyczny system magazynowy (WMS), np. Easy WMS firmy Mecalux, pozwala usprawnić procesy, kierując pracą magazynierów, którzy dzięki temu szybciej i wydajniej realizują powierzone im zadania.
WMS pełni w takim przypadku funkcję Poka-Yoke określającego kolejność – pracownicy kolejno wykonują zadania przesłane z systemu na terminal radiowy. Po otrzymaniu polecenia magazynier musi potwierdzić jego wykonanie, aby otrzymać następne.
Przykład 2: Informowanie za pomocą wskaźników „pick to light”
Kompletacja zamówień jest czynnością magazynową obarczoną największym ryzykiem błędu. Zmęczenie fizyczne magazynierów, a także podobieństwo produktów czy regałów mogą dodatkowo przyczynić się do popełnienia pomyłki (niekompletne zamówienia, pomylone artykuły, niewłaściwa liczba sztuk itd.).
Zastosowanie urządzeń świetlnych pick-to-light, które można zakwalifikować do grupy informacyjnych elementów Poka-Yoke, jest rozwiązaniem pozwalającym uniknąć błędów podczas kompletacji. Urządzenia te, za pomocą sygnałów świetlnych, wyraźnie wskazują operatorom produkty oraz konieczną do pobrania ilość. Ich funkcją jest eliminacja błędów ludzkich występujących podczas kompletacji.
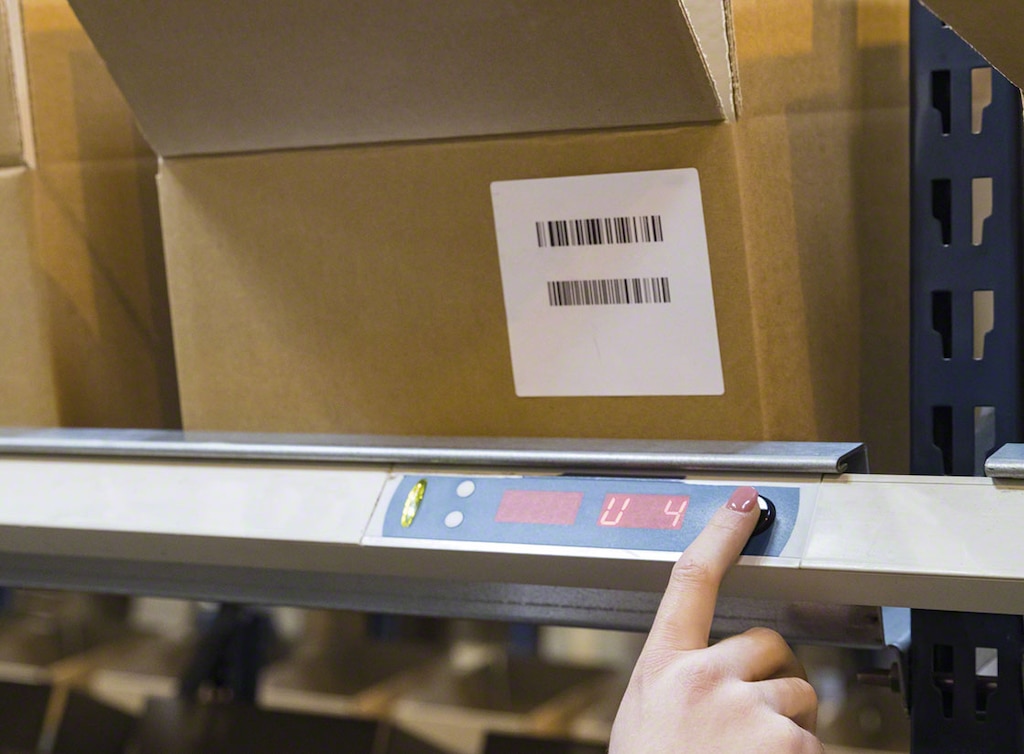
Przykład 3: Grupowanie produktów przy tworzeniu zestawów
W wielu magazynach wykonywany jest kitting, czyli proces kompletacji zestawów polegający na gromadzeniu poszczególnych elementów składowych produktu, które następnie przekazywane są innym operatorom w celu wytworzenia wyrobu gotowego.
W takim przypadku dobrym pomysłem jest zastosowanie Poka-Yoke z grupowaniem, czyli wcześniejsze przygotowanie wszystkich potrzebnych elementów na stanowiskach roboczych, aby pracownicy nie musieli szukać ich w magazynie.
