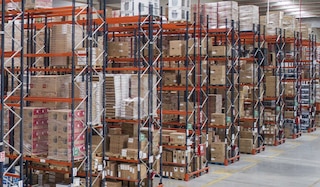
10 najczęstszych problemów logistycznych występujących w magazynie
Ewolucja w kierunku rynków cyfrowych i nowe wymagania klientów pociągają za sobą znaczne zwiększenie problemów logistycznych, w szczególności związanych z zarządzaniem magazynem.
Jakie problemy logistyczne są najbardziej powszechne? Wskazujemy dziesięć najczęściej występujących nieprawidłowości w magazynie i proponujemy kilka rozwiązań umożliwiających ograniczenie ich skutków.
1. Niewykorzystana przestrzeń
Brak przestrzeni magazynowej to jeden z głównych problemów, z którymi boryka się większość przedsiębiorstw. W takiej sytuacji, spowodowanej najczęściej rozwojem działalności, firmy są zmuszone do optymalizacji przestrzeni, jeżeli chcą uniknąć znacznych wydatków związanych z rozbudową obiektu lub wynajmem powierzchni logistycznej.
Jednym z najczęściej stosowanych rozwiązań w celu maksymalizacji przestrzeni bez powiększania dotychczasowej powierzchni jest wykorzystanie wysokości magazynu za pomocą wyższych regałów lub podestów i pomostów. Optymalizacja przestrzeni magazynowej jest możliwa dzięki instalacji akumulacyjnych systemów składowania, takich jak Pallet Shuttle, regały przesuwne Movirack czy regały wjezdne (drive-in).
2. Nieuporządkowanie towaru
Niewłaściwa organizacja składowanego towaru prowadzi do błędów i opóźnień podczas wyszukiwania konkretnych produktów, utrudniając realizację dostaw w wyznaczonym terminie. Uporządkowany magazyn to pierwszy krok w kierunku efektywności logistycznej.
Aby uniknąć nieładu, należy opracować skuteczną strategię rozmieszczenia ładunków, uwzględniając właściwości poszczególnych pozycji asortymentowych, dostępne systemy magazynowe i środki transportu bliskiego oraz poziom rotacji towaru.
Wykorzystanie w tym zakresie systemu WMS do zarządzania magazynem gwarantuje kompleksową kontrolę nad składowanymi zapasami dzięki synchronizacji poleceń przyjęcia i wydania towaru. System WMS m.in. automatyzuje proces rozmieszczania ładunków w magazynie (slotting) na podstawie ustalonych kryteriów i reguł.
3. Błędy podczas kompletacji
Pobieranie niewłaściwych artykułów lub mieszanie kilku zamówień w ramach jednego zlecenia pociąga za sobą negatywne skutki dla funkcjonowania logistyki magazynu i przyczynia się do zwiększenia nakładów poniesionych na logistykę odzysku (zwrotu towaru).
Błędy podczas kompletacji są bardzo kosztowne. Według niektórych badań ich średnie skutki finansowe szacuje się na ok. 17 euro na zamówienie.
Podczas tak złożonej czynności, jaką jest przygotowywanie zamówień, gdy operatorzy kompletują wiele zamówień obejmujących różne pozycje asortymentowe, rozwiązaniem umożliwiającym ograniczenie liczby błędów jest automatyzacja, która pozwala zarazem na zwiększenie liczby zamówień kompletowanych w magazynie w ciągu godziny.
