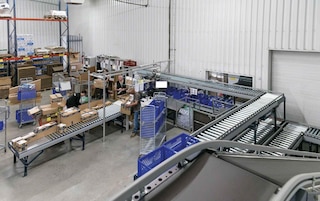
Brak zapasów w magazynie – jak zapobiec jego występowaniu?
Brak zapasów w magazynie (ang. out of stock (OOS), stockout) to sytuacja, w której z powodu nieefektywnego zarządzania składowanym asortymentem dochodzi do wyczerpania się konkretnego produktu na stanie magazynowym.
Sprawia to, że niemożliwe staje się spełnienie zamówienia klienta, co w konsekwencji będzie miało negatywne przełożenie na działalność przedsiębiorstwa: straty finansowe spowodowane zaprzepaszczeniem szansy sprzedażowej, a także pogorszenie się wizerunku marki oraz prawdopodobieństwo utraty lojalności klienta, które mogą doprowadzić do dokonania zakupów u konkurencji.
W tym artykule przyjrzymy się przyczynom i skutkom występowania braku zapasów w magazynie oraz rozwiązaniom, które mogą im zapobiec.
1. Wskaźnik braku zapasów
Skuteczne zarządzanie asortymentem magazynowym to umiejętność zachowania idealnego balansu pomiędzy zapotrzebowaniem na produkty a ich dostępnością. Brak zapasów w magazynie oznacza, że doszło do jego zachwiania.
Wskaźnik braku zapasów jest jednym z KPI (kluczowych wskaźnik efektywności) stosowanych w logistyce magazynowej, który pozwala ocenić efektywność obrotu towarów w magazynie. Oblicza się go według następującej formuły
Wskaźnik braku zapasów = liczba niezrealizowanych zamówień / całkowita liczba zamówień x 100
2. Jakie są konsekwencje braku zapasów w magazynie?
Bezpośrednim skutkiem problemów z dostępnością asortymentu jest wzrost kosztów logistycznych. Współcześnie firmy są o wiele bardziej narażone na ten problem, ponieważ składowanych jest coraz więcej różnorodnych referencji. Jedną z metod ograniczenia kosztów magazynowania oraz uniknięcia ryzyka braku zapasów w magazynie jest wdrażanie w organizacjach strategii lean, jak na przykład just-in-time lub cross-docking.
Konsekwencje występowania deficytu produktów w magazynie możemy podzielić na dwie grupy. Pierwsza z nich to straty o wartości obiektywnej, czyli inaczej mówiąc mierzalnej. Są to wcześniej wspomniane większe koszty finansowe czy zmniejszenie obrotu towarami.
Drugą grupę stanowią straty o wartości subiektywnej. Są one o wiele trudniejsze do zmierzenia, a dotyczą m.in.: odpływu klientów do konkurencji, która dysponuje odpowiednim zaopatrzeniem zdolnym spełnić ich potrzeby, lub utrata wiarygodności i rzetelności wizerunku marki w oczach konsumentów. Straty te są szczególnie dotkliwe i istotne z punktu widzenia firm prowadzących logistykę e-commerce.
