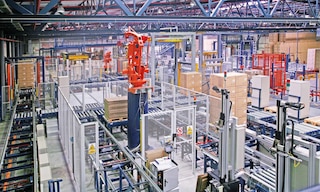
25 wskazówek jak poprawić bezpieczeństwo w logistyce
Stosowanie sprawdzonych wskazówek dotyczących bezpieczeństwa w logistyce pozwoli uchronić personel magazynu przed groźnymi w skutkach wypadkami, a także zapewnić optymalne warunki przechowywania towarów oraz sprawne działanie systemów składowania i przeładunku. Oprócz zagwarantowania zgodności z obowiązującymi przepisami BHP pozwoli też zwiększyć wydajność pracy w przyjaznym i odpowiednio dostosowanym środowisku roboczym.
Przypomnijmy pokrótce najważniejsze zagrożenia występujące w obiektach logistycznych:
- Upadek ładunków z regału w wyniku nieprawidłowego składowania, uderzenia w konstrukcję regałów itp.
- Upadki, poślizgnięcia, uderzenia, skaleczenia, pochwycenia kończyn i zderzenia z pojazdami, maszynami i urządzeniami przeładunkowymi pracującymi w magazynie.
- Pożary wywołane przez spontaniczny zapłon substancji łatwopalnych, nagromadzenie niebezpiecznych oparów, porażenia prądem i oparzenia w wyniku awarii instalacji elektrycznej itp.
W niniejszym artykule przytaczamy 25 wskazówek dotyczących bezpieczeństwa w logistyce i podpowiadamy, jak je stosować.
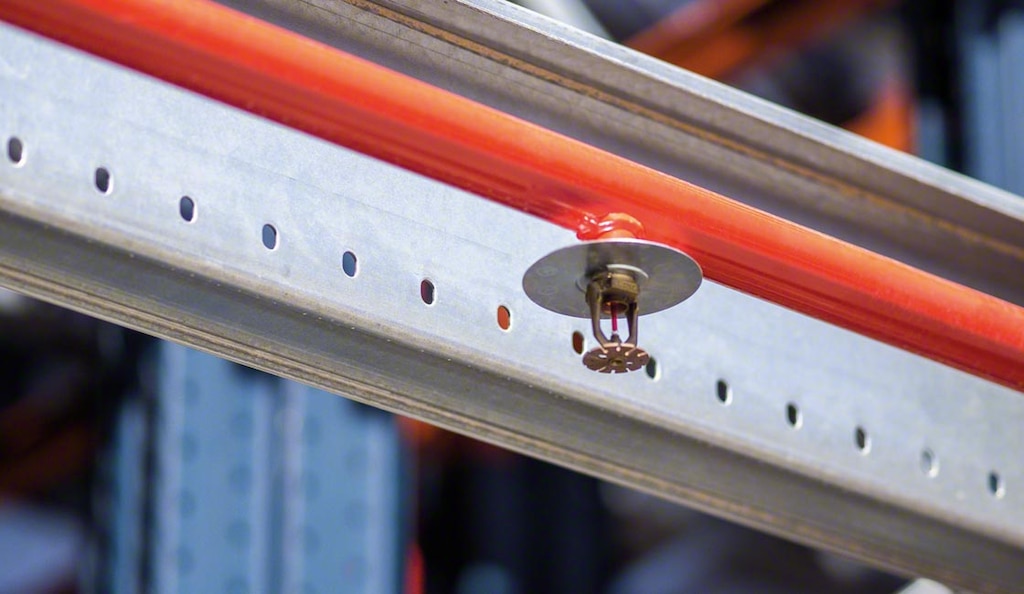
Jak poprawić bezpieczeństwo w logistyce
Zacznijmy od kilku wskazówek pozwalających znacznie ograniczyć ryzyko upadku ładunków z regału:
- Stosowanie odpowiednich środków ochrony indywidualnej. Środki ochrony indywidualnej (ŚOI) mają za zadanie chronić personel magazynu przed występującymi w miejscu pracy zagrożeniami dla zdrowia. Do najczęściej stosowanych środków ochrony indywidualnej należą: kaski, rękawice, gogle, obuwie oraz nauszniki i zatyczki do uszu.