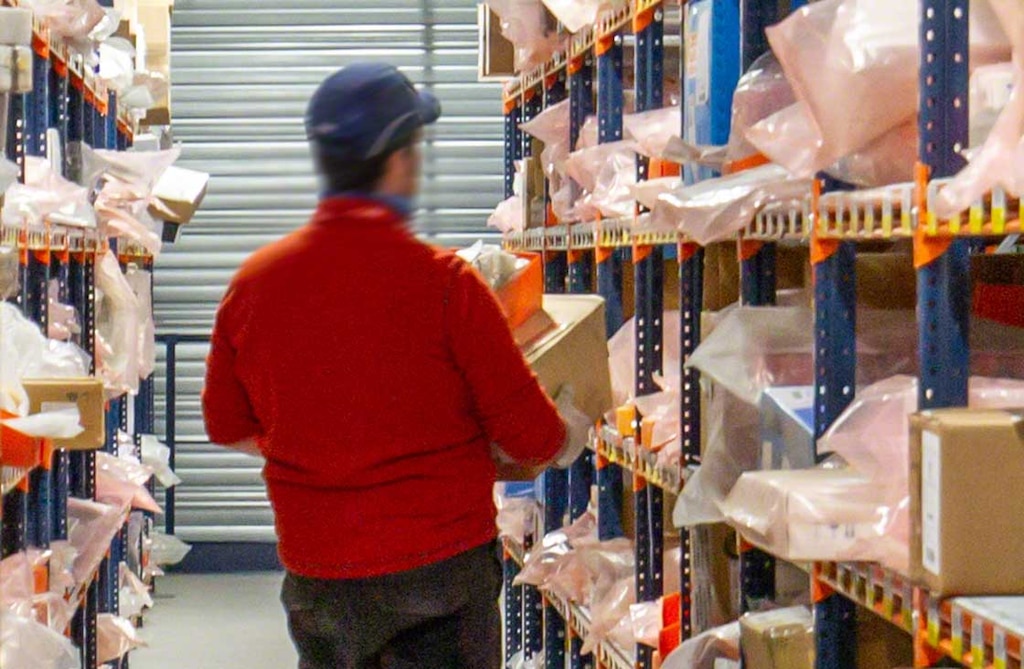
4. Brak systemu identyfikowalności produktów
W kontekście zintegrowanego łańcucha dostaw klienci i dostawcy chcą otrzymywać szczegółowe informacje na temat surowców wykorzystanych do wytworzenia artykułu oraz procesów produkcyjnych i logistycznych, którym produkt został poddany przed dostawą.
Identyfikowalność produktów, funkcja logistyczna umożliwiająca rejestrację i śledzenie każdego artykułu od momentu jego wyprodukowania po dostarczenie klientowi docelowemu, ma szczególne znaczenie m.in. w sektorze farmaceutycznym i rolno-spożywczym. Brak możliwości śledzenia może pociągać za sobą istotne problemy dla nabywców oraz dla samego dostawcy.
Wdrożenie oprogramowania logistycznego, takiego jak system WMS, gwarantuje identyfikowalność produktów od przyjęcia w magazynie do momentu wysyłki. Na rynku są dostępne także inne programy umożliwiające korzystanie z tej funkcji logistycznej, np. WMS do zarządzania produkcją, zaawansowana funkcja systemu Easy WMS firmy Mecalux. Moduł synchronizuje strefę zaopatrzenia ze strefą produkcji w celu monitorowania procesu produkcyjnego w magazynie.
5. Nieaktualny stan magazynowy
Znajomość i planowanie zapasów w magazynie to kwestie o nadrzędnym znaczeniu w celu utrzymania wydajności wszystkich czynności logistycznych. Brak bieżącej kontroli stanu magazynowego bądź zbyt mała częstotliwość inwentaryzacji może wywołać poważne skutki dla firmy, od błędów w zakresie rozmieszczenia produktów nawet po brak zapasów w magazynie.
W miarę rozwoju firmy i składowania coraz większej liczby pozycji asortymentowych w magazynie wdrożenie systemu WMS staje się niezbędne w celu zapewnienia aktualnych informacji na temat zapasów dostępnych w magazynie.
6. Błędy podczas obsługi towaru
Prawidłowa obsługa jednostek ładunkowych w magazynie to jeden z kluczowych aspektów warunkujących ograniczenie uszkodzeń towarów i zwiększenie wydajności. Należy zatem wyposażyć obiekt we właściwe urządzenia transportu bliskiego, zapewnić odpowiednie przeszkolenie operatorów w zakresie ich obsługi oraz zadbać o niezbędną konserwację.
Rozwiązaniem, które zagwarantuje optymalną obsługę ładunków, jest automatyzacja procesów logistycznych polegająca na zastąpieniu tradycyjnych urządzeń transportu bliskiego, w tym ręcznych wózków paletowych i wózków widłowych przenośnikami oraz układnicami w celu przyspieszenia przepływu towaru pomiędzy poszczególnymi procesami logistycznymi.
Ponadto należy pamiętać o odpowiednim ułożeniu towarów na jednostce ładunkowej (zwykle paleta lub pojemnik) w celu zagwarantowania stabilności i stateczności ładunku podczas wszelkich czynności wykonywanych w magazynie.