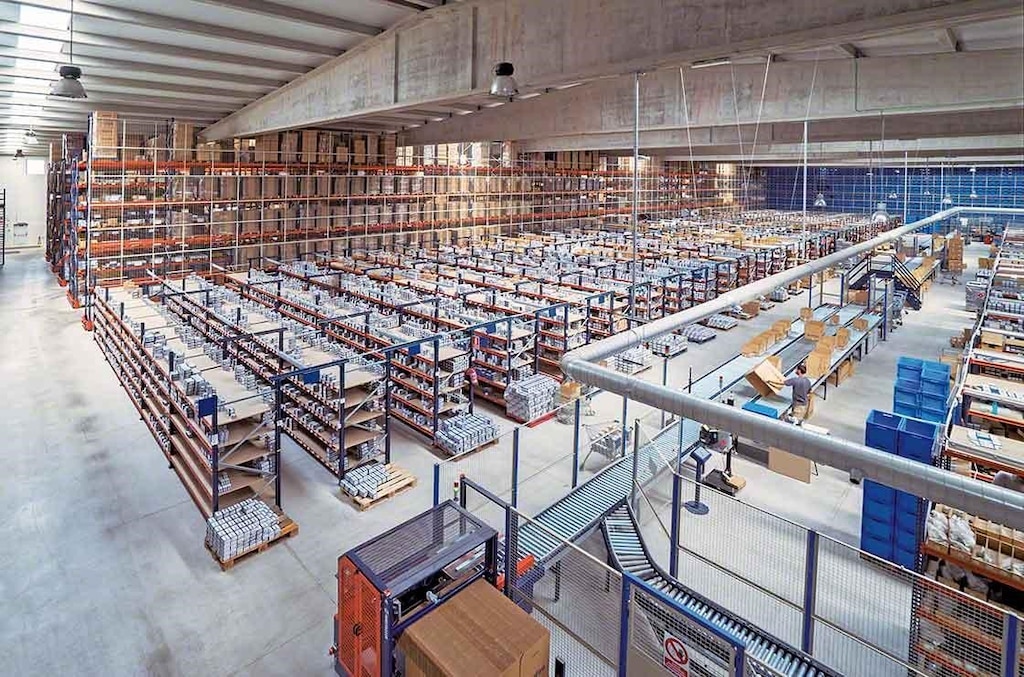
3. Przyczyny braku zapasów w magazynie
Choć nie istnieje jednoznaczna odpowiedź na tak postawione pytanie, to można pokusić się o stwierdzenie, że za brak zapasów w magazynie najczęściej odpowiedzialne są nieskuteczne planowanie oraz prognozowanie zarówno w sferze zarządzania procesami magazynowymi, jak i składowanymi zapasami.
Poniżej zebraliśmy najważniejsze oraz najczęściej występujące przyczyny braku zapasów w magazynie:
- nagły wzrost popytu na produkt: nieprzewidziane wystąpienie zwiększonego zapotrzebowania na artykuł będzie mieć wpływ zarówno na produkcję, jak i dystrybucję, co przełoży się na zmianę lead time, a w konsekwencji może doprowadzić do wystąpienia deficytu towaru w magazynie;
- błędne prognozy zapotrzebowania: prognozy popytu muszą być przeprowadzane na dużej ilości wiarygodnych danych, wszelkie nietrafione szacunki będą mieć bezpośredni wpływ na sposób zarządzania zapasami oraz wolumen składowanych w magazynie produktów;
- niezgodność w stanie zapasów: brak zapasów w magazynie może być konsekwencją niezgodności danych inwentaryzacyjnych z rzeczywistym stanem towarów na regałach;
- opóźnienie w dostawach: problemy z dostarczeniem produktów do magazynu mogą przełożyć się na ich niedostępność dla klienta;
- brak surowców: w przypadku fabryk brak lub opóźnienie w dostawie surowca może spowolnić lub nawet wstrzymać cały proces produkcyjny;
- czynnik ludzki: może wystąpić na różnych etapach łańcucha dostaw lub produkcyjnego.
4. Jak uniknąć pustych półek regałowych w magazynie?
– Większa skuteczność prognoz zapotrzebowania
Dzisiejszy rynek charakteryzuje się bardzo dużą liczbą zmiennych, które wpływają na sprzedaż produktów. Stąd niezwykle istotne jest stosowanie skutecznych narzędzi analitycznych umożliwiających zmaksymalizowanie trafności przygotowywanych prognoz. Big data w logistyce odgrywa coraz istotniejszą rolę i pozwala przekuć na korzyść przedsiębiorstwa informacje uzyskane dzięki danym, które są generowane na każdym etapie łańcucha dostaw.