- Przestrzeganie terminów corocznego przeglądu technicznego systemów składowania. Norma PN-EN 15635 nakłada na właściciela magazynu obowiązek zgłoszenia regałów magazynowych do corocznego przeglądu technicznego, przeprowadzanego przez specjalistów, którzy oceniają stan poszczególnych elementów instalacji.
- Przestrzeganie udźwigu regałów i maksymalnej wielkości ładunków. Każdy system składowania ma określone dopuszczalne obciążenie oraz wymiary jednostek ładunkowych.
- Przebudowa tylko za zgodą dostawcy. Regały są montowane przez specjalistów z uwzględnieniem wszystkich szczegółów technicznych istotnych z punktu widzenia bezpieczeństwa. Dlatego zdecydowanie odradzamy wprowadzanie jakichkolwiek zmian w ich konstrukcji bez wcześniejszego uzgodnienia z dostawcą systemu.
- Zapoznanie się z tabliczką znamionową i przestrzeganie opisanych na niej parametrów. Tabliczka znamionowa udostępniona przez dostawcę zawiera wszystkie istotne dane techniczne instalacji. Należy ją umieścić w dobrze widocznym miejscu i okresowo sprawdzać zgodność informacji ze stanem faktycznym.
- Kontrolowanie stanu palet. Tę czynność można zautomatyzować przy użyciu odpowiedniego stanowiska kontroli wejściowej, aby mieć stuprocentową pewność, że towary i palety nadają się do użytku wewnątrz obiektu i nie spowodują groźnych w skutkach wypadków.
- Prawidłowy załadunek palet. Aby uniknąć przypadkowego zsunięcia się towarów i zapewnić odpowiednią stabilność konstrukcji, należy pamiętać o prawidłowym przygotowaniu palet do składowania i transportu.
- Wyposażenie regałów w stosowne zabezpieczenia. W ofercie dostępnych jest wiele różnych osłon regałów, które mają za zadanie chronić konstrukcję przed przypadkowymi uderzeniami i zapewnić jej integralność. Do najczęściej stosowanych elementów należą osłony słupów mocowane do posadzki oraz osłony boczne, które chronią dolne partie regałów.
- Montaż siatek zabezpieczających. Te elementy mocuje się w tylnej części regałów przyległych do strefy roboczej lub strefy ruchu, aby zapobiec upadkowi ładunków. Należy je również zamontować w dolnej części przejść awaryjnych.
Równie istotne są zalecenia pozwalające do minimum ograniczyć ryzyko związane z poruszaniem się po magazynie oraz obsługą maszyn i urządzeń:
- Prawidłowe oświetlenie magazynu. Odpowiednie oświetlenie pozwala zmniejszyć ryzyko wypadków. Całe wyposażenie magazynu powinno być dobrze widoczne, co pozytywnie wpływa na bezpieczeństwo pracowników i sprzętu.
- Stosowanie ogrodzeń ochronnych. Ogrodzenia wokół automatycznych magazynów lub stref pracy robotów chronią personel przed spadającymi materiałami. Ogrodzenia przemysłowe z kolei pozwalają wydzielić strefy o ograniczonym dostępie.
- Montaż luster przy skrzyżowaniach i korytarzach. Lustra poprawiają widoczność na skrzyżowaniach czy trasach przejazdu wózków widłowych i innych urządzeń przeładunkowych.
- Wyznaczenie przejść awaryjnych. Przejścia przebiegają w poprzek korytarzy między regałami i ułatwiają ewakuację w razie zagrożenia. Są niezbędne w przypadku bardzo długich korytarzy.