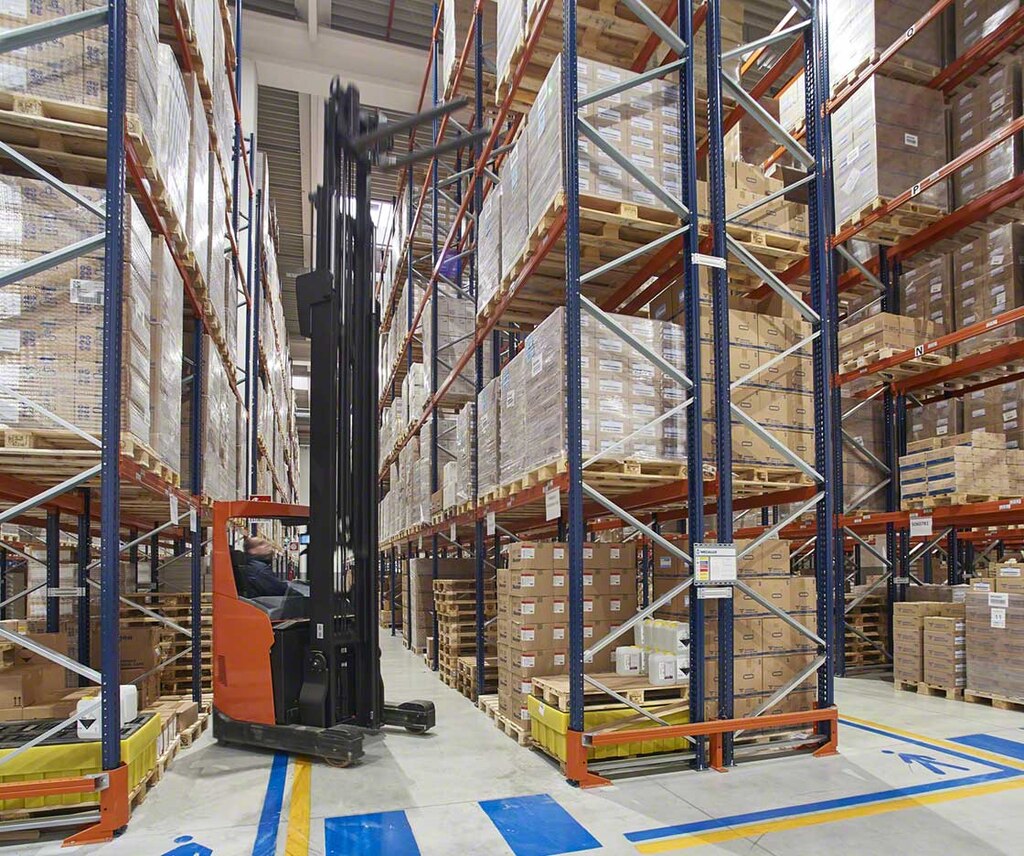
7. Opóźnienia wysyłki
Wysyłka towaru stanowi ostatni proces, któremu poddawany jest produkt przed wydaniem z magazynu, czy to do klienta docelowego, czy też do innego centrum dystrybucyjnego lub produkcyjnego.
Aby skutecznie przeprowadzić ten etap, zaleca się zaplanowanie dostaw, sprawną konsolidację towaru, prawidłową weryfikację niezbędnej dokumentacji na potrzeby wysyłki oraz szybki i bezpieczny załadunek towaru.
System zarządzania magazynem potrafi zgrupować zamówienia m.in. stosownie do tras dostawy, rodzaju pojazdu, klienta lub priorytetu wysyłki.