Oprócz prowadzenia zaawansowanej analityki warto również pamiętać o następujących kwestiach:
- w każdej prognozie należy uwzględnić margines błędu,
- obowiązkowa jest znajomość cyklu życia każdego produktu,
- wymagane jest określenie sezonowych szczytów sprzedażowych i planowanie z wyprzedzeniem przebiegu procesów magazynowych w trakcie ich trwania,
- sporządzane prognozy powinny być krótkoterminowe.
– Odpowiednia infrastruktura technologiczna i informatyczna
Pozytywny wpływ oprogramowania informatycznego na kontrolę i optymalizację przepływów logistycznych został już wielokrotnie potwierdzony. Z uwagi na wysokie zaawansowanie i złożoność realizowanych procesów, firmy wdrażają dwa typy systemów:
- system ERP stanowiący podstawę pracy przedsiębiorstwa,
- system WMS lub oprogramowanie zarządzające flotą transportową, które współpracują bezpośrednio z systemem ERP.
Głównym celem ich zastosowania jest pełna kontrola nad zapasami na przestrzeni całego łańcucha dostaw. Bezbłędne i na bieżąco aktualizowane dane na temat towarów minimalizują ryzyko pojawienia się pomyłek oraz strat. Warto także wspomnieć, że obecne systemy WMS dysponują funkcjonalnościami, których zadaniem jest niezwłoczne wysyłanie ostrzeżeń w przypadku wykrycia zapasów wymagających uzupełnień.
– Regularne kontrole KPI dotyczących zarządzania zapasami
Wskaźniki KPI dotyczące zarządzania towarami wykorzystywane są w celu zidentyfikowania nieskutecznych procesów oraz pomagają w zapobieganiu występowania braku zapasów w magazynie. Oto trzy kwestie w tym względzie, które należy wziąć pod uwagę:
- moment odnowy zapasu: np. sytuacja, w której do dostawcy powinno zostać wysłane zlecenie w sprawie uzupełnienia produktu. Punkt ten powinien być na bieżąco monitorowany, ponieważ wpływa na minimalny stan zapasu, jaki powinna posiadać firma;
- wskaźnik rotacji zapasów: dzięki jego zastosowaniu firma uzyskuje informacje, ile razy nastąpił obrót zapasami w magazynie w danym przedziale czasowym. Monitorowanie tego wskaźnika pozwala określić m.in. wymaganą ilość magazynowanego towaru;
- zapas buforowy: jest to ilość zapasów „awaryjnych”, które muszą być zawsze dostępne w magazynie w przypadku wystąpienia nieprzewidzianych sytuacji (np. opóźnienia w dostawie), dzięki czemu nadal będzie możliwe zrealizowanie zamówień klientów.
– Znaczenie inwentaryzacji ciągłej
W wielu przypadkach brak zapasów w magazynie spowodowany jest nieaktualnymi informacjami na temat stanu zapasów i ich lokalizacji na półkach regałów magazynowych. Z tego powodu przedsiębiorstwa decydują się na wdrażanie systemów zarzadzania magazynem, które umożliwiają przeprowadzanie inwentaryzacji ciągłej, czyli monitorowania towarów w czasie rzeczywistym.
System WMS na bieżąco aktualizuje informacje na temat składowanych produktów i ich położenia w strefie magazynowej. Digitalizacja magazynu udostępnia dane zarówno w skali makro, pozwalając monitorować przyjęcia, wydania i przepływ towarów, jak i mikro, umożliwiając analizę cyklu życiowego pojedynczej SKU.