- Poprawne oznakowanie magazynu. Znaki informują pracowników o możliwych zagrożeniach, strefach ograniczonego dostępu, trasach przejazdu wózków widłowych, czy miejscach kompletacji i przygotowania zamówień. Do oznakowania magazynu wykorzystuje się kolorowe tablice o określonych kształtach.
- Ostrożna obsługa urządzeń przeładunkowych. Operatorzy wózków widłowych powinni zachować szczególną ostrożność, aby nie potrącić innych pracowników oraz by nie uderzyć w regały lub inne urządzenia.
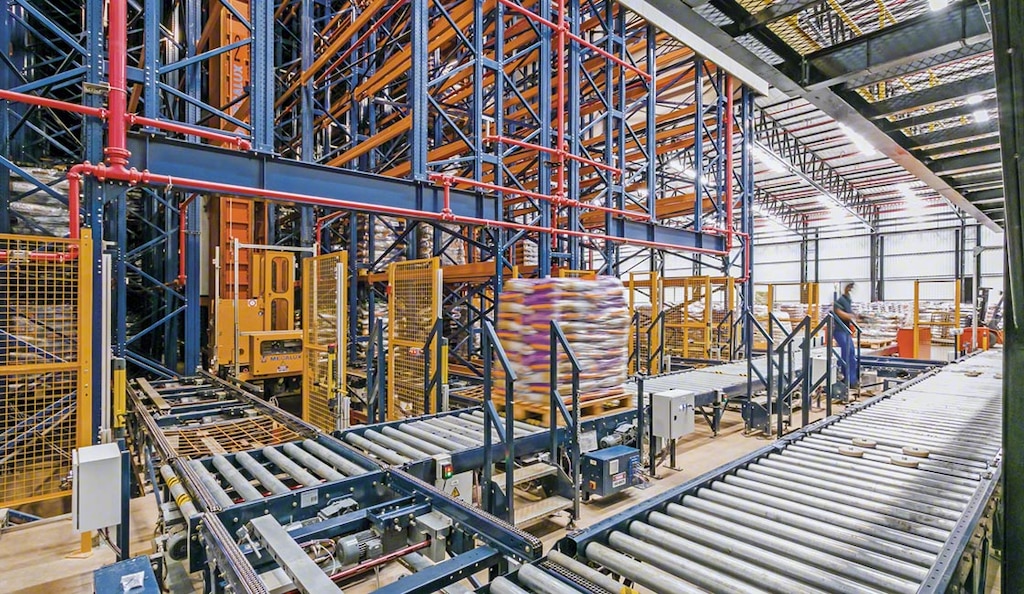
Warto też mieć na uwadze inne zalecenia bardziej ogólnej natury, ale nie mniej istotne z punktu widzenia bezpieczeństwa, jak konserwacja zapobiegawcza maszyn i urządzeń, szkolenie personelu czy egzekwowanie zasad BHP.
- Instalacja urządzeń przeciwpożarowych. Niezbędne środki ochrony przeciwpożarowej w każdym magazynie: ręczne (gaśnice i hydranty), automatyczne systemy wykrywania i sygnalizacji pożaru (np. czujki dymu), automatyczne systemy gaśnicze (instalacje tryskaczowe), systemy kontroli temperatury i oddymiania.
- Okresowa konserwacja maszyn. Ustanowienie kompleksowego programu konserwacji zapobiegawczej, obejmującej wszelkie bieżące naprawy urządzeń i systemów składowania celem uniknięcia groźnych w skutkach awarii, to najlepszy sposób na zwiększenie wydajności sprzętu i poprawę bezpieczeństwa obiektu.
- Dbanie o czystość i porządek w obiekcie. Praca w czystym i uporządkowanym otoczeniu jest bezpieczniejsza i przebiega sprawniej. Utrzymywanie porządku w magazynie, na stanowiskach roboczych i w strefach przechowywania towarów oznacza konieczność zapewnienia odpowiedniej czystości podłóg, sufitów, ścian, regałów, instalacji, oświetlenia i maszyn.