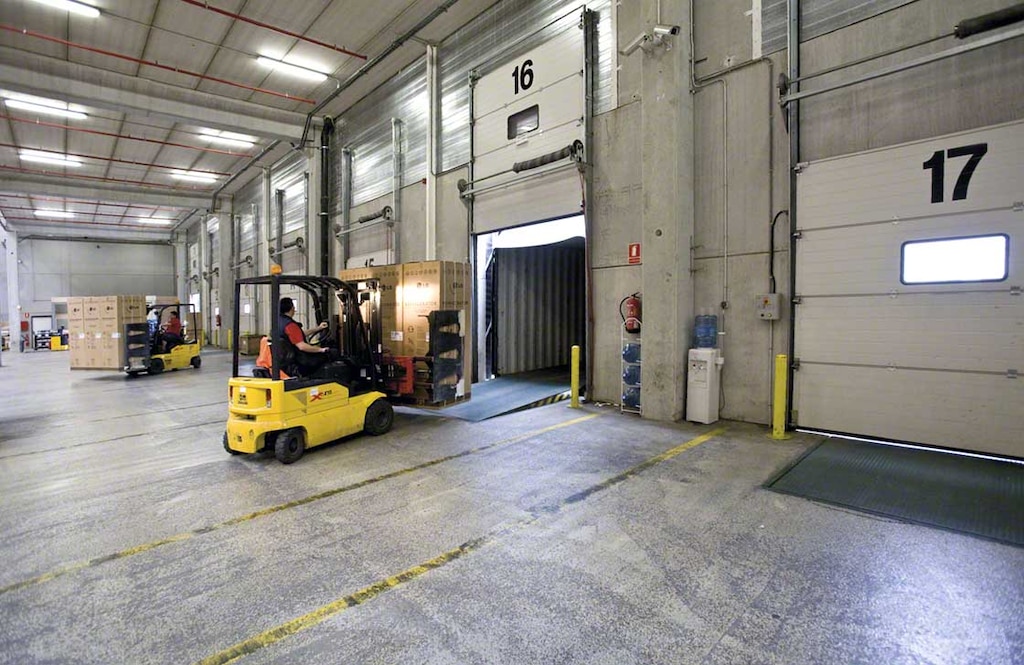
8. Niedostateczne oznakowanie magazynu
W przestrzeni, w której jednocześnie znajdują się operatorzy, ładunki i urządzenia transportu bliskiego, oznakowanie magazynu jest wymogiem niezbędnym. Oznaczenia powinny znajdować się w odpowiednich miejscach i być wyraźnie widoczne zarówno na posadzce, jak i na regałach czy elementach konstrukcji, aby spełnić wymogi w zakresie bezpieczeństwa, minimalizując ryzyko wypadku.
Źródłem przepisów nakładających obowiązek oznakowania magazynu jest dyrektywa Rady 92/58/EWG, która określa sposób wykonania oznakowania w obiekcie magazynowym. Znaki mogą mieć różne kolory, symbole i kształty w zależności od specyfiki oraz rodzaju przekazywanego komunikatu.
9. Nieprawidłowe KPI logistyczne
Najlepszym narzędziem umożliwiającym ciągłe doskonalenie procesów magazynowych są wskaźniki wydajności, czyli KPI logistyczne (Key Performance Indicators). Na podstawie zgromadzonych danych można monitorować wydajność poszczególnych czynności w celu zidentyfikowania obszarów wymagających poprawy.
KPI logistyczne umożliwiają pomiar wszystkich operacji prowadzonych w magazynie, takich jak m.in.: przyjęcie towaru, magazynowanie, kompletacja zamówień, zarządzanie zapasami, wysyłki, dostawy, transport i obsługa zwrotów. W przypadku nieprawidłowego wykorzystania wskaźników lub skupienia uwagi na analizie niewłaściwych KPI identyfikacja pozytywnych lub negatywnych zmian i podjęcie odpowiednich działań w celu osiągnięcia efektywności logistycznej będą znacznie utrudnione.
Zastosowanie odpowiedniego programu, takiego jak Supply Chain Analytics Software opracowanego przez firmę Mecalux, umożliwia monitorowanie całej działalności magazynu i kalkulację najważniejszych KPI logistycznych w celu ich analizy.
10. Brak integracji danych w przedsiębiorstwie (ERP)
Kierownik magazynu powinien mieć możliwość koordynacji działań z pozostałymi działami firmy, aby zrealizować cel działalności logistycznej, jakim jest dostarczenie zamówienia w wyznaczonym terminie i w formie uzgodnionej z klientem.
W tym celu stworzono system ERP (Enterprise Resourcing Planning) łączący rozmaite rodzaje oprogramowania, w tym logistyczne, i koordynujący pracę wielu działów firmy m.in. księgowości, marketingu, działu handlowego itp.
Nieprawidłowa koordynacja między magazynem i działem handlowym może prowadzić do błędnych lub niekompletnych zamówień, co pociąga za sobą poważne skutki finansowe dla firmy.
Korzyści płynące z usprawnienia magazynu
Automatyzacja operacji oraz zarządzania magazynem za pomocą systemu WMS to najlepsza strategia umożliwiająca wyeliminowanie błędów w magazynie oraz znaczne usprawnienie jego pracy.
Jeżeli dostrzegasz któryś z wymienionych problemów w swoim magazynie lub jeśli chcesz zautomatyzować zarówno składowanie, jak i zarządzanie centrum dystrybucji, skontaktuj się z firmą Mecalux. Zespół ekspertów pomoże Ci rozwiązać pojawiające się problemy, zapewniając maksymalną wydajność prowadzonych procesów logistycznych.