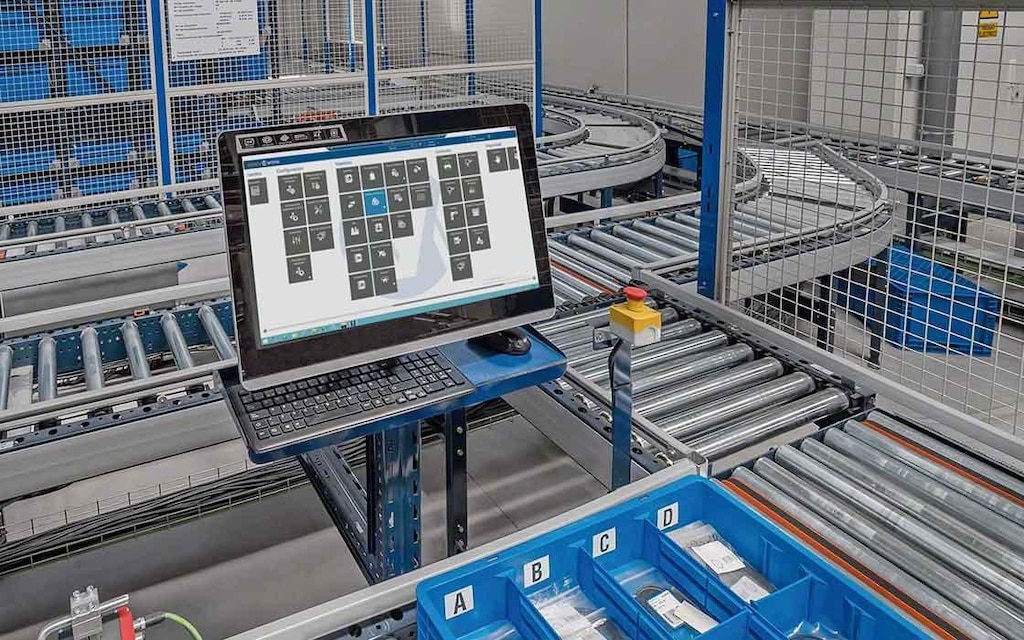
– Automatyzacja i procesy wewnątrzmagazynowe
Automatyzując procesy magazynowe, zmniejsza się ryzyko występowania strat w składowanych produktach spowodowanych na przykład ich uszkodzeniami, nieprawidłowym przechowywaniem lub obsługą, a nawet kradzieżą.
Oto kilka kwestii związanych z automatyzacją pozwalających ograniczyć występowanie strat, które w dłuższej perspektywie mogą doprowadzić do braku zapasów w magazynie:
- ograniczony dostęp do danych na temat zapasów: oprogramowanie magazynowe WMS (jak na przykład zaprojektowany przez Mecalux system Easy WMS) pozwala ograniczyć dostęp do konkretnych danych w zależności od użytkownika;
- automatyzacja obsługi ładunków: przekłada się na redukcję błędów oraz wypadków i optymalizuje przepływ towarów w magazynie;
- w pełni zautomatyzowana identyfikacja SKU i uzupełnianie danych w systemie: jako przykład niech posłuży stanowisko kontroli rozmiarów, wagi i stanu palet, które identyfikuje ładunki przyjmowane do magazynu i przesyła wszelkie niezbędne informacje do systemu zarządzania magazynem.
Jak widać z powyższego artykułu, brak zapasów w magazynie jest w dużej mierze wynikiem nieefektywnego zarządzania stanem magazynowym. W jego optymalizacji może pomóc zastosowanie odpowiednich rozwiązań technologicznych.
Firma Mecalux posiada wieloletnie doświadczenie w projektowaniu automatycznych systemów składowania oraz rozwoju i wdrażaniu autorskiego systemu zarzadzania magazynem Easy WMS. Ich współpraca umożliwia zwiększenie wydajności przeprowadzanych operacji logistycznych.
Jeśli chcesz uzyskać więcej informacji na temat rozwiązań Mecaluxu lub szukasz pomocy w obszarach logistyczno-magazynowych – skontaktuj się z nami. Nasi eksperci udzielą Ci wszelkich potrzebnych informacji.