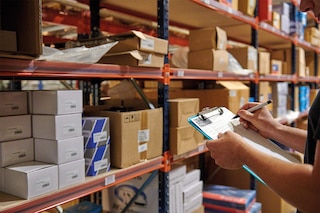
Różnice inwentaryzacyjne – czym są i jak im zapobiegać
Różnice inwentaryzacyjne stanowią poważny problem w logistyce. Niezgodność stanu zapasów fizycznie zgromadzonych w sklepie lub magazynie ze stanem zarejestrowanym w systemie komputerowym może prowadzić do poważnych strat finansowych.
W niniejszym artykule analizujemy, czym są różnice inwentaryzacyjne, a także omawiamy, jak je identyfikować we właściwym czasie, aby nie wpływały negatywnie na kompletację i wysyłkę zamówień.
Czym są różnice inwentaryzacyjne
Termin „różnice inwentaryzacyjne”, (ang. phantom inventory), dotyczy rozbieżności między zapasami fizycznie składowanymi w sklepie lub magazynie a zapasami zarejestrowanymi w systemie. Innymi słowy, są to produkty, które widnieją w bazie danych jako dostępne, lecz w rzeczywistości, najprawdopodobniej w wyniku błędu ludzkiego, nie znajdują się we wskazanej lokalizacji.
Taka niezgodność prowadzi między innymi do sytuacji, w których firma przyjmuje zamówienia, a następnie nie może ich dostarczyć klientom ze względu na brak zapasów. Operator zauważa niewystarczającą ilość towaru i komunikuje brak możliwości realizacji zamówienia dopiero na etapie kompletacji. Może to również skutkować problemami z zaopatrzeniem linii produkcyjnych w surowce, a w konsekwencji doprowadzić do wstrzymania produkcji danego artykułu.
Różnice stanu zapasów sprawiają, że w odpowiednim czasie nie zostaje złożone zlecenie zakupu, (punkt zamawiania, ang. reorder point), co prowadzi do braku zapasów w magazynie (w przypadku zbyt późnego złożenia zlecenia) lub do powstania zapasu nadmiernego (w przypadku zlecenia zakupu ze zbytnim wyprzedzeniem na podstawie stanu magazynowego niższego niż w rzeczywistości).
Różnice inwentaryzacyjne zdarzają się zarówno w magazynach, jak i sklepach i są zazwyczaj wynikiem błędów związanych z ręcznym zarządzaniem towarem. Najczęściej występują w obiektach obsługujących szeroką gamę pozycji asortymentowych, na przykład w firmach z sektora e-commerce lub u sprzedawców detalicznych.
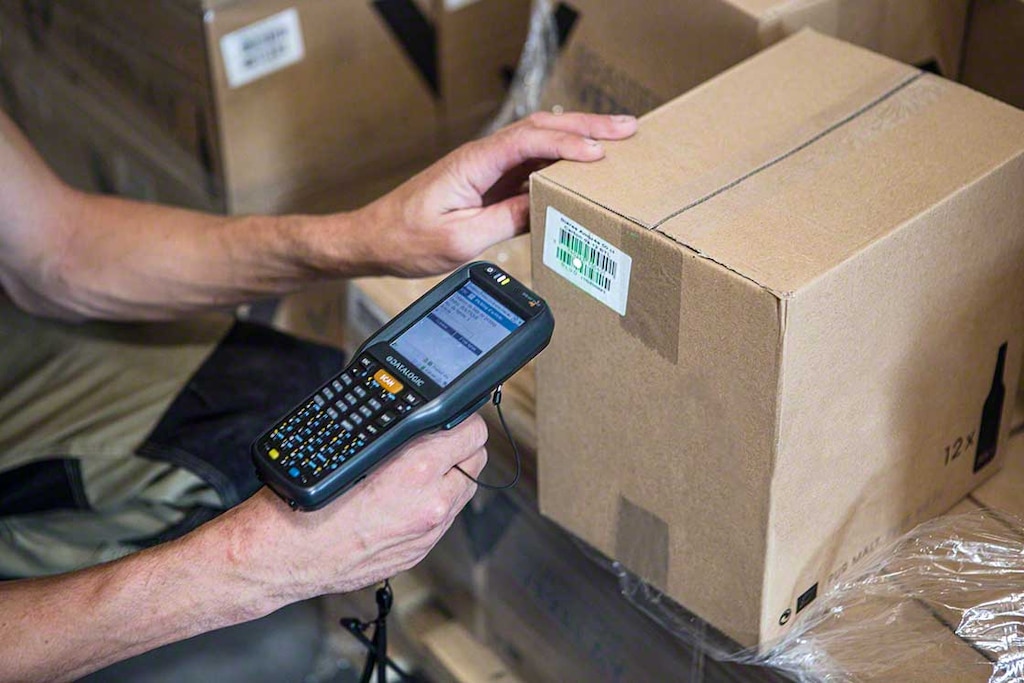
Różnice inwentaryzacyjne są wynikiem błędu ludzkiego na etapie przyjęcia lub kompletacji zamówień
Różnice inwentaryzacyjne stanowią poważne zagrożenie logistyczne, ponieważ ich bezpośrednim skutkiem jest brak zapasów w magazynie uniemożliwiający dostarczenie zamówienia w terminie i na warunkach uzgodnionych z klientem. Sytuacja ta może również utrudniać realizację zleceń produkcyjnych zgodnie z BOM-em materiałowym (ang. Bill of Materials) na przewidzianym poziomie.