Takie rozwiązanie pozwala znacznie usprawnić pracę i zwiększyć jej dokładność, ponieważ pracownicy mogą utworzyć gotowy zestaw bez konieczności opuszczania stanowiska.
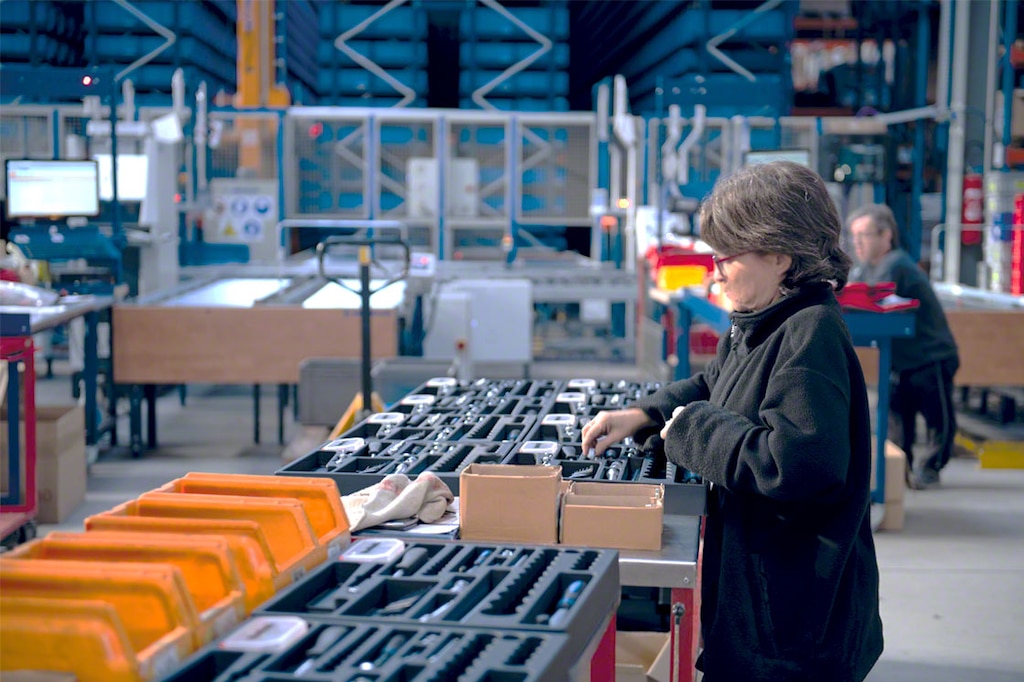
Przykład 4: Poka-Yoke fizyczne – ogrodzenia ochronne
Najczęściej spotykanym tego typu rozwiązaniem Poka-Yoke w magazynie są ogrodzenia ochronne, które mają na celu zapobieganie wypadkom.
Strefy pracy automatycznych urządzeń przeładunkowych, np. układnic, są zabezpieczone przed dostępem osób nieupoważnionych. W momencie wejścia do strefy roboczej ─ przez pomyłkę lub np. w celu konserwacji ─ urządzenie automatycznie się zatrzyma.
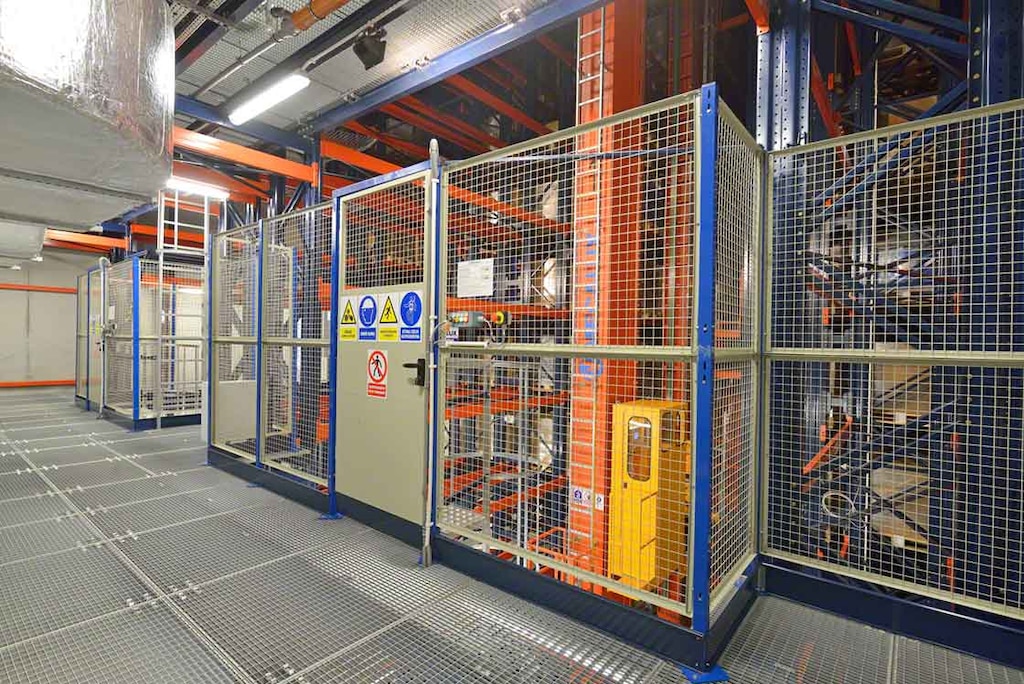
Przykład 5: Poka-Yoke fizyczne – wózki kompletacyjne
Innym przykładem fizycznego Poka-Yoke często stosowanego w magazynach są wózki do kompletacji zamówień. Ich rozmiary są zwykle dostosowane do wielkości produktów i zamówień.