- Utrzymuj odpowiednią temperaturę w miejscu pracy. Zastosowanie automatycznych urządzeń w magazynie chłodniczym pozwala ograniczyć narażenie pracowników na szkodliwe dla zdrowia działanie niskich temperatur.
- Odpowiednie szkolenie personelu. Wszyscy pracownicy obiektu powinni wiedzieć, jak prawidłowo korzystać z dostępnych narzędzi oraz programów. Mecalux oferuje profesjonalne szkolenia, w trakcie których personel nauczy się obsługi systemu Easy WMS i dodatkowych modułów do projektowania i konfiguracji, a także pozna zasady działania innych programów oferowanych przez Mecalux.
Warto również rozważyć możliwość automatyzacji różnych procesów i czynności, co wyraźnie poprawi poziom bezpieczeństwa wielu zadań na co dzień realizowanych w magazynie:
- Stosowanie automatycznych systemów transportowych. Ryzyko groźnych w skutkach wypadków rośnie wprost proporcjonalnie do natężenia ruchu urządzeń przeładunkowych sterowanych ręcznie przez operatorów. Można temu zaradzić poprzez wdrożenie automatycznych urządzeń do transportowania ładunków, np. przenośników rolkowych, pojazdów sterowanych automatycznie (AGV) czy autonomicznych robotów mobilnych.
- Przygotowanie ergonomicznych stanowisk pracy. Stanowiska kompletacji powinny nie tylko umożliwiać wydajne przygotowanie zamówień do wysyłki, ale też zapewniać bezpieczną, sprawną i wygodną pracę. Dlatego warto wyposażyć je w ramiona hydrauliczne do przenoszenia cięższych ładunków oraz stoły z regulowaną wysokością blatu, przy których można komfortowo pracować w różnych pozycjach.
- Zastosowanie czujników bezpieczeństwa. Elementy te wykrywają ewentualne przeszkody na trasie ruchu urządzeń automatycznych, aby w porę zatrzymać system, zanim dojdzie do wypadku. Szczególnie zalecany jest montaż czujników na wszystkich rodzajach układnic czy na regałach przesuwnych Movirack.
- Automatyczne wyznaczanie ścieżek kompletacji. Odpowiednio zaawansowany system WMS potrafi automatycznie wyznaczać pracownikom optymalne ścieżki kompletacji zamówień. Dzięki temu nie muszą pokonywać kilkukrotnie tych samych tras między regałami w poszukiwaniu potrzebnych artykułów, a krótsze przejścia to mniejsze ryzyko wypadków.
- Automatyzacja przemieszczania ładunków wewnątrz regałów. Zastosowanie automatycznych systemów składowania, np. układnic paletowych, układnic pojemnikowych czy systemu Pallet Shuttle również pozwala znacząco ograniczyć natężenie ruchu wózków widłowych i paletowych w magazynie.