Jak ograniczyć różnice inwentaryzacyjne?
Różnice inwentaryzacyjne zwykle wynikają z różnego rodzaju błędów człowieka: zmiana lokalizacji towaru bez zarejestrowania jej w systemie, zasłonięcie towaru innym ładunkiem, pobieranie niewłaściwych pozycji asortymentowych, wykonywanie pracy na pamięć i błędne odnotowanie rodzaju lub liczby produktów, wprowadzenie błędnych danych do systemu, kradzież itp. Jeżeli inwentaryzacja prowadzona jest za pomocą arkusza Excel, na kartce lub za pomocą podstawowego oprogramowania, najprawdopodobniej takie błędy wystąpią, prowadząc do powstania różnic inwentaryzacyjnych.
Wdrożenie zaawansowanego oprogramowania do zarządzania magazynem, takiego jak Easy WMS firmy Mecalux, umożliwia znaczne ograniczenie tego rodzaju pomyłek.
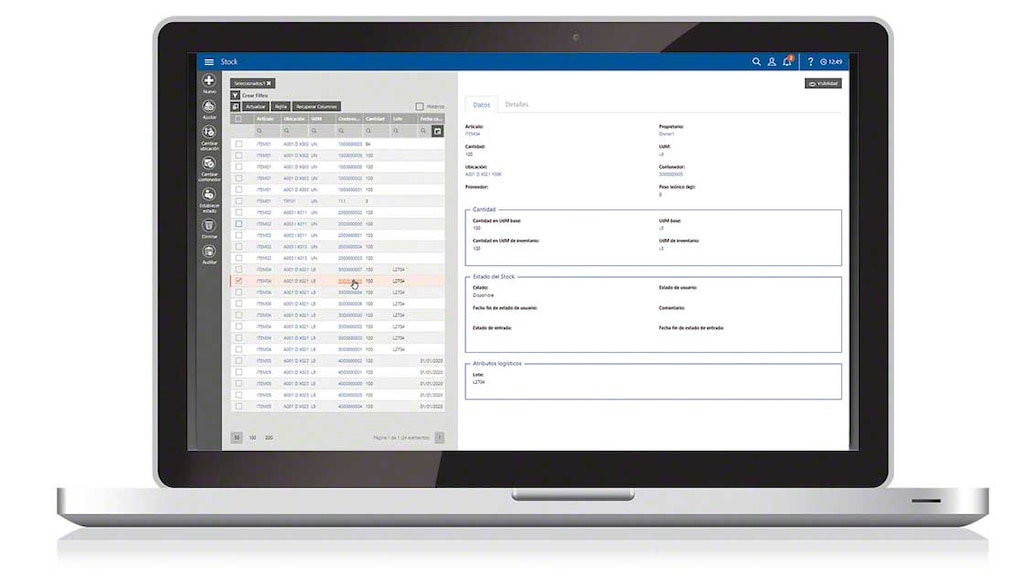
Easy WMS organizuje pracę operatorów i zapewnia jej prawidłowe wykonanie. Przykładowo podczas przyjęcia towaru oprogramowanie wysyła szczegółowe instrukcje dotyczące prawidłowej rejestracji otrzymanych pozycji asortymentowych, ich przeładunku, a następnie miejsca składowania. W ten sposób zapobiega ono pominięciu czynności, które mogłoby skutkować błędem. Odczytując kody kreskowe lub dokonując potwierdzenia w terminalu, operator poświadcza pobranie prawidłowego produktu i pozostawienie go w wyznaczonym miejscu.
Kolejnym etapem, na którym zwykle popełniane są błędy, jest kompletacja zamówień. Tu również automatyzacja zarządzania ma na celu minimalizację czynnika ludzkiego. Kierując poszczególnymi zadaniami operatora w prosty i intuicyjny sposób, technologie wspomagające proces kompletacji, takie jak pick-by-light czy pick-by-voice pozwalają wyeliminować ryzyko pojawienia się różnic inwentaryzacyjnych. Wystarczy, że magazynier będzie stosował się do poleceń przekazywanych przez urządzenie.
Bardziej zaawansowanym rozwiązaniem są wysoko wydajne stacje kompletacyjne. Produkty są składowane w pojemnikach, które układnica pojemnikowa automatycznie pobiera z regału i umieszcza na stanowisku roboczym obsługiwanym przez pracownika. Operator nie musi się nigdzie przemieszczać. Jego zadanie polega jedynie na wyjęciu wskazanej liczby sztuk towaru z dostarczonego mu pojemnika i umieszczenie ich w innym.
Wszystkie te rozwiązania mają na celu maksymalne uproszczenie wykonywanych czynności, aby zminimalizować ryzyko popełnienia błędu przez człowieka.