Jeżeli w magazynie prowadzi się kompletację falową (tzw. wave picking), wózki dodatkowo podzielone są na tyle przegródek, ile zamówień obsługiwanych jest w pojedynczej fali. Takie rozwiązanie pozwala uniknąć pomyłek.
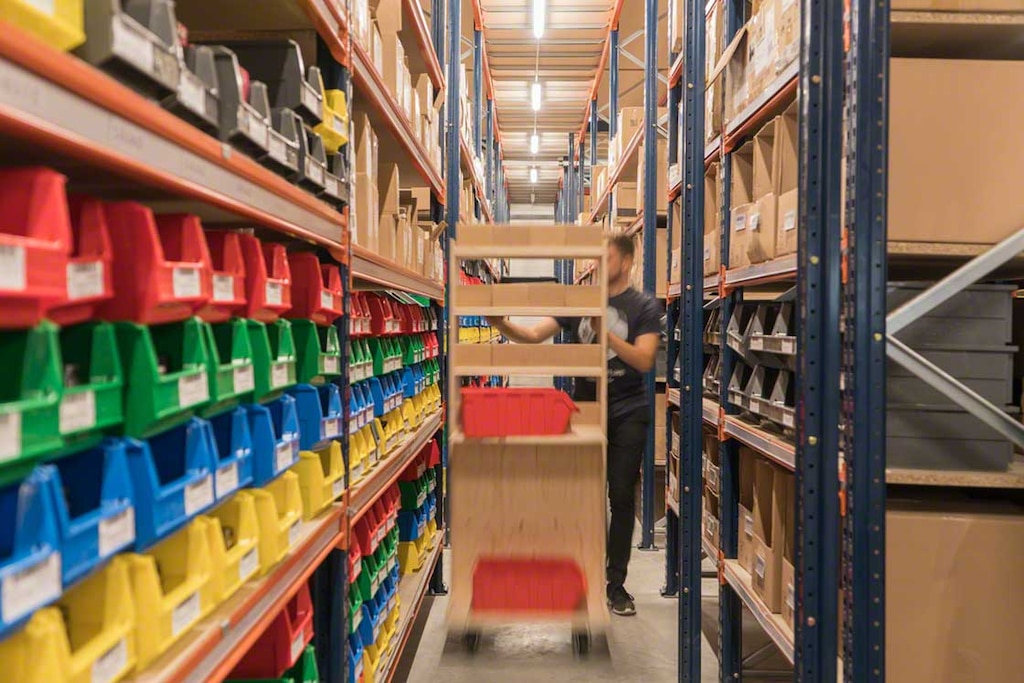
Eliminacja błędów dla poprawy jakości
Poka-Yoke to określenie szeregu technik pozwalających uniknąć błędów w powtarzalnych czynnościach. Efekty ich wdrożenia możemy zaobserwować w najbliższym otoczeniu w postaci przedmiotów i urządzeń, którymi posługujemy się na co dzień, a także w miejscu pracy, np. magazynie czy zakładzie produkcyjnym.
Poka-Yoke ma na celu poprawę jakości procesów, usług i gotowych wyrobów, mogących zwiększyć zadowolenie klientów.
Mecalux posiada wieloletnie doświadczenie w projektowaniu rozwiązań magazynowych pozwalających uprościć pracę i poprawić wydajność. Skontaktuj się z nami, a pomożemy Ci zaprojektować wydajny magazyn wyposażony w systemy umożliwiające ograniczenie ryzyka pomyłki.