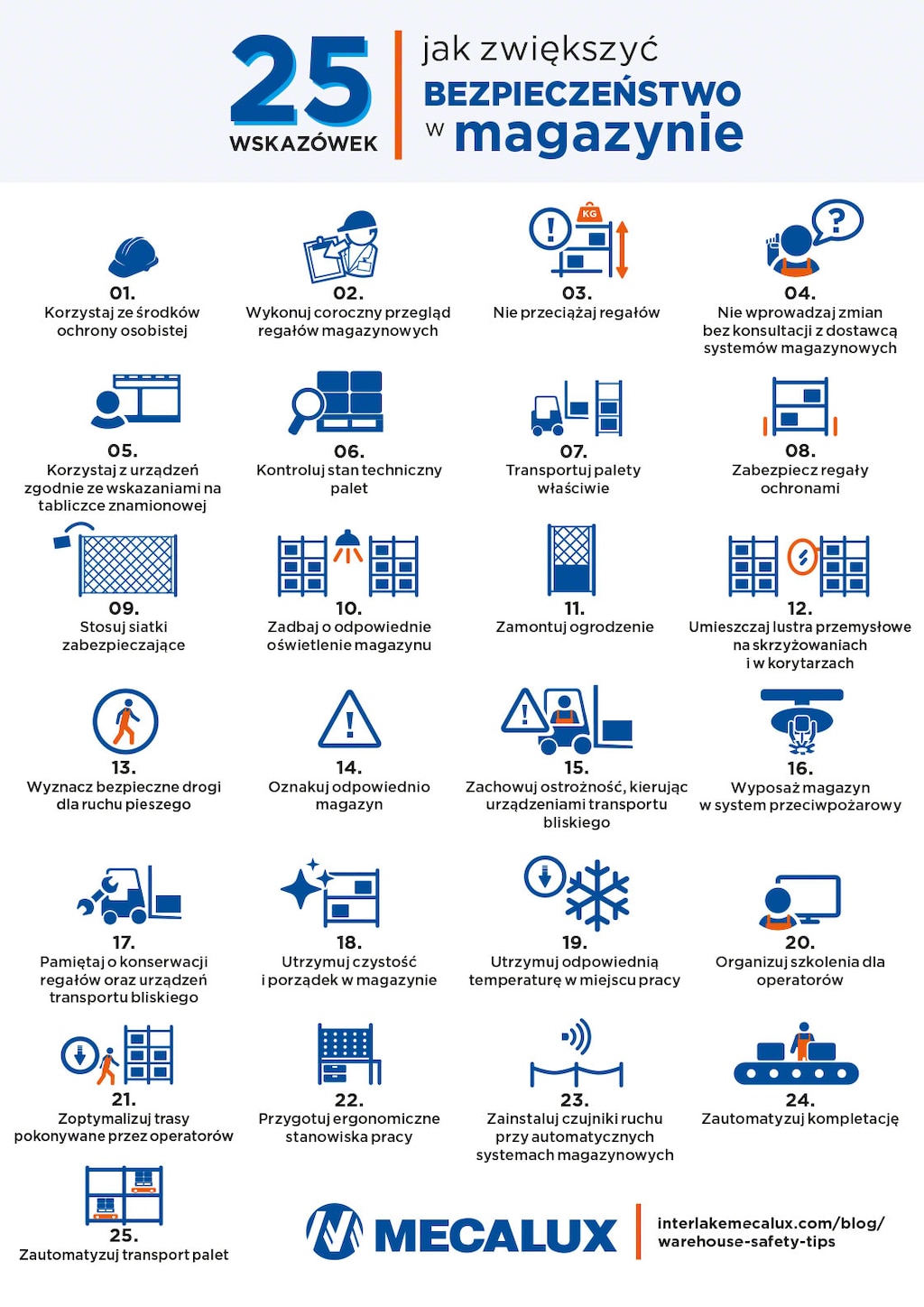
Droga do maksymalnego bezpieczeństwa w magazynie
Stosując się do wskazanych porad, poprawisz bezpieczeństwo personelu, magazynowanych ładunków oraz systemów transportu i składowania, zwiększając tym samym wydajność i jakość pracy całego przedsiębiorstwa.
Bezpieczeństwo w logistyce przekłada się na lepsze funkcjonowanie magazynu. Zdecydowanie ułatwia też utrzymanie konkurencyjności łańcucha dostaw, pozwalając jednocześnie wyeliminować kosztowne błędy i inne czynniki hamujące rozwój biznesu.
Jeżeli chcesz poprawić bezpieczeństwo w magazynie, skontaktuj się z nami. Nasi specjaliści dokładnie przeanalizują Twój obiekt i zaproponują możliwości poprawy jego działania i ograniczenia ryzyka wypadków.