Automatyzacja – rozwiązanie pozwalające ograniczyć różnice inwentaryzacyjne
Oprogramowanie magazynowe WMS i systemy wspomagające proces kompletacji znacząco zmniejszają ryzyko popełnienia błędu. Jednak niemal całkowitą eliminację pomyłek mogą zapewnić wyłącznie magazyny automatyczne, w których obsługa ładunków odbywa się bez udziału operatorów. Praca personelu ogranicza się do zarządzania i nadzoru. Można to zaobserwować zwłaszcza w przypadku automatycznych magazynów paletowych.
W tego rodzaju obiektach, na etapie przyjęcia, każda paleta przechodzi przez stanowisko kontroli (PIE), którego zadaniem jest weryfikacja prawidłowego stanu towaru i potwierdzenie zgodności ze stanem wprowadzonym do systemu. Następnie system przenośników przemieszcza ładunek do magazynu automatycznego, gdzie układnica paletowa pobiera go i odkłada w wyznaczonej lokalizacji na regałach. W celu wydania towaru proces ten jest wykonywany w odwrotnej kolejności.
Wszystkie wspomniane operacje są wykonywane bez udziału człowieka i podlegają kontroli systemu WMS, który sprawdza, czy obsługiwany jest właściwy towar i kieruje jego przepływem w magazynie. Dzięki temu wystąpienie różnic inwentaryzacyjnych jest niemal niemożliwe.
Automatyzacja nie tylko eliminuje możliwość popełnienia błędów w zakresie zapasów, ale również znacznie zwiększa wydajność magazynu i pozwala uzyskać maksymalną pojemność składowania poprzez wykorzystanie wysokości obiektu i ograniczenie przestrzeni między regałami.
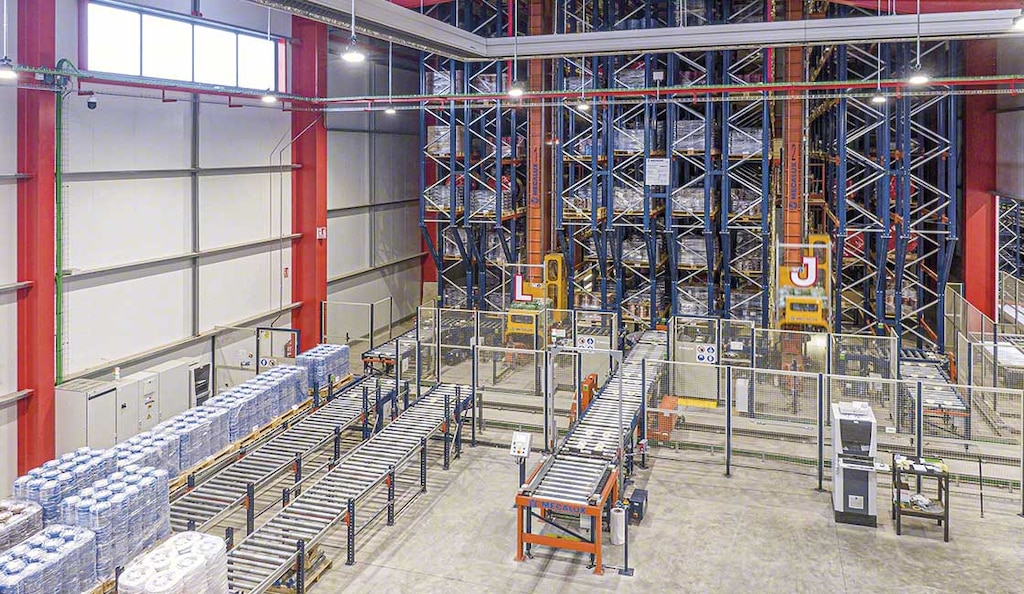
Całkowita eliminacja różnic inwentaryzacyjnych
Rozbieżności w stanie magazynowym są powodem wielu poważnych problemów. Z tego względu ręczne zarządzanie magazynem jest zastępowane elementami zautomatyzowanymi zapewniającymi niezawodność i bezpieczeństwo wszystkich procesów.
Wdrożenie systemu WMS to pierwszy krok w kierunku wyeliminowania różnic inwentaryzacyjnych. Oprogramowanie monitoruje wszystkie przepływy ładunków i kieruje czynnościami wykonywanymi przez operatorów podczas uzupełniania zapasów, zapobiegając pomyłkom. Idealnym rozwiązaniem pozwalającym jeszcze bardziej ograniczyć udział pracowników są automatyczne systemy magazynowe. Sprawują one pełną kontrolę nad składowanym towarem, uniemożliwiając jego utratę lub uszkodzenie. Automatyzacja wykonywanych procesów ma kluczowe znaczenie podczas zliczania zapasów, gdyż pozwala znacznie ograniczyć margines błędu.
Automatyczne rozwiązania magazynowe oraz system Easy WMS firmy Mecalux zapewniają maksymalną niezawodność podczas rejestracji zapasów, co umożliwia wyeliminowanie podstawowej przyczyny występowania różnic inwentaryzacyjnych. Skontaktuj się z nami, a przedstawimy Ci rozwiązanie najlepiej dostosowane do Twoich potrzeb.